Silicon
Critical Minerals and The Energy Transition
Navigating the Silicon Market
Silicon, integral to the technological fabric of contemporary society, stands at the forefront of the semiconductor industry, underpinning the operation of virtually all electronic devices. As the second most abundant element in the Earth's crust, its semiconductor properties are harnessed to create integrated circuits and transistors, marking the core of computers, smartphones, and many digital technologies. Beyond powering the electronics market, silicon's application extends to solar panels, where it plays a pivotal role in capturing solar energy, aligning with global sustainability efforts. The demand for silicon in semiconductors is fueled by the ever-expanding digital economy and the push towards renewable energy sources, positioning it as a cornerstone in the transition towards an electrified, sustainable future. This demand, however, brings to light challenges such as the environmental impact of silicon mining and the continuous pursuit of more efficient, sustainable production techniques. As the semiconductor industry progresses, the significance of silicon is magnified, emphasising the necessity for innovation in silicon recycling and reducing its environmental footprint. The ongoing evolution of silicon technology and its applications in semiconductors drives advancements in computing and energy and highlights the broader challenge of balancing technological growth with environmental stewardship.
An introduction to silicon
Silicon demand and end-uses
Silicon, the second most abundant element on Earth, has become a key material across a wide range of industries, from traditional manufacturing to advanced technology applications. The global silicon market is witnessing strong growth, driven by demand across diverse end-use sectors. This analysis explores current market dynamics, major applications, and the trends shaping the future of this critical material.
The silicon industry is expanding across several product segments, underpinned by technological advancements and an ever-widening scope of applications. The global silicon metal market is expected to grow steadily, while the downstream silicone segment, comprising products manufactured using silicon as a base material, is exhibiting even more dynamic growth. Meanwhile, the silicon wafer segment, essential for electronics and semiconductors, continues to expand at pace.
The electrification of vehicles and the digitisation of infrastructure are driving increased demand for semiconductors and power electronics, all of which rely heavily on silicon. The rise of artificial intelligence, high-speed computing, and data centre infrastructure is creating new, high-value markets for silicon-based components. AI and next-generation computing, in particular, are propelling the fastest-growing areas of the semiconductor industry. Silicon materials remain at the core of these systems, from processors to thermal management solutions. While traditional markets such as smartphones may be maturing, demand from data centres and AI infrastructure continues to grow rapidly.
Ongoing research and development is unlocking new applications for silicon-based materials, broadening their role in advanced manufacturing and product design. Technological improvements have enhanced the purity, efficiency, and cost-effectiveness of silicon production, making it increasingly accessible across a variety of sectors. The global push for low-carbon solutions is also boosting demand for silicon, particularly in areas such as solar energy, energy efficiency, and sustainable transport. Innovations in bio-compatible and hybrid silicone materials are gaining traction, further expanding the market’s reach.
The construction industry remains one of the largest consumers of silicon-based products, particularly silicones. Valued for their weather resistance, stability, and water-repellent properties, silicone materials are used in combination with marble, glass, concrete, steel, aluminium, and polymers in both residential and commercial projects.
Silicones serve as highly effective sealants and adhesives, particularly where durable and flexible bonding is required. Their resistance to extreme temperatures and harsh environmental conditions makes them ideal for use in infrastructure such as roads, bridges, pipelines, oil platforms, and industrial facilities. As global urbanisation and infrastructure development continue, construction remains a major driver of silicon demand.
Silicon is foundational to the electronics and semiconductor industry. High-purity silicon wafers form the basis of integrated circuits and microchips, powering nearly all modern electronic devices. The sector is forecast to grow significantly, with the global semiconductor industry expected to expand by nearly 10% in 2025, largely driven by applications in AI and data infrastructure.
Beyond semiconductors, silicon also plays a vital role as a thermal and electrical insulator in electronic components, shielding them from heat, moisture, and contamination. Silicon-based thermal interface materials (TIMs) are crucial for maintaining optimal performance in laptops, smartphones, and high-performance computing systems.
The automotive industry also accounts for a substantial share of silicon use. Aluminium-silicon alloys help reduce vehicle weight and improve fuel efficiency, while silicone-based materials are used for gaskets, seals, hoses, and vibration dampening to improve durability and comfort. As the global automotive sector transitions to electric vehicles (EVs), silicon’s importance is increasing further. It is now critical to EV battery systems, power electronics, and thermal regulation—making it indispensable to next-generation vehicle design.
Silicon is equally central to the renewable energy sector, particularly in solar photovoltaic (PV) technology. Crystalline silicon (c-Si) remains the dominant material in commercial solar cells, converting sunlight into electricity. As solar energy adoption accelerates worldwide, demand for silicon is set to rise accordingly. The potential to recover silicon from end-of-life solar panels is also gaining attention as part of emerging circular economy initiatives.
In healthcare, medical-grade silicones are valued for their biocompatibility, flexibility, and resistance to bacterial growth. These materials are widely used in implants, prosthetics, and medical devices that come into direct contact with human tissue. Rigorously tested for safety, silicone elastomers continue to meet the strict standards required for healthcare applications. As global healthcare infrastructure expands, so too does demand for advanced silicon-based solutions.
Silicon-based products also feature prominently in industrial manufacturing processes. Silicones are employed as lubricants, anti-foaming agents, coatings, adhesives, and additives across a broad range of industries—from offshore drilling to pulp and paper production. Their high-temperature resistance, dielectric strength, UV stability, and foam control properties make them ideal for use in seals, gaskets, and components exposed to extreme conditions. Silicon materials reliably perform above 100°C, maintaining structural integrity in demanding operational environments.
Looking ahead, advanced silicones, high-efficiency thermal materials, and emerging energy storage technologies represent promising new frontiers for silicon use. The development of bio-compatible and hybrid silicone materials is also opening new opportunities, particularly in healthcare, personal care, and wearable technology.
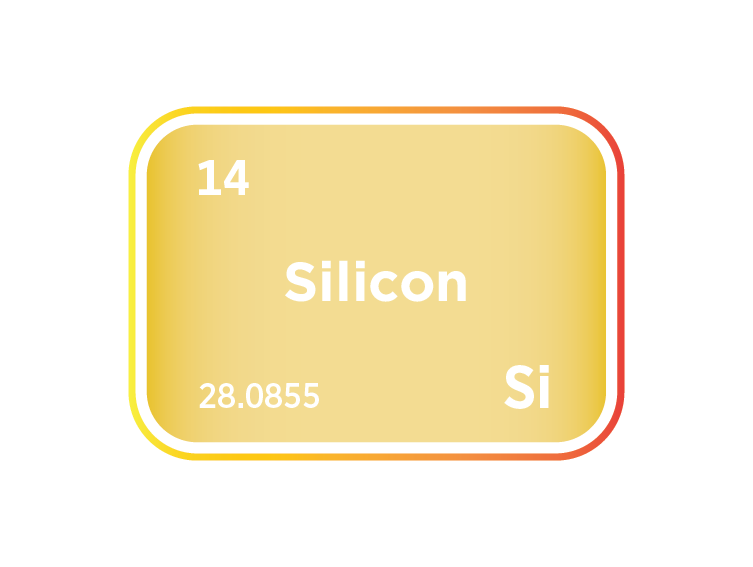
Silicon supply
China dominates global silicon production, accounting for the majority of both raw and refined output, and mining over five million tonnes annually. Other major producers include Russia, Brazil, Norway, and the United States, although the U.S. contributes only a modest share. While China leads in overall volume, countries such as Germany and the United States are key exporters of high-purity silicon, which is essential for semiconductor and solar panel manufacturing. Despite its production dominance, China remains the largest net importer of high-purity silicon, reflecting the scale of its domestic demand from advanced manufacturing sectors.
Silicon wafer production, a critical step in semiconductor fabrication, is primarily concentrated in Japan, Taiwan, Germany, and South Korea. China accounts for a relatively small portion of global wafer output, while the United States currently has no domestic wafer manufacturing capacity. The global silicon supply chain faces persistent challenges, including geographic concentration, shortages of associated materials, geopolitical tensions, and lingering COVID-19-related disruptions. Although there is growing interest in reshoring or localising parts of the supply chain, the significant cost and complexity involved suggest that global interdependence will remain essential. Efforts are instead likely to focus on improving supply chain resilience and reducing single-point vulnerabilities.
Ukraine is also an important supplier, not of silicon itself, but of critical noble gases such as neon, krypton, and xenon, which are used in laser lithography during the processing of silicon wafers. Conflict-related disruptions, as seen in the war in Ukraine, can halt gas production, limit exports, and drive-up global prices. These disruptions contribute to delays and shortages across the silicon-based semiconductor supply chain, highlighting the fragility of upstream inputs that support advanced technology manufacturing.
Silicon metal producers
Polysilicon producers
Closed polysilicon producers
Silicon substitution
While silicon can be partially substituted in specific applications, its unique combination of properties such as semiconducting capability, thermal stability, and widespread availability makes it difficult to replace on a broad scale. In most cases, industries are focused on enhancing silicon’s performance through dopants or compound materials, rather than replacing it altogether. Silicon remains deeply embedded in global manufacturing infrastructure, and most alternatives, while promising, are still limited by cost, availability, or technical maturity.
In the electronics and semiconductor industry, alternative materials such as gallium arsenide (GaAs), gallium nitride (GaN), and silicon carbide (SiC) are used in specific high-performance applications. These substitutes are particularly valuable in areas requiring high-frequency, high-power, or high-temperature capabilities, such as in power electronics, RF devices, and LEDs. Emerging materials like graphene and transition metal dichalcogenides (TMDs) are also being explored for next-generation electronics, including flexible and ultra-thin devices. However, while these materials offer performance advantages in niche uses, they are typically more expensive, less abundant, and not yet suited for mass production at the scale and cost efficiency of silicon, particularly for mainstream integrated circuits and processors.
In solar energy, alternatives to crystalline silicon include thin-film technologies such as cadmium telluride (CdTe) and emerging perovskite solar cells. These materials can be cheaper to produce and are often lighter and more flexible than traditional silicon-based panels. However, they currently face challenges related to efficiency, long-term durability, and environmental or scalability concerns. Crystalline silicon (c-Si) remains the dominant material in the solar photovoltaic market due to its proven performance, relatively stable costs, and well-established global supply chain.
In the construction industry, silicone-based products are widely used for their durability, water resistance, and flexibility. While substitutes such as polyurethane, acrylic, or butyl-based sealants are available, they often do not match silicone's long-term performance in demanding environments. These alternatives may lack resistance to UV exposure, high temperatures, and extreme weather conditions, limiting their suitability for critical infrastructure or exterior applications. As a result, silicone remains the preferred choice for sealants, adhesives, and coatings in both residential and commercial construction.
In automotive manufacturing, aluminium-silicon alloys are commonly used to reduce vehicle weight while maintaining mechanical strength and thermal performance. Although materials such as magnesium, titanium, or carbon composites can serve as substitutes in certain components, they are generally more expensive or more complex to process. Silicon’s role in metal alloys is difficult to replace due to its balance of availability, performance, and cost-effectiveness, especially in mass-market vehicles where scalability is essential. This is equally true in electric vehicles, where silicon also plays a key role in battery systems and thermal management.
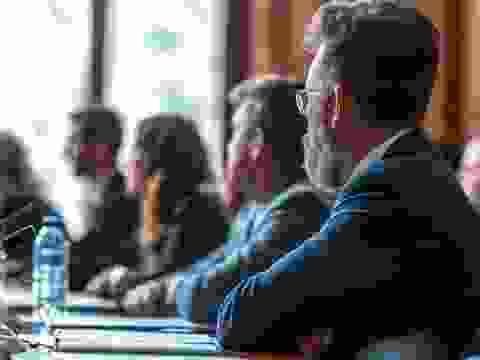
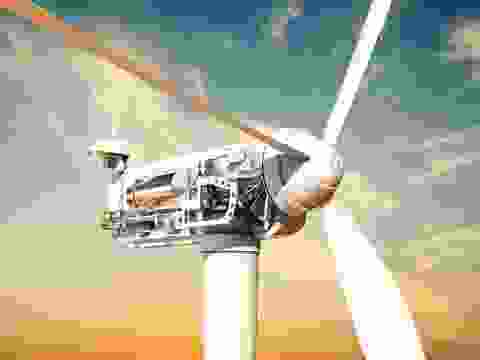
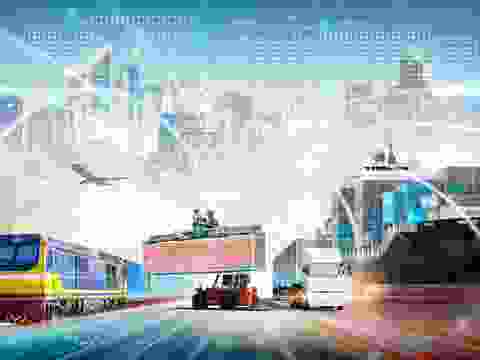
Meet the Critical Minerals team
Trusted advice from a dedicated team of experts.
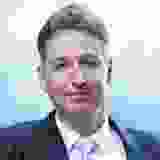
Henk de Hoop
Chief Executive Officer
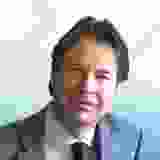
Beresford Clarke
Managing Director: Technical & Research
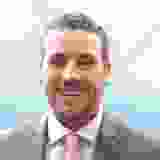
Jamie Underwood
Principal Consultant
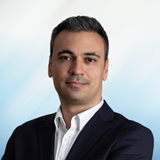
Ismet Soyocak
ESG & Critical Minerals Lead
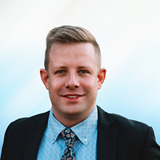
Rj Coetzee
Senior Market Analyst: Battery Materials and Technologies
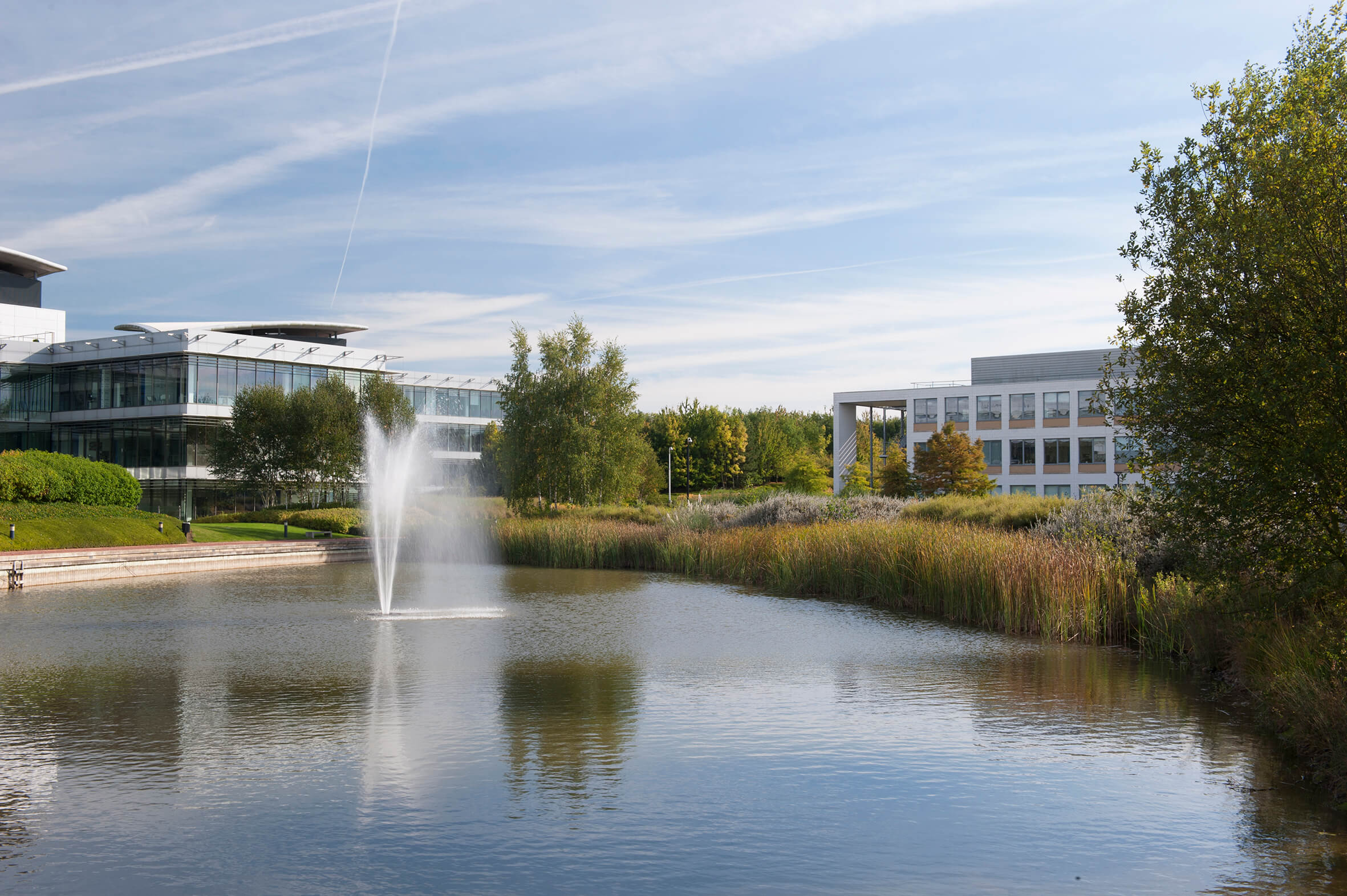
How can we help you?
SFA (Oxford) provides bespoke, independent intelligence on the strategic metal markets, specifically tailored to your needs. To find out more about what we can offer you, please contact us.