Hafnium
Critical Minerals and The Energy Transition
Navigating the Hafnium Market
Hafnium, a lustrous, silvery metal closely related to zirconium, is uniquely positioned in advanced materials and clean technologies. It is not mined directly but extracted as a byproduct from zirconium minerals, reflecting both its rarity and the complexity of its production. With a high melting point, excellent corrosion resistance, and exceptional neutron absorption, hafnium plays a vital role in specialised applications across the aerospace, nuclear, and semiconductor industries. It enhances the performance and safety of nuclear reactors, strengthens high-temperature superalloys in jet engines, and underpins next-generation transistor technologies through hafnium-based gate insulators. As demand for high-efficiency, low-emission technologies grows, so too does hafnium's strategic importance. Addressing future supply challenges will require a coordinated focus on diversifying sources, improving recycling systems, and developing substitutes for non-critical uses. In a world moving towards net-zero emissions, securing a stable and sustainable hafnium supply is essential to enabling progress across clean energy, defence, and digital infrastructure.
An introduction to hanfium
Hafnium demand and end-uses
Hafnium, a rare transition metal renowned for its exceptional thermal stability and neutron absorption capabilities, has solidified its role as a critical material in both traditional industrial uses and burgeoning energy transition technologies. It possesses a unique set of properties, including a high melting point of 2233°C, robust corrosion resistance, and efficient neutron capture, making it indispensable in sectors such as nuclear energy, aerospace engineering, semiconductor manufacturing, and cutting-edge energy systems.
Hafnium, a rare transition metal renowned for its exceptional thermal stability and neutron absorption capabilities, has solidified its role as a critical material in both traditional industrial uses and burgeoning energy transition technologies. It possesses a unique set of properties, including a high melting point of 2233°C, robust corrosion resistance, and efficient neutron capture, making it indispensable in sectors such as nuclear energy, aerospace engineering, semiconductor manufacturing, and cutting-edge energy systems.
The demand for hafnium is influenced by several key trends that shape its future applications. These include a resurgence in nuclear energy, expected to significantly boost its annual demand, stringent requirements for exceptionally pure HfO₂ in semiconductor advancements, and the growing need for hydrogen infrastructure development. Together, these elements highlight the escalating strategic importance of hafnium across various high-tech industries.
Currently, the demand for hafnium is on a steady rise, primarily driven by its use in nuclear energy, which remains a major consumer, alongside aerospace superalloys and the semiconductor sector. The market is also characterised by notable price volatility, with European spot prices having risen substantially in recent years. This underscores the dynamic nature of the hafnium market and its critical role in modern technological applications.
Trade restrictions on dual-use technologies and military applications have created regional supply disparities. The United States maintains strategic reserves for defence applications, while European manufacturers face 6-9 month lead times for reactor-grade hafnium. China's semiconductor industry growth has driven domestic consumption creating export limitations despite holding around 20% of reserves.
In nuclear applications, fafnium's neutron absorption cross-section of 105 barns for thermal neutrons makes it ideal for nuclear reactor control rods. Modern pressurised water reactors contain 500-800 kg of hafnium across 50-75 control rod assemblies, with each assembly lasting 15-20 years. The material's stability under radiation (maintaining structural integrity up to 10^21 n/cm² fluence) enables precise reaction control without becoming significantly radioactive.
Recent advancements in hafnium hydride moderators show potential for fast reactor designs, with HfH₁.₇ demonstrating 40% better neutron economy than traditional boron carbide systems. This innovation could reduce uranium fuel requirements by 12-15% in next-generation reactors.
Hafnium-tantalum alloys are being tested as accident-tolerant fuel cladding, showing 300% better oxidation resistance than zirconium alloys at 1,200°C. The China Nuclear JingHuan facility has developed Hf-7Ta-3W cladding that maintains integrity for 72 hours under loss-of-coolant conditions.
In the aerospace and advanced manufacturing, in jet engine superalloys, haium's primary aerospace application involves nickel-based superalloys containing 1.5-2% Hf for turbine blades and vanes. The MAR-M 247 alloy (1.5% Hf) enables turbine operation at 1,038°C, improving fuel efficiency by 8% compared to hafnium-free alternatives. Each CFM International LEAP engine contains 18 kg of hafnium across 78 turbine components.
In thermal protection systems, hafnium carbide (HfC), with a melting point of 3,958°C, plays an essential role in the manufacturing of hypersonic vehicle components. The material's exceptional ablation resistance at speeds exceeding Mach 7 makes it indispensable for critical parts such as leading edges and rocket nozzles. Recent evaluations of HfC-TaC composites have demonstrated a 22% enhancement in performance over silicon carbide in tests conducted under NASA's X-60A programme.
In semiconductor and electronics manufacturing of anode node technologes, the high dielectric constant of hafnium oxide (κ=25) is crucial for the ongoing miniaturisation of transistors, with Intel's 4 process utilising 2nm HfO₂ gate dielectrics. Furthermore, the ferroelectric properties of this material are being leveraged in 3D NAND flash memory, where HfZrO₄ films achieve 50% better charge retention compared to traditional silicon nitride.
There have also been technological breakthroughs in energy storage using hafnium. For example, researchers at Berkeley Lab have developed hafnium oxide-zirconium oxide micro capacitors that boast an energy density of 80mJ/cm², facilitating on-chip power delivery essential for AI processors. These devices exhibit a power density 170 times greater than that of standard capacitors, effectively addressing the 'power wall' challenge in advanced computing.
In the hydrogen economy, nitrogen-doped hafnium oxyhydroxide catalysts have shown platinum-like efficacy in proton exchange membrane electrolysers, significantly enhancing hydrogen evolution and oxidation reactions. This breakthrough could slash the costs of electrolyser catalysts by up to 90% compared to those made from platinum group metals.
Further developments in the use of hafnium have emerged within carbon capture systems, where hafnium-based metal-organic frameworks (MOFs), particularly Hf-UiO-66, are proving to be highly effective in direct air capture technologies. Notably, pilot systems in Estonia have demonstrated efficiencies of up to 90% in capturing CO₂, utilising hafnium amino-tris(methylene phosphonate) sorbents.
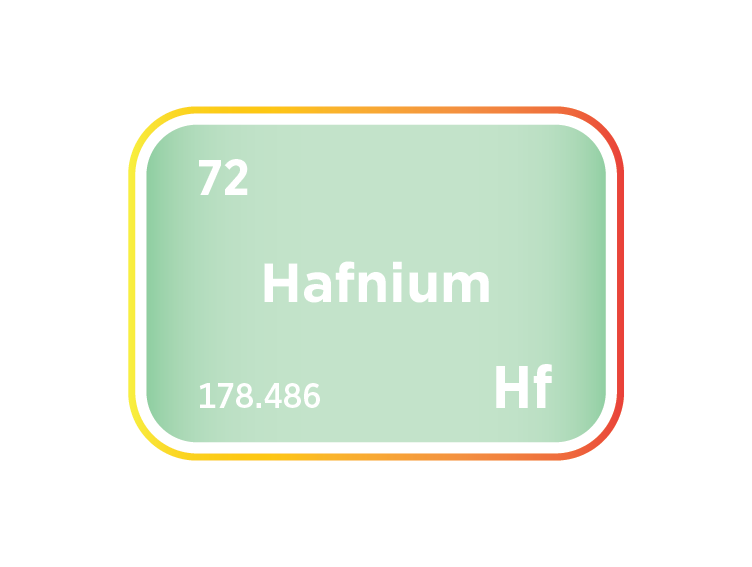
Hafnium supply
Hafnium supply is intricately tied to its production process, as the element is not found in a pure form in nature but is instead obtained as a byproduct of zirconium refining. Global production is predominantly concentrated in a few countries, most notably France, the United States, China, and Russia. The extraction and purification of hafnium from zirconium is both technically demanding and expensive, particularly when producing material suitable for nuclear applications. In response to growing industrial demand, significant investments have been made in facilities such as Framatome’s Jarrie plant in France, which is working to expand the output of high-purity hafnium.
The hafnium supply chain faces several constraints. These include the technical complexity and high cost of separating hafnium from zirconium, geopolitical factors, given that a large share of processing capacity is concentrated in NATO countries and Russia, and limitations in secondary recovery due to low recycling rates from superalloy scrap.
Hafnium is primarily sourced from zirconium-bearing minerals such as zircon (zirconium silicate) and baddeleyite (zirconium oxide), which are mined across various parts of the world. Although these minerals are principally valued for their zirconium content, they are also the most significant sources of hafnium. As a result, hafnium is extracted as a co-product, a process that has become increasingly important due to the element’s scarcity and rising demand across high-tech and strategic sectors.
Hafnium production is shaped by distinct regional concentrations in both raw material extraction and specialised metallurgical processing. The key zirconium mining countries underpinning hafnium availability include Australia, South Africa, the United States, and Senegal. Secondary producers such as Mozambique, Sierra Leone, and Madagascar also contribute to the global zircon supply chain, albeit on a smaller scale.
Nations with advanced nuclear-grade zirconium refining capabilities—and therefore capable of producing hafnium—include France, the United States, Russia, and China. In addition to these primary processing countries, several others are gradually expanding their roles in the global hafnium market. India, for instance, is developing its processing capabilities through the Nuclear Fuel Complex in Hyderabad, with the aim of extracting hafnium from domestic zircon sources. Germany has modest but notable production capacity through companies like H.C. Starck, which processes imported zircon alongside other strategic metals. Canada, meanwhile, is exploring the potential to recover hafnium from the Nechalacho rare earth deposit; although still at the pilot stage, this initiative could eventually make Canada a contributor to global supply. These efforts reflect a broader trend of countries investing in domestic processing technologies or expanding existing infrastructure to capitalise on the strategic importance of hafnium.
Recycling presents additional challenges, primarily due to the technical difficulty of separating hafnium from zirconium in scrap materials. Nonetheless, recent advancements, such as new hydrometallurgical processes developed by American Elements have shown promise. These techniques have proven effective in recovering substantial quantities of hafnium from turbine blade scrap, offering a potential avenue for supplementing the global supply and easing pressure on primary production sources.
Top zirconium mining countries supplying hafnium feedstock
Leading hafnium refining countries and processing facilities
Hafnium substitution
In a range of specialised applications, there is a move towards alternatives to hafnium, driven by factors such as cost and availability. For example, zirconium serves as a substitute in nuclear reactors due to its low neutron absorption rates, unlike hafnium which is traditionally used in control rods. In the semiconductor sector, materials like titanium nitride (TiN) and aluminium oxide (Al₂O₃) are being used in place of hafnium for metal gates and insulators respectively, providing advantages in terms of conductivity and insulation.
In aerospace engineering, where components must withstand extreme conditions, alloys of Niobium and Tantalum are preferred for their heat and corrosion resistance comparable to that of hafnium. Tungsten, known for its high melting point, is also a favoured alternative in applications that require robust filaments and electrodes. The choice of these substitutes is guided by specific requirements of each application, including mechanical properties and resistance to environmental factors, reflecting a sophisticated approach to selecting alternatives that strike a balance between performance and practical considerations.
Furthermore, ongoing research into substitutes for hafnium in superalloys is making headway with the development of tantalum-rhenium composites, silicon carbide fiber-reinforced molybdenum, and additive-manufactured gradient alloys. These innovations are providing various performance and cost benefits, indicating a proactive stance towards finding sustainable and efficient alternatives in high-performance applications.
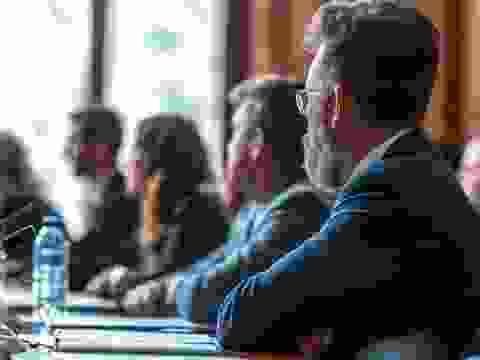
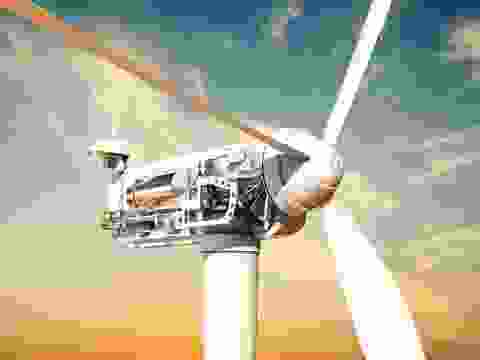
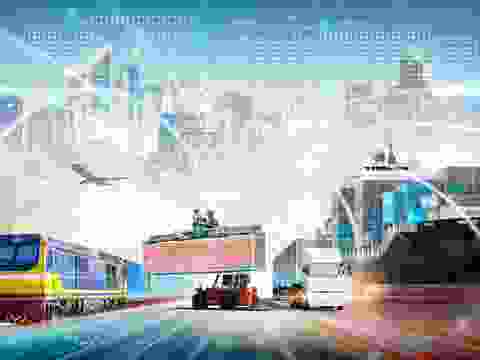
Meet the Critical Minerals team
Trusted advice from a dedicated team of experts.
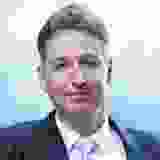
Henk de Hoop
Chief Executive Officer
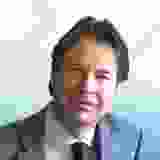
Beresford Clarke
Managing Director: Technical & Research
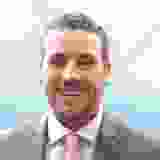
Jamie Underwood
Principal Consultant
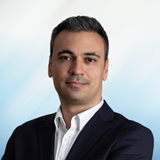
Ismet Soyocak
ESG & Critical Minerals Lead
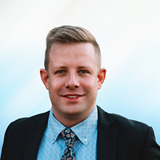
Rj Coetzee
Senior Market Analyst: Battery Materials and Technologies
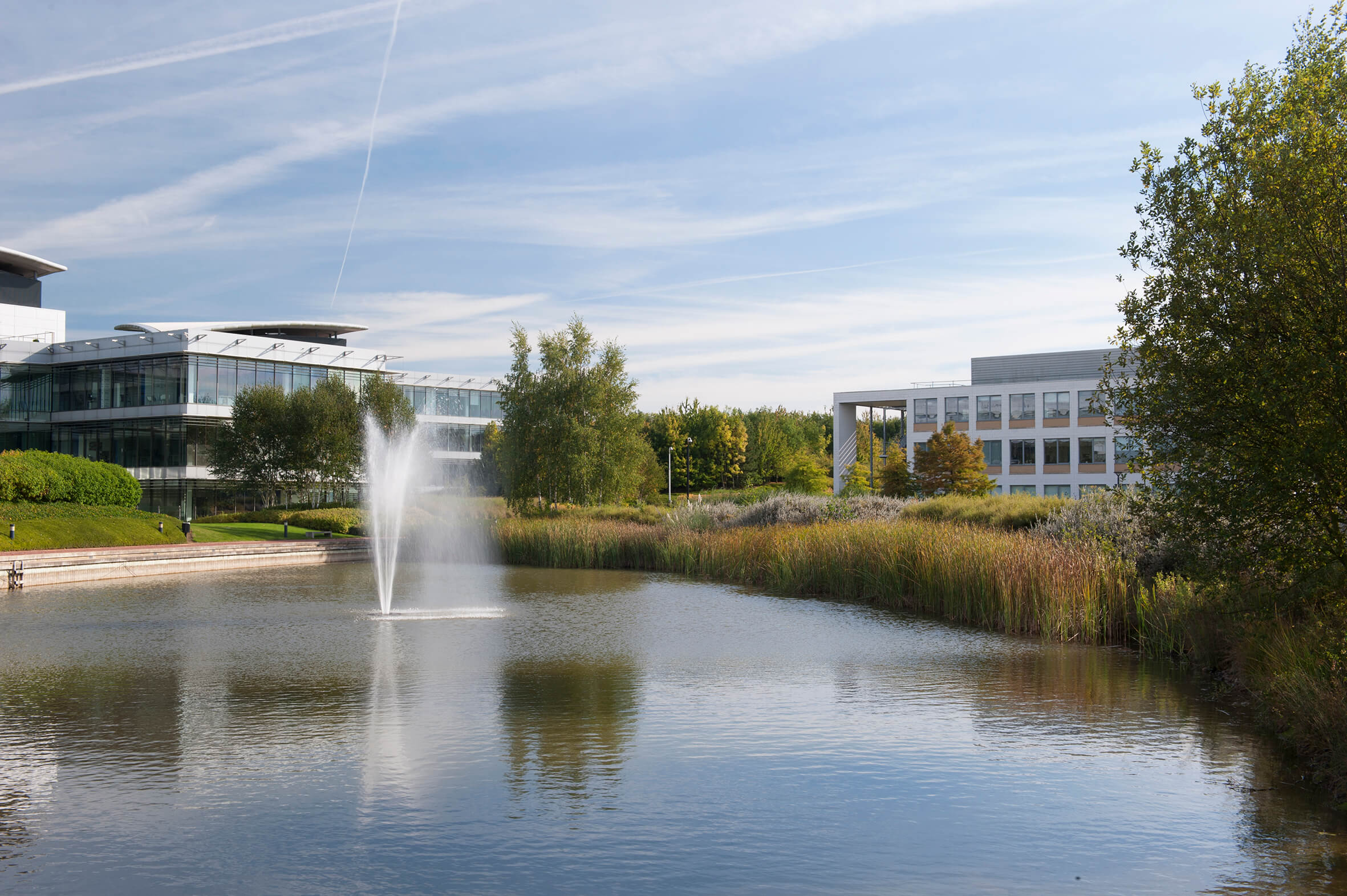
How can we help you?
SFA (Oxford) provides bespoke, independent intelligence on the strategic metal markets, specifically tailored to your needs. To find out more about what we can offer you, please contact us.