Bismuth
Critical Minerals and The Energy Transition
Navigating the Bismuth Market
Bismuth is an underappreciated but increasingly strategic element, gaining traction as a key enabler of the global energy transition. With a unique combination of low toxicity, thermal stability, and favourable electronic properties, bismuth is used across clean energy technologies, from nuclear reactors and thermoelectrics to solar energy systems and advanced battery chemistries. It also serves as a sustainable, non-toxic alternative to lead in multiple applications, including electronics, medical imaging, and fire safety systems. Although geologically scarce, bismuth is typically obtained as a by-product of base metal mining and is more economically accessible than many critical or rare earth elements. However, its highly concentrated supply, dominated by China, raises concerns about long-term availability, especially as demand grows in environmentally conscious sectors. Bismuth’s expanding role spans end-uses in energy, manufacturing, healthcare, and electronics. It is central to multiple low-carbon technologies, and its substitution potential in a range of industrial processes highlights its strategic value. As the energy transition accelerates, bismuth’s distinctive properties and widening applications position it as a material of growing industrial, technological, and geopolitical significance.
An introduction to bismuth
Bismuth demand and end-uses
Bismuth is establishing itself as a crucial enabler of the global energy transition. Its role spans nuclear reactors, solar and thermoelectric systems, and energy storage technologies, offering a rare combination of performance, environmental safety, and economic viability. As research advances and demand for sustainable materials grows, bismuth is set to play an increasingly prominent role in the future of clean energy.
Bismuth is a highly versatile element with growing importance across modern industries, particularly in the context of the global energy transition. Its applications span electronics, manufacturing, healthcare, cosmetics, and clean energy technologies. Prized for its non-toxic nature, bismuth is a preferred substitute for hazardous elements such as lead, while its unique thermal and electronic properties support innovations in energy efficiency, environmental sustainability, and health and safety standards.
In electronics and energy, bismuth telluride is widely used in thermoelectric devices that convert heat directly into electricity or provide efficient heating and cooling. Thermoelectric coolers are employed in portable refrigeration units, climate-controlled car seats, and electronic component cooling, while thermoelectric generators harness waste heat from vehicle exhausts or industrial processes to generate electricity, reducing dependence on fossil fuels. Bismuth is also critical in lead-free solders used on circuit boards and components, reducing electronic waste toxicity and enhancing recyclability.
Low melting point bismuth alloys are essential for fire sprinkler systems, melting at preset temperatures to trigger water release and provide reliable fire suppression. In healthcare, bismuth compounds improve X-ray imaging by enhancing contrast without resorting to more hazardous materials. In cosmetics, bismuth oxychloride provides shimmer in products such as eyeshadows and highlighters, while in dentistry, bismuth-containing amalgams offer a safer, mercury-free alternative.
Bismuth’s role in clean energy is rapidly expanding. As a post-transition metal with low toxicity and favourable electronic, optical, and thermal properties, bismuth supports a range of clean technologies from nuclear cooling systems and solar energy to thermoelectric materials and energy storage. Its substitution for toxic elements like lead is increasingly valuable in light of stricter global regulations, and its environmental safety aligns well with decarbonisation goals.
One of the most advanced applications of bismuth is its use in lead-bismuth eutectic (LBE) alloys as coolant in nuclear reactors. LBE, composed of 44.5% lead and 55.5% bismuth, melts at just 123.5°C and boils at 1,670°C, making it ideal for Generation IV fast neutron reactors. These reactors offer improved thermal efficiency, enhanced safety, and potential for hydrogen production, operating under atmospheric pressure and high temperatures. First developed for Soviet Alfa-class submarines, LBE systems are now under development globally. The alloy’s chemical stability, high thermal conductivity, and low reactivity with air or water give it operational advantages over sodium and other liquid metal coolants. LBE reactors can also improve fuel utilisation and reduce radioactive waste by burning transuranic actinides.
Bismuth-based materials also show strong potential in solar energy technologies. Bismuth (III) oxide, a wide-bandgap semiconductor, is being explored in photovoltaic devices, thin-film solar cells, and dye-sensitised solar cells for its ability to absorb light and reduce electron recombination. Bismuth-based perovskites are also under development as low-toxicity replacements for traditional lead-based solar materials, although further efficiency improvements are needed. In dye-sensitised solar cells, bismuth-based photoanodes offer high stability and efficient electron transport.
Photocatalysis is another promising area. Compounds such as bismuth vanadate (BiVO₄) are being developed for water splitting and CO₂ reduction, with applications ranging from hydrogen production to environmental remediation. The monoclinic phase of BiVO₄ demonstrates strong photocatalytic activity under visible light. Performance is being enhanced through nanostructuring, hybridisation with other materials, and integration with photovoltaics to enable co-generation of electricity and clean fuels.
Thermoelectric materials based on bismuth allow for direct heat-to-electricity conversion, enabling waste heat recovery from industrial equipment, engines, and other sources. These materials are increasingly used in hybrid thermoelectric systems to improve efficiency across diverse temperature ranges, particularly in solar thermal and geothermal platforms. Their ability to enhance overall energy efficiency makes them valuable for low-carbon systems.
Bismuth also plays a growing role in energy storage technologies. In lithium-ion batteries, bismuth oxide is being explored as an anode material for its high capacity and stability. For sodium-ion batteries, which offer a cheaper and more abundant alternative to lithium, bismuth’s ability to accommodate large sodium ions makes it a promising solution. In supercapacitors, bismuth-based compounds provide high power density and fast charging capabilities due to their conductivity and structural stability.
From an environmental standpoint, bismuth offers distinct advantages. Its non-toxic profile contrasts sharply with toxic metals like lead and cadmium, supporting safer manufacturing and cleaner end-of-life processes. Bismuth contributes to lower environmental footprints in energy systems, supporting sustainable development goals while reducing risks to human health.
Despite its many advantages, challenges remain. Performance optimisation is still required in areas such as photovoltaics and photocatalysis. Scalability, production costs, and material consistency are key issues for commercial deployment. Continued research is focused on improving electronic properties, developing bismuth nanostructures, and creating hybrid materials that maximise performance while preserving environmental benefits.
Future research directions include the use of nanotechnology to increase catalytic activity, composite materials for multifunctional performance, and advanced manufacturing to enable high-quality, scalable production. As understanding of bismuth's properties grows, new applications are likely to emerge across the energy sector.
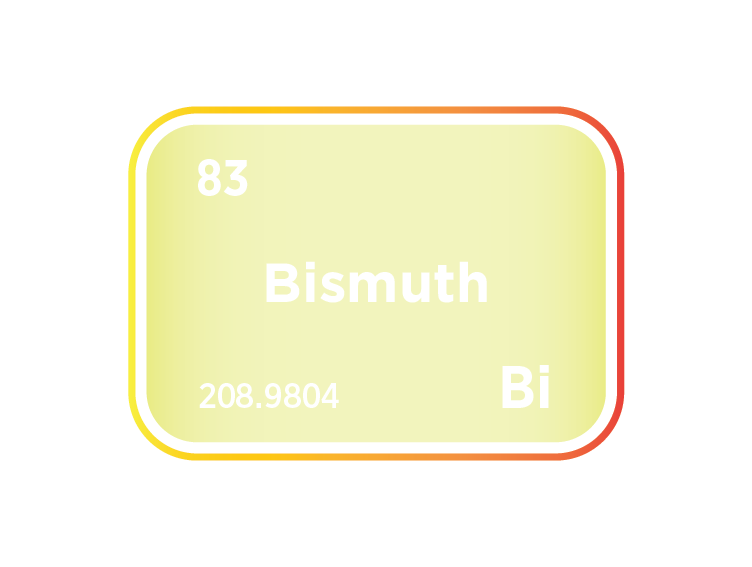
Bismuth supply
Bismuth is a relatively scarce element in the Earth's crust and is typically obtained as a by-product of the mining and refining of other metals, most notably lead, copper, tin, and tungsten. It is rarely mined as a primary commodity due to its low natural concentrations and limited standalone ore bodies.
Despite its geological scarcity, bismuth is considered economically accessible, as it is often recovered during the processing of more abundant base metals. It is also less costly to refine than many rare or strategic elements such as indium or gallium. Its durability extends the lifespan of components, reducing replacement and maintenance costs, which contributes to the commercial viability of bismuth-based technologies—particularly in cost-sensitive clean energy applications.
The most common bismuth-bearing minerals include bismuthinite (Bi₂S₃), a primary bismuth sulphide mineral occasionally mined directly, and bismite (Bi₂O₃), a bismuth oxide found in oxidised zones. Bismuth is also present in the tetrahedrite–tennantite group, a family of copper–arsenic–antimony sulphosalts that may contain trace amounts of bismuth. Additionally, galena (PbS)—the primary ore of lead—often hosts bismuth as an impurity, making lead smelting a major source of global bismuth supply.
Given its association with polymetallic deposits, bismuth production is strongly influenced by the economics and environmental regulation of base metal mining. Global supply is, therefore, vulnerable to shifts in the lead and copper industries, particularly when smelters shut down or adopt cleaner processes that do not recover bismuth.
Currently, refined bismuth production is overwhelmingly concentrated in China, which dominates both upstream mining and downstream refining. This geographic concentration presents a potential supply risk for countries reliant on imports, especially as demand grows for environmentally friendly alternatives to toxic metals such as lead.
Other refined bismuth producers include Laos, where bismuth is recovered from polymetallic operations; South Korea and Japan, which process imported concentrates for electronics and pharmaceuticals; and Kazakhstan, where production is tied to lead and copper refining. Smaller-scale refining is also conducted in Bulgaria, linked to lead-zinc mining, and in Bolivia, one of the few nations with primary bismuthinite production, albeit at a modest scale.
The United States was historically a refined bismuth producer, primarily through lead smelting. However, due to shifting economic and environmental conditions, domestic production has ceased. The U.S. now relies entirely on imports to meet its industrial and technological requirements.
Refined bismuth producers
Historic refined bismuth producers
Bismuth substitution
Alternatives to bismuth span a wide range of sectors, with choices shaped by factors such as cost, availability, regulatory requirements, and performance criteria. The suitability of each substitute depends on the specific demands of the application, whether mechanical strength, thermal or electrical conductivity, or biocompatibility.
Bismuth-based compounds are known for converting waste heat into electricity in thermoelectric devices. Alternatives include silicon germanium (SiGe), typically used in high-temperature environments, and lead telluride (PbTe), which performs effectively within specific temperature ranges.
For lead-free solders, tin-silver-copper (SAC) alloys have emerged as the most common alternative to bismuth-containing formulations. Widely used in electronics, SAC solders offer strong mechanical properties, good solderability, and resistance to thermal fatigue—though their higher melting point can pose challenges compared to bismuth-based solders.
In medical imaging, barium sulfate serves as a widely used substitute for bismuth in X-ray contrast agents, providing effective visibility of the gastrointestinal tract without toxicity concerns.
In cosmetics, mica and titanium dioxide are common alternatives to bismuth oxychloride. They deliver shimmer and pearlescent effects in products such as eyeshadows and highlighters while meeting consumer and regulatory expectations for low-toxicity ingredients.
In dentistry, composite resins are often used in place of bismuth-containing amalgams. These materials offer aesthetic benefits and are mercury-free, although they may lack the same durability as traditional amalgams over time.
In pharmaceuticals, particularly for gastrointestinal treatments, bismuth compounds can be replaced by alumina (aluminium oxide), calcium carbonate, magnesia (magnesium oxide), and various antibiotics. However, these substitutes may not replicate the antibacterial effectiveness or acid stability of bismuth formulations.
In pigments, particularly for coatings and personal care products, alternatives to bismuth oxychloride include titanium-dioxide-coated mica flakes and fish-scale extracts (guanine crystals). The choice of a substitute depends on regulatory standards, sustainability concerns, and desired visual properties.
For low-temperature soldering, cadmium, indium, lead, and tin can partially replace bismuth–tin alloys. Nevertheless, cadmium and lead are toxic, and indium is scarce and expensive—making them less suitable for environmentally regulated or large-scale applications.
In precision machining, bismuth alloys are commonly used to hold components in place due to their expansion upon solidification. Thermoplastic resins can be used as alternatives, though they may not offer the same thermal conductivity or dimensional stability. Likewise, in fire suppression systems, glycerine-filled glass bulbs serve as effective substitutes for bismuth in thermal triggers.
In free-machining alloys, elements like lead, selenium, and tellurium can replicate bismuth’s lubricating and chip-breaking qualities. Yet each has environmental or health trade-offs, prompting ongoing research into safer and more sustainable options.
Importantly, bismuth itself is increasingly deployed as a non-toxic substitute for lead in products such as plumbing solders, fishing weights, hunting ammunition, lubricating greases, and soldering materials. Its high density and malleability make it an effective and safer replacement, particularly where human health and environmental impacts are key concerns.
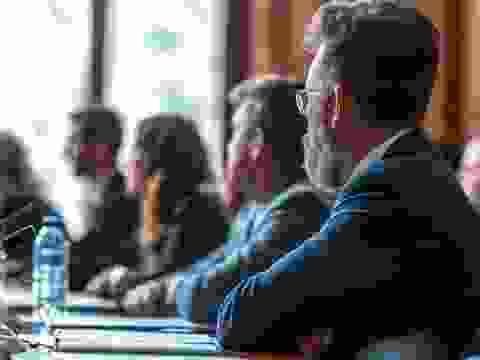
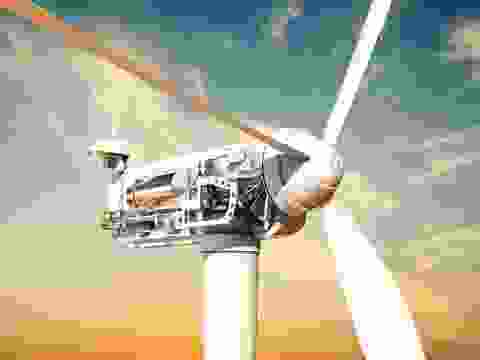
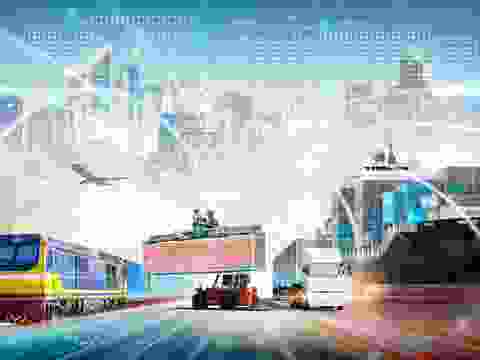
Meet the Critical Minerals team
Trusted advice from a dedicated team of experts.
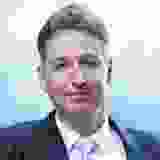
Henk de Hoop
Chief Executive Officer
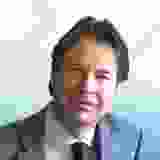
Beresford Clarke
Managing Director: Technical & Research
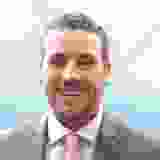
Jamie Underwood
Principal Consultant
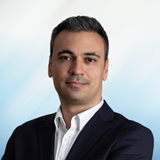
Ismet Soyocak
ESG & Critical Minerals Lead
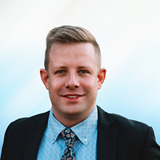
Rj Coetzee
Senior Market Analyst: Battery Materials and Technologies
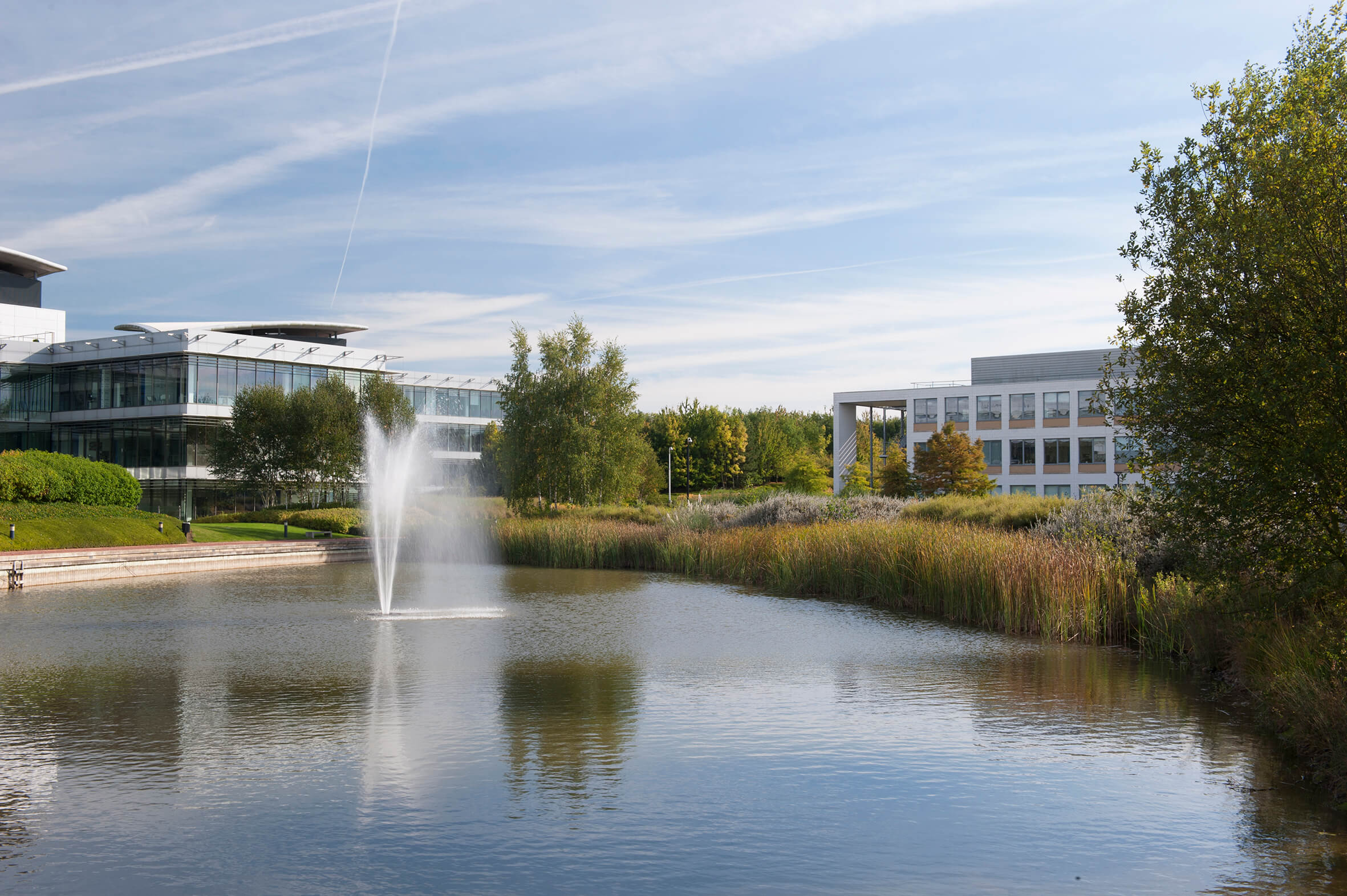
How can we help you?
SFA (Oxford) provides bespoke, independent intelligence on the strategic metal markets, specifically tailored to your needs. To find out more about what we can offer you, please contact us.