Barium
Critical Minerals and The Energy Transition
Navigating the Barium Market
Barium, primarily in the form of barium sulphate, is a critical mineral extensively used as drilling mud in the oil and gas industry. Beyond its traditional roles, barium's applications stretch to manufacturing paints and plastics, sound reduction in engine compartments, and medical imaging, leveraging its high density and chemical inertness. Amidst the global push for cleaner energy, barium’s role in the energy transition is becoming increasingly significant, particularly in geothermal energy production and carbon capture technologies where its properties help seal wells against leaks and enhance the efficiency of processes. The global supply of barite is primarily concentrated in the Asia-Pacific region, which contributes about 70% of the world's output, with China alone responsible for nearly half. This concentration significantly impacts global supply chains, influencing pricing and availability, which are vulnerable to regional policy shifts and economic conditions. Barite production is geographically diverse with producers located across continents, including Asia, Africa, Europe, the Americas, and Australia. However, the scale of production and environmental impacts vary widely among these regions, influenced by local geology, technological advancements, and regulatory frameworks. Increasingly, the industry is focusing on secondary barite sourced from mining tailings. Advancements in barite mining techniques and compliance with the EU's REACH regulation, which mandates less than 3 mg/kg of heavy metals in products, are driving progress towards more sustainable energy practices.
An introduction to barium
Barium demand and end-uses
North America leads in market demand, accounting for over 40% globally, largely due to intense shale and offshore drilling activities. Barite's versatility ensures its relevance across energy, healthcare, and manufacturing sectors, where strategic investments in sustainable mining and recycling technologies are pivotal in addressing supply chain vulnerabilities and environmental concerns.
Global oil demand directly correlates with increased consumption of barite in drilling fluids. While North America continues to lead in consumption, Asia-Pacific dominates in production, with China's output being crucial to global supply chains. Emerging mining projects in Liberia, Mexico, and Zimbabwe are seeking to diversify supply sources, though they face logistical and geopolitical challenges.
China's dominance in barite production, accounting for 50% of global output, introduces vulnerabilities in the supply chain, particularly as environmental regulations become more stringent. In contrast, the United States remains heavily reliant on imports despite an increase in domestic shale drilling, highlighting the geopolitical complexities of barite trade. Europe's market remains stable, driven by stringent radiation safety standards in the healthcare and nuclear sectors. Meanwhile, Africa's untapped reserves, particularly in Morocco and Algeria, present opportunities for growth, though infrastructural limitations are a barrier to rapid development.
In the oil and gas industry, barite's high specific gravity (4.0–4.5 g/cm³) and chemical inertness make it essential as a weighting agent in drilling muds, accounting for 88% of its global consumption. Barite-enriched muds counteract subsurface pressures to prevent blowouts, particularly in deepwater wells exceeding 5,000 metres. It also aids in cuttings removal by transporting rock fragments to the surface and reduces friction and heat generation during drilling, extending the lifespan of equipment. The shift towards horizontal drilling and hydraulic fracturing (fracking) has increased demand, as these methods require 20–30% more barite per well compared to conventional vertical drilling.
While barite-based muds are preferred for their performance, environmental concerns remain. Disposed drilling waste containing barite can accumulate heavy metals like lead and zinc, posing risks to aquatic ecosystems. Innovations in eco-friendly formulations, such as Excalibar Minerals’ ExBar HD Series, aim to improve biodegradability while maintaining necessary density.
In radiation shielding, from medical imaging to nuclear safety, barite's radiation attenuation capabilities, due to its high atomic number (Z=56) and density (4.5 g/cm³), enable effective absorption of X-rays and gamma rays. A 2024 study showed barite concrete’s linear attenuation coefficient of 0.205 cm⁻¹ at 662 keV, outperforming ordinary concrete. In medical imaging, pharmaceutical-grade barium sulfate suspensions coat gastrointestinal tracts, enhancing visibility in X-rays and CT scans. At nuclear facilities, barite-enriched concrete shields reactors and waste storage units, reducing neutron flux by 40% compared to standard concrete. And in industrial shielding, precast Bariwall bricks, used in facilities like Birmingham University, offer modular radiation protection solutions.
Barite is a multifunctional performance enhancer in plastics and composites. Incorporating barite at up to 70% filler concentration improves plastic stiffness (by 25%), heat resistance (withstanding 180°C), and sound insulation (15 dB noise reduction). RBH Ltd.’s AmBar® and SintaBar® grades enhance automotive components like dashboards and under-hood parts, where dimensional stability under thermal stress is critical.
Barite reduces polymer costs by 12–18% while enhancing recyclability. Its inert nature minimises degradation during reprocessing, making it ideal for circular manufacturing. In injection-moulded products, barite-filled plastics exhibit 30% lower shrinkage rates, reducing post-production machining.
In construction and industrial materials, barite acts as a flux in glass production, increasing the refractive index (to 1.62) and chemical resistance. In ceramics, it reduces firing shrinkage by 8% and enhances glaze opacity, critical for sanitaryware and tiles. TEAMChem’s high-purity formulations achieve 99.9% whiteness in premium ceramic coatings.
In metal casting and foundry applications, barite’s high melting point (1,580°C) makes it ideal for foundry moulds, improving surface finish and reducing gas porosity in aluminium and steel castings. Its thermal stability minimises mould cracking during rapid cooling cycles.
Barium sulfate is used in medical imaging for precision diagnostics. Gastrointestinal contrast agents, purified barium sulfate suspensions, ingested or administered via enema, coat mucosal linings to visualise ulcers, polyps, and tumours. Advances in nanoparticle suspensions now enable high-resolution imaging of small intestinal lesions previously undetectable. Safety protocols ensure non-toxicity, with adverse reaction rates below 0.01%.
Barite’s emerging role in lithium-ion battery shields and EV components presents a new opportunity, enhancing its market potential.
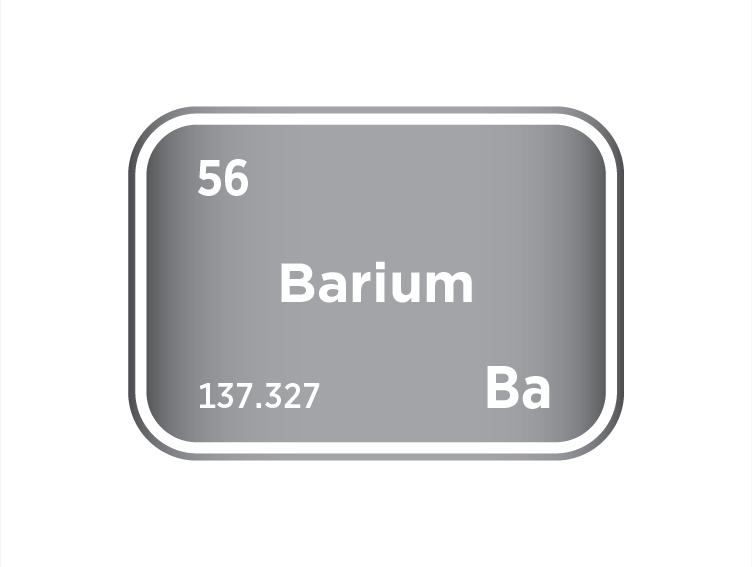
Barium supply
Barite, primarily composed of barium sulphate, is an indispensable industrial mineral extensively used in the oil and gas industry as drilling mud. Its applications extend to the manufacture of paints and plastics, sound reduction in engine compartments, medical imaging tests, and various other industries due to its high density and chemical inertness.
The global supply of barite is largely concentrated in the Asia-Pacific region, contributing about 70% of the world's output, with China alone responsible for nearly half. This concentration in China significantly impacts global supply chains, particularly in terms of pricing and availability, which can be affected by local policy shifts and economic conditions.
Despite this concentration, barite production is globally diverse, spanning several continents which helps mitigate reliance on any single country and stabilises supply chains against geopolitical or economic fluctuations. Major current producers are spread across Asia (China, India, Kazakhstan), Africa (Morocco, Nigeria), Europe (Turkey, Russia), the Americas (USA, Brazil), and Australia. Historically, nations like Georgia, Slovakia, Guatemala, and Argentina have also played roles in the production of barite. The scale of production and environmental impacts vary significantly across these regions, influenced by local geology, technological advancement, and regulatory frameworks.
A rising interest in secondary barite, recovered from mining tailings, is noteworthy. This practice not only reduces the environmental burden of new mining operations but also repurposes waste into valuable products. For example, recycled barite composites have demonstrated electromagnetic shielding effectiveness of 17.99 dB in low-frequency applications, outperforming alternatives like zeolite and magnetite.
Environmental and regulatory challenges are prominent in the barite sector, particularly with the emission of pollutants such as fluorine and strontium during extraction and processing. These issues necessitate advanced beneficiation techniques to lessen environmental impacts.
Moreover, stringent regulations such as the EU’s REACH (Registration, Evaluation, Authorisation, and Restriction of Chemicals) stipulate that heavy metal content in consumer products must be below 3 mg/kg. This directive compels producers to adopt cleaner processing technologies, thereby ensuring compliance and promoting sustainability in the barite industry.
Barium substitution
Barite is extensively utilised in oil and gas drilling as a weighting agent, essential for preventing blowouts and stabilising the borehole. It is particularly valued for its high specific gravity, low solubility, and chemical inertness. While alternatives to barite do exist, they are typically employed only in specific scenarios due to various trade-offs.
Several substitutes are used under particular conditions. Calcium carbonate, for example, is often utilised in shallow, water-based drilling muds where formation pressures are low. Its biodegradable nature and ability to dissolve in acid make it advantageous for reservoir clean-up. Hematite is employed for its high specific gravity in situations that necessitate heavier muds, proving especially useful in deep wells. Ilmenite, another dense mineral, acts as a weighting agent suitable for the high-density muds required in deep well applications. Manganese tetroxide is preferred in environments that require non-toxic materials and is also beneficial in high-temperature geothermal drilling. Less commonly used alternatives such as Celestite, Iron Carbonate, and Strontium Carbonate are mentioned in some technical literature and patents, selected when specific properties of these minerals meet unique drilling requirements.
Despite the availability of these alternatives, none can fully replace barite across all drilling conditions. Barite's availability, effectiveness, and cost-efficiency continue to make it the primary choice in most drilling operations.
Alternative weighting agents like ilmenite and hematite threaten barite’s dominance in drilling fluids, though their higher costs (15–20% premium) limit adoption.
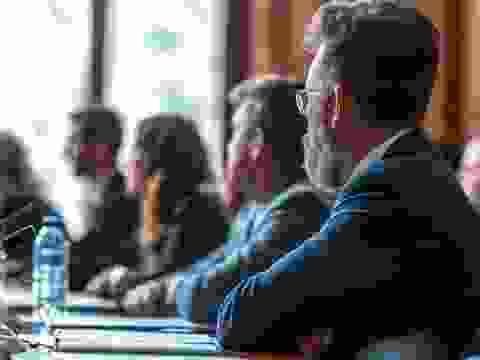
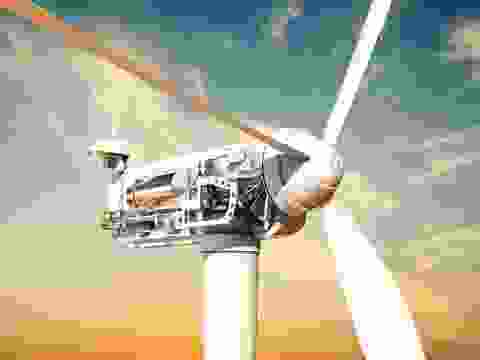
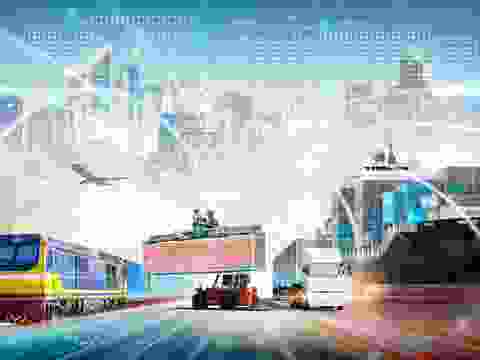
Meet the Critical Minerals team
Trusted advice from a dedicated team of experts.
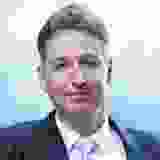
Henk de Hoop
Chief Executive Officer
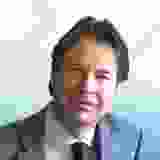
Beresford Clarke
Managing Director: Technical & Research
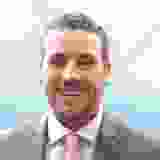
Jamie Underwood
Principal Consultant
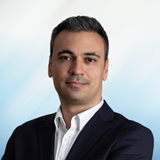
Ismet Soyocak
ESG & Critical Minerals Lead
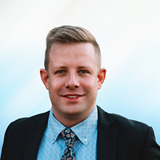
Rj Coetzee
Senior Market Analyst: Battery Materials and Technologies
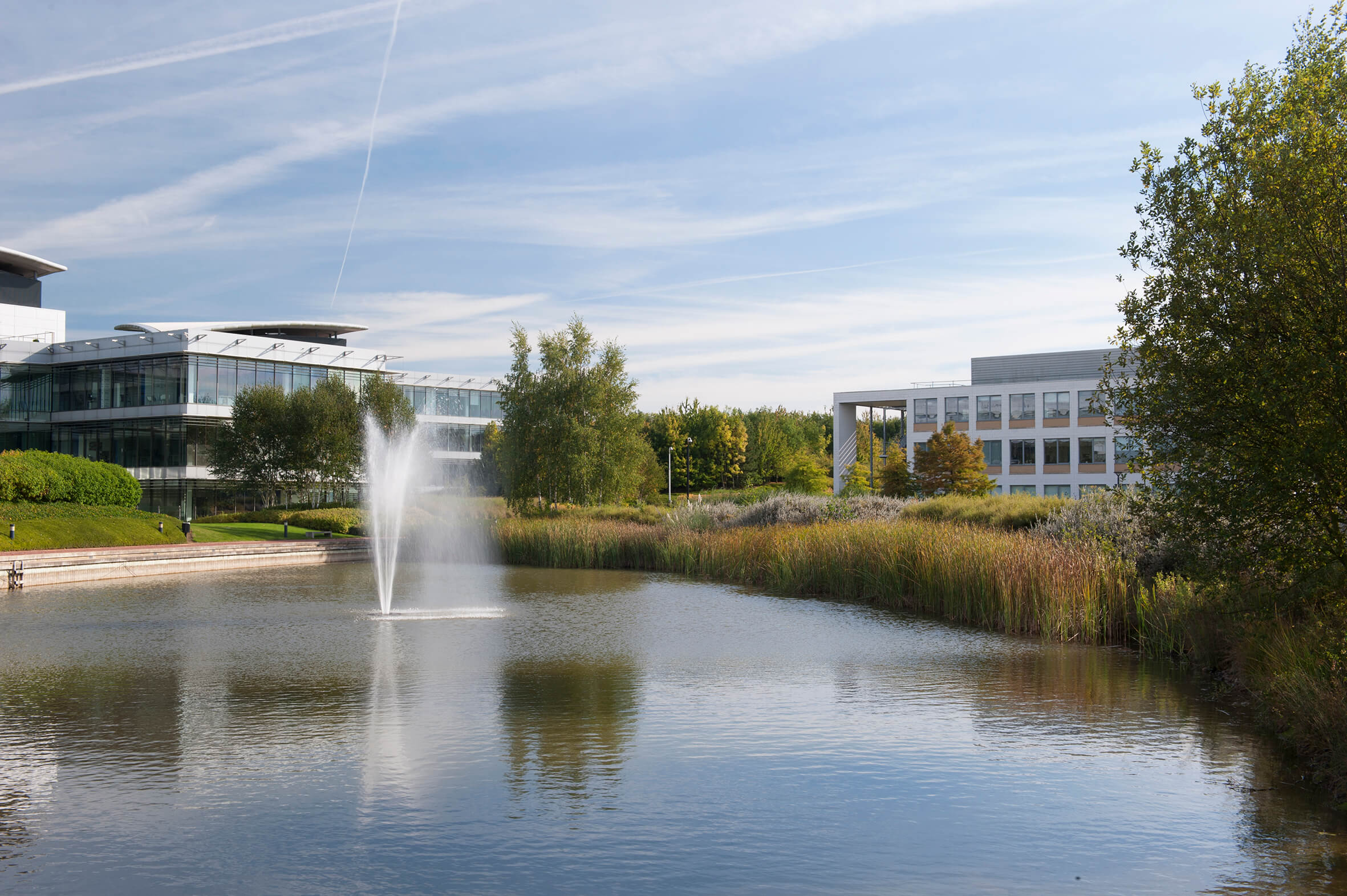
How can we help you?
SFA (Oxford) provides bespoke, independent intelligence on the strategic metal markets, specifically tailored to your needs. To find out more about what we can offer you, please contact us.