Can graphite export restrictions lift supply?
Localising electric vehicle supply chains
20 June 2024
Graphite export restrictions could finally be the push needed to develop domestic resources in North America and Europe
Discussions about battery materials tend to focus on lithium, nickel, and cobalt, while graphite remains the forgotten but vital ingredient in the many EV plans that have been announced. SFA (Oxford) views graphite as the dominant anode material over the next two decades despite the promise of the many alternatives that are in development. However, while there have been many improvements to graphite anodes over the past few years, the development of upstream and midstream production outside of China has stagnated. As graphite production continues to be dominated by China and prices dampened for some time, it has not been easy to attract the necessary investment to build domestic supply. Now, graphite has become the focus of trade tensions between the US and China, and we believe that this could finally drive the much-needed industry development in North America and Europe and curb some of the geopolitical risks associated with the energy transition.
Is the critical battery material finally getting its due?
In December 2023, China imposed trade restrictions on graphite that required producers to apply to the government for permits to export high-grade graphite materials and related products in the future. Given China’s dominance of natural and synthetic graphite, many sectors worldwide, not just EV production, could be negatively impacted, given the lack of industry development. As part of a broader initiative that included an increase of tariffs on EVs (from 25% to 100% in 2024) and lithium-ion batteries (from 7.5% to 25% in 2024), the US imposed a new 25% tariff on natural graphite from China in May. On 15 June, the United States Trade Representative reinstated the 25% tariff on synthetic graphite. To many, the US response is well overdue, especially as the lithium-ion battery market continues to expand, and there are no substitutes for graphite’s use in refractories and military applications.
Graphite is the anode material choice for many reasons, but to us, it is the thermal stability of the material, the minimal expansion and contraction during charging and discharging, and the low cost that has made it the dominant choice. Efforts are being made to improve and replace graphite anodes owing to their weight, flat voltage profile, inability to accommodate high-voltage cathodes, and long-term stability as the battery ages. Automakers have already adopted silicon-enhanced graphite (<10% silicon) and invested in developing silicon-carbon, silicon oxides, graphenes, silicon metal, nano-composite silicon materials, and lithium metal. However, the new anode materials in development have unique technical hurdles that need to be overcome, which may or may not be possible. Furthermore, the time it takes to adopt even minute changes to the battery chemistry means that more significant changes, such as replacing the graphite anode, is a 6-10 commercialisation process from the prototype phase of development.
Depending on the vehicle's range, EV batteries need about 50-100 kg of graphite. Automakers can use either natural or synthetic graphite depending on design goals, often blending them to take advantage of their individual qualities. Natural graphite provides higher capacity and lower costs, while synthetic graphite provides longevity and fast charging capabilities. Once purified, both types are spheroidised and coated, but synthetic graphite, typically 2-3x the price of natural graphite, is much more ecologically damaging. While China’s coal-powered energy generation and use of strong acids impact anode production from both synthetic and natural graphite, the energy-intensive Acheson process is typically used to produce synthetic graphite has a more negative impact and is a notable source of NOx, SOx and PM10 pollutants.
LCA comparison between synthetic and natural graphite
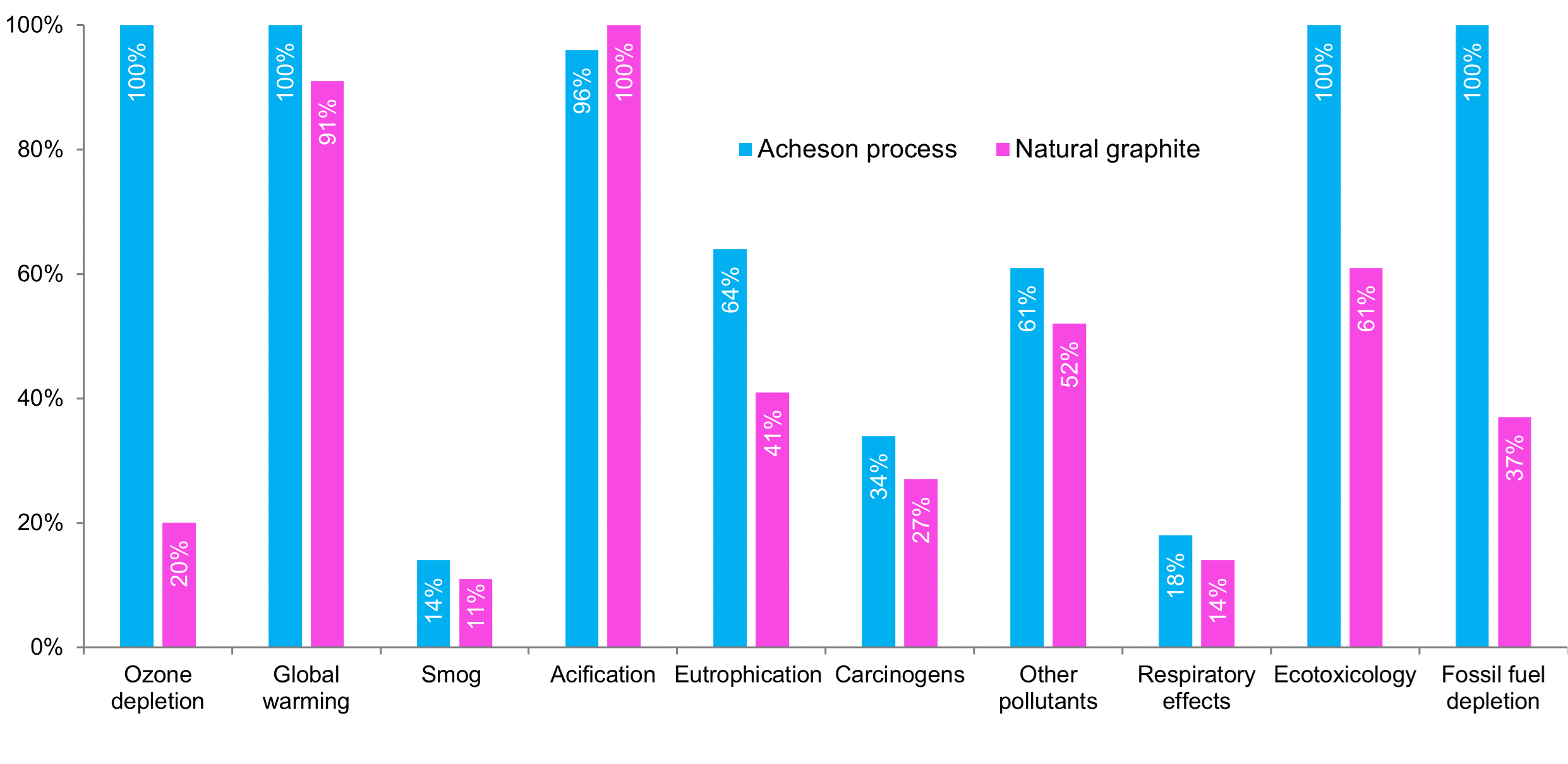
Source: SFA (Oxford), Kulkarmi et al., 2022
In conclusion, the industrial processes used in China cannot be readily transferred to Europe and North America. Therefore, companies developing domestic graphite production will require more investment to reduce emissions and pollution and better manage waste.
China controls 65-75% of global graphite production
Natural graphite is mined from ore deposits and comes in three forms of natural graphite: amorphous (low quality), flake (small, medium and large size) or vein (high quality). The source of battery-grade graphite is low to medium-flake graphite. However, the current production process is highly inefficient and does not scale well. It takes three tonnes of flake graphite to produce one tonne of battery-grade graphite, and the negative environmental impact of the graphite industry in China on surrounding communities has been well-documented.
Commercial-scale graphite mining in China moved from the eastern province of Shandong to the north-eastern province of Heilongjiang and the north Inner Mongolia region due to a depletion of ore reserves. The ores in the country are fine flake (60%) and amorphous (40%), and processing produces a substantial volume of particulate emissions, not to mention wastes from acid leaching, which has greatly impacted surrounding communities. While the central government in China has directed industry consolidation and introduced inspections at all levels of the value chain, the finer the flake, the more expensive and environmentally damaging it is to process into a battery-grade product. In general, the quality of natural flake graphite is inconsistent as deposits can differ greatly, and there can be a significant yield loss if particles are too fine to go through the spheroidisation step needed to produce the coated, spherical purified graphite (CSPG) needed for battery grade applications.
Life cycle assessment from natural graphite anode production
kg CO2 eg / t anode graphite
Natural and synthetic graphite prices
CNY/Mt
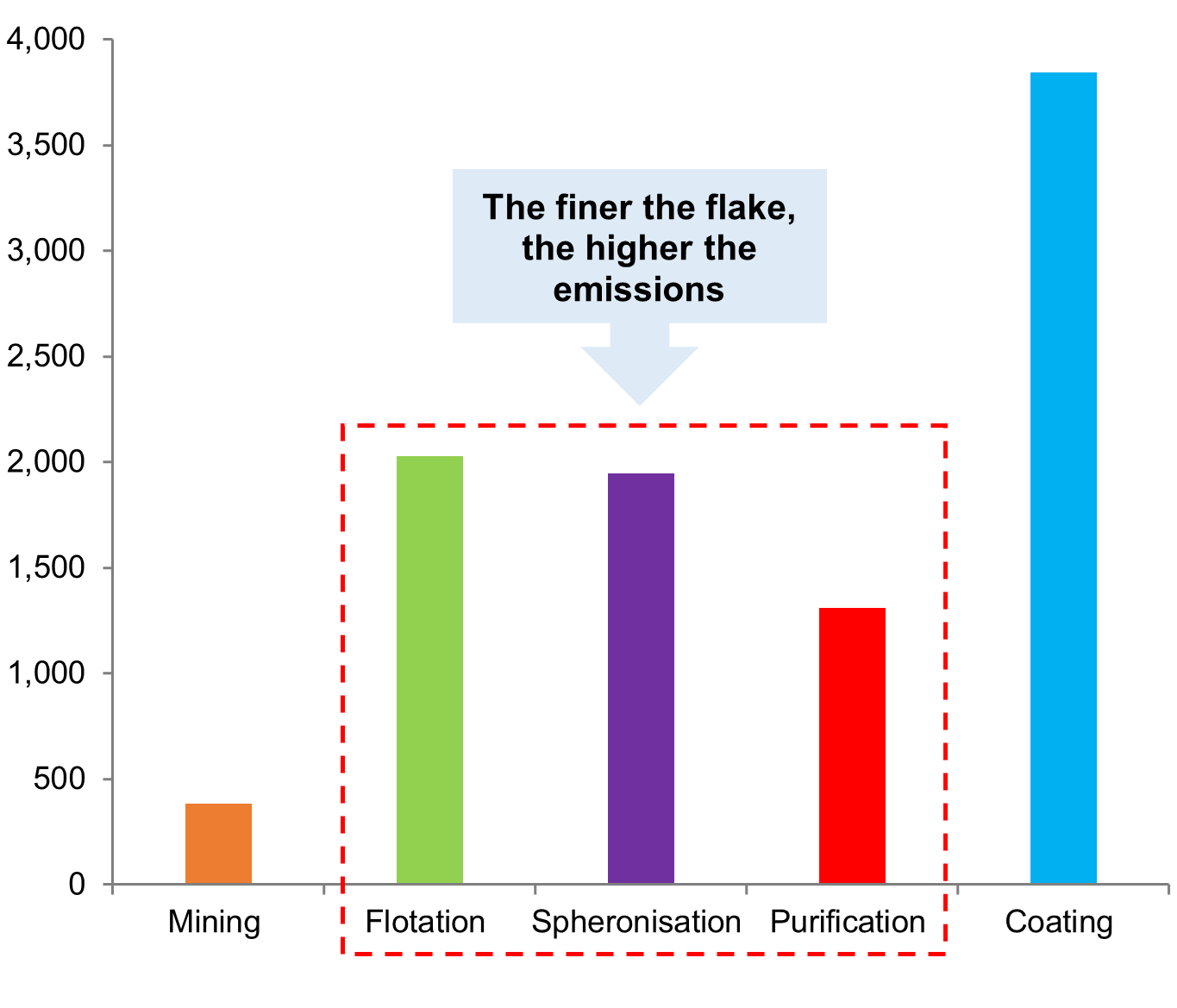
SFA Oxford, SMM, Engels et al. 2022
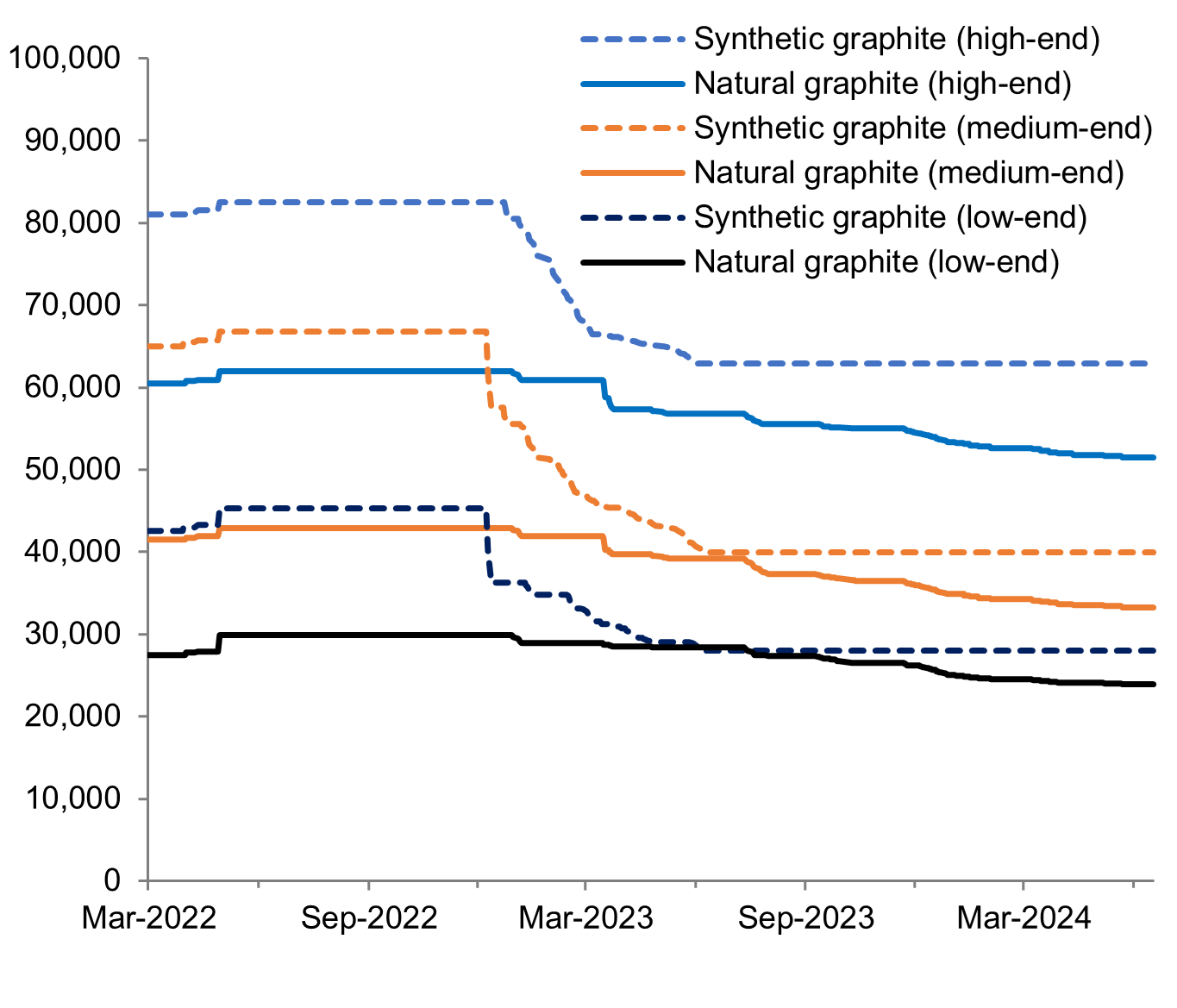
Natural graphite deposits are unique as quality is assessed by both purity and flake size, and these characteristics determine application. For example, higher-priced, larger graphite flakes are used in refractories such as steel ladles, basic oxygen furnaces (BOF), and electric arc furnaces (EAF). The general rule is that the smaller the flake size, the more resources (and emissions) are involved to get the required yields. Therefore, medium flake size is the sweet spot for LiB applications.
-
North America: Graphite mine production in the US ceased in 1994, but a few companies are developing mine assets in the Alaska and the Alabama graphite belt. Canada has about 5.7 million tonnes of graphite reserves, and Quebec has the only operating mine in North America, Northern Graphite’s Lac des Iles mine, which produced 13 in 2022. Furthermore, Nouveau Monde was developing a mining asset north of Montreal and broke ground to build an anode facility in Bécancour, targeting 43 ktpa of capacity.
-
Europe: The European Commission published a critical mineral study on graphite to increase domestic output and flake deposits in Czechia, Finland, Germany, Sweden and Norway are being assessed for development or expansion. In addition, the Australia-based Talga Group has commissioned a graphite anode plant in Luleå, Sweden, close to the company’s graphite resources 61in Vittangi, and received final environmental approval last June.
-
Africa: Mine production in Mozambique has more than doubled to 170 kt; in Madagascar, it has risen by 57% to 110 kt. In addition, Tanzania had no mine production in 2021, but 8 kt in 2022 and this is expected to grow substantially over the next five years. Of particular note, Syrah Resources closed a $102 million loan to expand its US anode processing plant in Louisiana and was selected for up to $220 million in grants from the US DOE. The feedstock will come from the company’s 350 ktpa Balama mine operation in Mozambique, which has been in production since 2017. A life-cycle assessment concluded that the plant has a global warming potential of 7.3 kg CO2 eq./kg anode active material (AAM), roughly half that of natural graphite produced in China.
The US has a competitive advantage in synthetic graphite
Synthetic graphite is a man-made substance that is produced through the high-temperature processing of amorphous carbon feedstocks such as petroleum, coal, or natural and synthetic organic compounds. However, not all precursor material can be graphitised as the process requires a rearrangement of carbon atoms in a certain manner before the heat treatment phase. Compared to natural graphite, synthetic graphite has a lengthier and more carbon-intensive production process. It takes up to 4-5 months to attain the crystallisation necessary to produce artificial graphite versus 3-5 days for natural graphite, resulting in the significant price discrepancy between the two forms.
Needle coke is a precursor material for synthetic graphite typically derived from petroleum coke or coal-tar pitch. Although it is a by-product of well-established industrial processes, needle coke production is energy-intensive and inefficient. In addition, only 5% of petroleum coke feedstock meets the high purity and structural specifications to produce synthetic graphite. Therefore, the processes used to produce synthetic graphite are varied and complex, and standardisation may not be possible.
-
Petroleum coke is the primary precursor material used to produce needle coke in the US, as the country accounts for more than 40% of global production. The product of leftover residue from the coking process used in the oil-refining industry, petroleum coke, must be specified to ensure it results in high-quality graphite. The reality is that the by-products of crude oil streams can differ significantly in quality and synthetic graphite can only be produced from the highest-grade crude oils that are high in aromatic organics content (e.g. decanted heavy gasoil of catalytic cracking, heavy pyrolysis resin.
-
Many petroleum refineries do not have the required delayed coker units and there is a lack of industry coordination among the raw material producers, intermediate producers, and the battery industry. Some technical constraints must be overcome, as the initial petroleum coke product is a solid, non-melting carbon containing several volatile organic compounds that must be removed or turned into calcined petroleum coke, typically by a rotary kiln. GrafTech is the leading company that produces needle coke from petroleum coke to produce graphite electrodes for electric arc furnaces.
-
Coal-tar pitch is the residue from the distillation of coal tar ‒ a by-product of the coking, liquefaction, or gasification of coal. Only three companies in the world outside of China produce needle coke from coal-tar pitch: Mitsubishi, the first company to successfully produce coal-based needle coke, C-Chem and POSCO Chemicals.
For more information on midstream graphite production and competing technologies in development, please see our Q2 Battery Metals Quarterly report out July 5
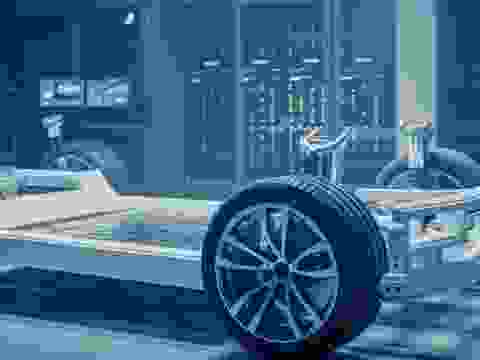
Brought to you by
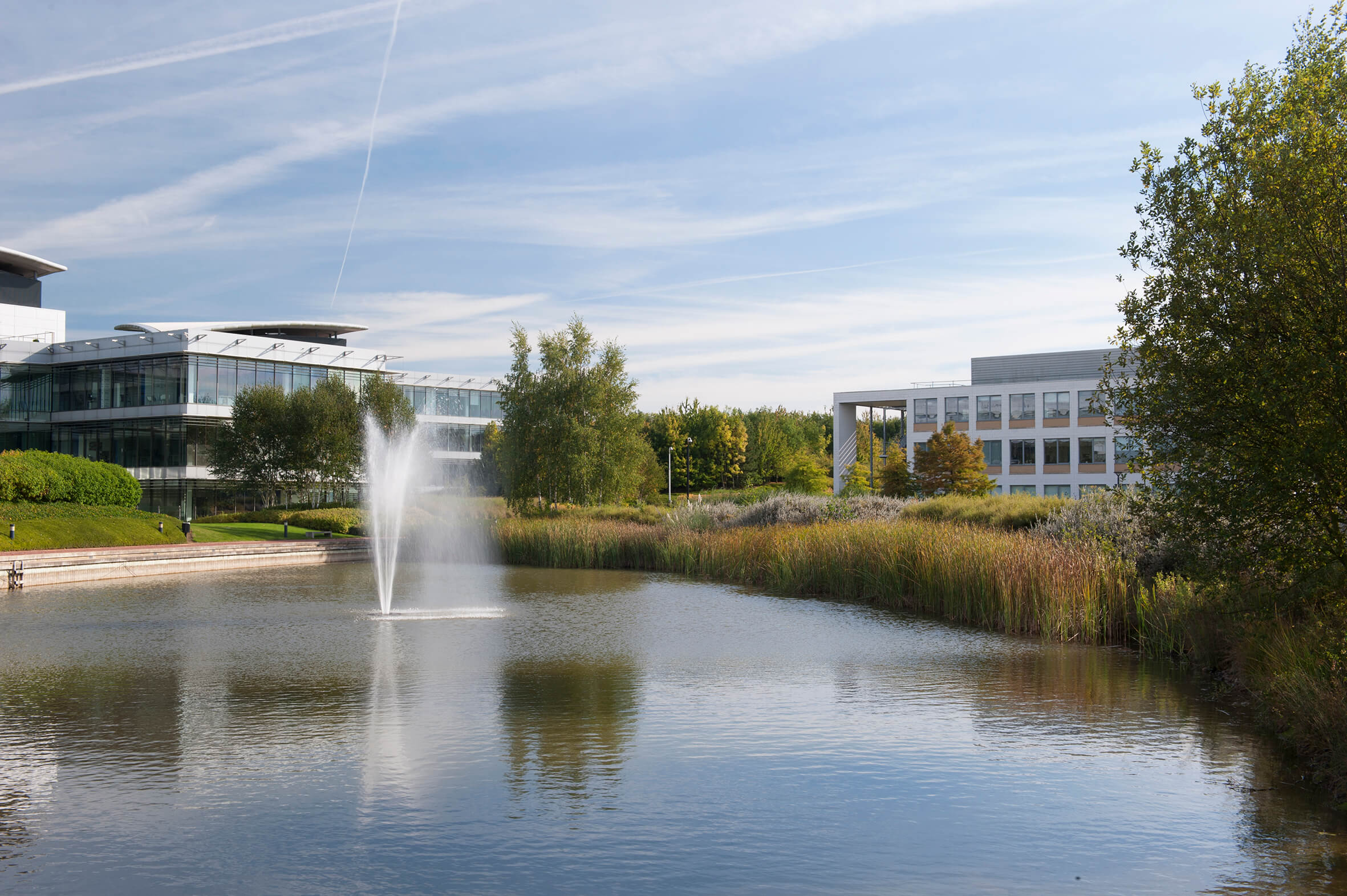
How can we help you?
SFA (Oxford) provides bespoke, independent intelligence on the strategic metal markets, specifically tailored to your needs. To find out more about what we can offer you, please contact us.