Additive Manufacturing
Critical minerals, policy, and the energy transition
Critical Minerals and Additive Manufacturing
Additive Manufacturing (AM), commonly known as 3D printing, has revolutionised the production of high-performance components across various industries, including aerospace, automotive, energy, and medical sectors. This transformative technology enables the creation of complex geometries, lightweight structures, and highly optimised materials that would be challenging or impossible to produce using conventional manufacturing methods. At the core of AM’s success lies a diverse range of critical minerals—elements essential for producing advanced alloys and high-performance materials. These minerals enhance mechanical strength, thermal stability, corrosion resistance, and overall efficiency in demanding applications. From titanium and aluminium in aerospace to tungsten and niobium in high-temperature environments, each element plays a crucial role in advancing modern engineering and manufacturing. Here we explore their key applications, and how they contribute to the development of next-generation materials for industries that demand precision, strength, and sustainability.
Aerospace and lightweight structural components
Lightweight materials are crucial in aerospace, automotive, and high-performance engineering, where strength, durability, and weight reduction enhance fuel efficiency and structural integrity. 3D printing has revolutionised the use of lightweight alloys, enabling the creation of complex geometries and lattice structures that significantly reduce weight while maintaining strength. Additive Manufacturing (AM) techniques such as Powder Bed Fusion (PBF), Directed Energy Deposition (DED), and Selective Laser Melting (SLM) facilitate the production of high-strength, corrosion-resistant, and fatigue-resistant components for aircraft, spacecraft, and advanced automotive systems.
By leveraging AM-enabled topology optimisation, materials like aluminium, magnesium, and titanium can be designed to maximise strength while minimising weight. This allows for aerodynamically optimised, customised components with improved efficiency and sustainability, reducing production costs and material waste.
-
Magnesium – A key element in 3D-printed aluminium-magnesium alloys, reducing weight while maintaining structural integrity. AM processes such as Selective Laser Melting (SLM) and Powder Bed Fusion (PBF) optimise Mg-based alloys for aerospace applications, enhancing fuel efficiency.
-
Aluminium – Widely used in aerospace structural components, cabin interiors, and aircraft fittings due to its low density and high stiffness-to-weight ratio. AM techniques such as Laser Powder Bed Fusion (LPBF) and Binder Jetting enhance mechanical properties, making aluminium ideal for fuselages, space vehicle components, and structural supports.
-
Silicon – Enhances aluminium-magnesium alloys, improving castability, stiffness, and thermal stability. AM techniques like PBF and SLM ensure strong, thermally stable alloys for high-performance aerospace and automotive applications.
-
Scandium – Strengthens aluminium alloys for lightweight aerospace fittings. LPBF and DED improve strength, corrosion resistance, and fuel efficiency.
-
Titanium – Essential in aerospace and medical applications, offering high strength-to-weight ratios and superior corrosion resistance. Electron Beam Melting (EBM) and Direct Metal Laser Sintering (DMLS) enable the creation of intricate titanium structures for aircraft fuselages, jet engines, and space exploration components.
Superalloys and high-temperature applications
Superalloys are essential in aerospace, defence, and energy industries, where extreme heat resistance, oxidation protection, and mechanical stability are required. 3D printing enables the production of high-strength, lightweight components capable of withstanding extreme temperatures and mechanical stress. AM processes such as PBF, DED, and EBM allow precise microstructural control, optimising strength, durability, and creep resistance in high-temperature environments.
AM enhances turbine blade design, engine efficiency, and thermal protection systems, reducing weight and improving heat dissipation. Additionally, 3D printing minimises material waste and accelerates production.
-
Chromium – Enhances corrosion resistance in aerospace turbine engines and medical implants. SLM and DED integrate Cr into superalloys for durability and oxidation protection.
-
Manganese – Enhances tensile strength and toughness in Ni-based superalloys. AM ensures precise Mn incorporation for optimised performance.
-
Cobalt – Integral to CoCr superalloys in gas turbines and medical implants, offering strength, wear resistance, and corrosion protection. AM techniques like DMLS and PBF ensure precision in microstructural control.
-
Nickel – Found in aerospace turbine blades and engine components due to high-temperature stability and oxidation resistance. LPBF and EBM refine microstructures for improved performance.
-
Copper – Improves thermal conductivity in high-temperature alloys, benefiting aerospace, defence, and energy applications. DED and PBF facilitate customised Cu-based superalloys.
-
Niobium – Strengthens titanium-aluminium alloys (Ti-Al-Nb) for aerospace engines and structural applications. AM optimises mechanical stability and thermal efficiency.
-
Hafnium – Critical in nickel-based superalloys for aerospace turbines, improving creep resistance and mechanical performance. PBF and LMD optimise Hf-enhanced materials.
-
Tungsten – Used in heat-resistant superalloys for aerospace turbines and high-performance tool steels. LPBF and Binder Jetting create durable tungsten-based components.
Strengthening and structural alloys
Structural alloys are vital in aerospace, automotive, and industrial applications, requiring high strength, durability, and corrosion resistance. 3D printing enables the production of lightweight, high-performance components previously difficult to manufacture. AM techniques like PBF, DED, and SLM optimise strength, weight reduction, and fatigue resistance in high-performance engineering.
-
Vanadium – Increases strength and temperature stability in Ti-Al alloys. LPBF and SLM fabricate lightweight yet high-strength Ti-V components.
-
Iron – Used in 3D-printed stainless steel alloys for engine components and structural applications. LPBF and Binder Jetting enhance strength-to-weight ratios and resistance to extreme conditions.
-
Zirconium – Found in titanium alloys and bulk metallic glasses for precision structural components. AM fine-tunes Zr alloys for improved wear resistance and durability.
-
Molybdenum – Strengthens titanium alloys for aerospace and defence applications. DED and EBM precisely distribute Mo in Ti-based alloys for optimal stability.
Corrosion resistance and medical applications
Corrosion-resistant materials are critical in medical, dental, and biomedical engineering. 3D printing allows for patient-specific implants with improved biocompatibility, osseointegration, and longevity. AM techniques such as PBF, EBM, and SLM enable precise control of porosity, surface texture, and mechanical properties.
-
Titanium – Used in medical implants due to biocompatibility, high strength, and corrosion resistance. AM techniques like EBM and SLM create porous structures that integrate well with bone.
-
Chromium – Enhances corrosion resistance in medical implants. AM techniques like LPBF enable the fabrication of customised, high-strength CoCr and stainless steel implants.
-
Cobalt – Key in orthopaedic implants, dental prosthetics, and cardiovascular devices. AM processes like PBF and DMLS ensure high precision and durability.
Energy and nuclear applications
3D-printed materials play a crucial role in nuclear reactors and radiation shielding, where extreme temperature resistance and structural integrity are required. AM processes like PBF and DED enhance performance and safety in these high-stress environments.
-
Zirconium – Used in nuclear reactor components for its high corrosion resistance and neutron transparency.
-
Hafnium – Essential in nuclear control rods due to its neutron absorption capability and thermal stability.
-
Tungsten – Provides radiation shielding and extreme heat resistance in fusion reactors.
Space and hypersonic applications
Materials for space exploration and hypersonic vehicles require extreme heat resistance and structural durability. AM enables the production of lightweight, heat-resistant components for propulsion systems, re-entry shields, and spacecraft.
-
Niobium – Used in rocket nozzles and propulsion systems for heat resistance.
-
Hafnium – Strengthens superalloys for hypersonic aircraft and space vehicles.
-
Tungsten – Applied in spacecraft propulsion, heat shields, and thermal protection systems.
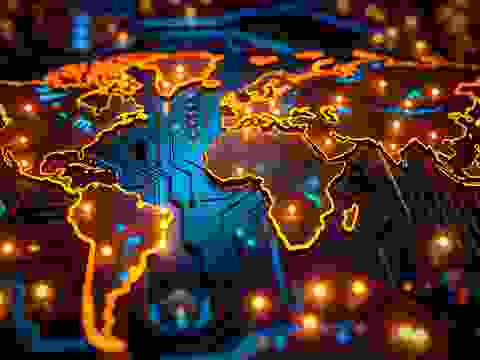
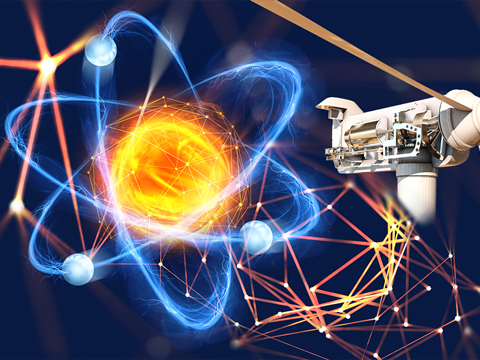
Critical sectors using strategic minerals
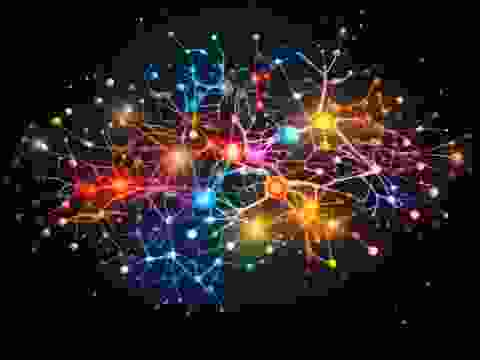
Meet the Critical Minerals team
Trusted advice from a dedicated team of experts.
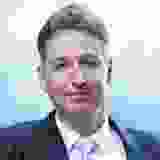
Henk de Hoop
Chief Executive Officer
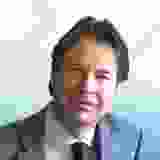
Beresford Clarke
Managing Director: Technical & Research
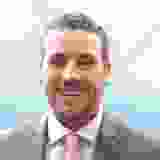
Jamie Underwood
Principal Consultant
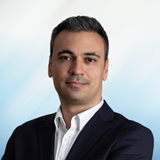
Ismet Soyocak
ESG & Critical Minerals Lead
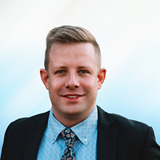
Rj Coetzee
Senior Market Analyst: Battery Materials and Technologies
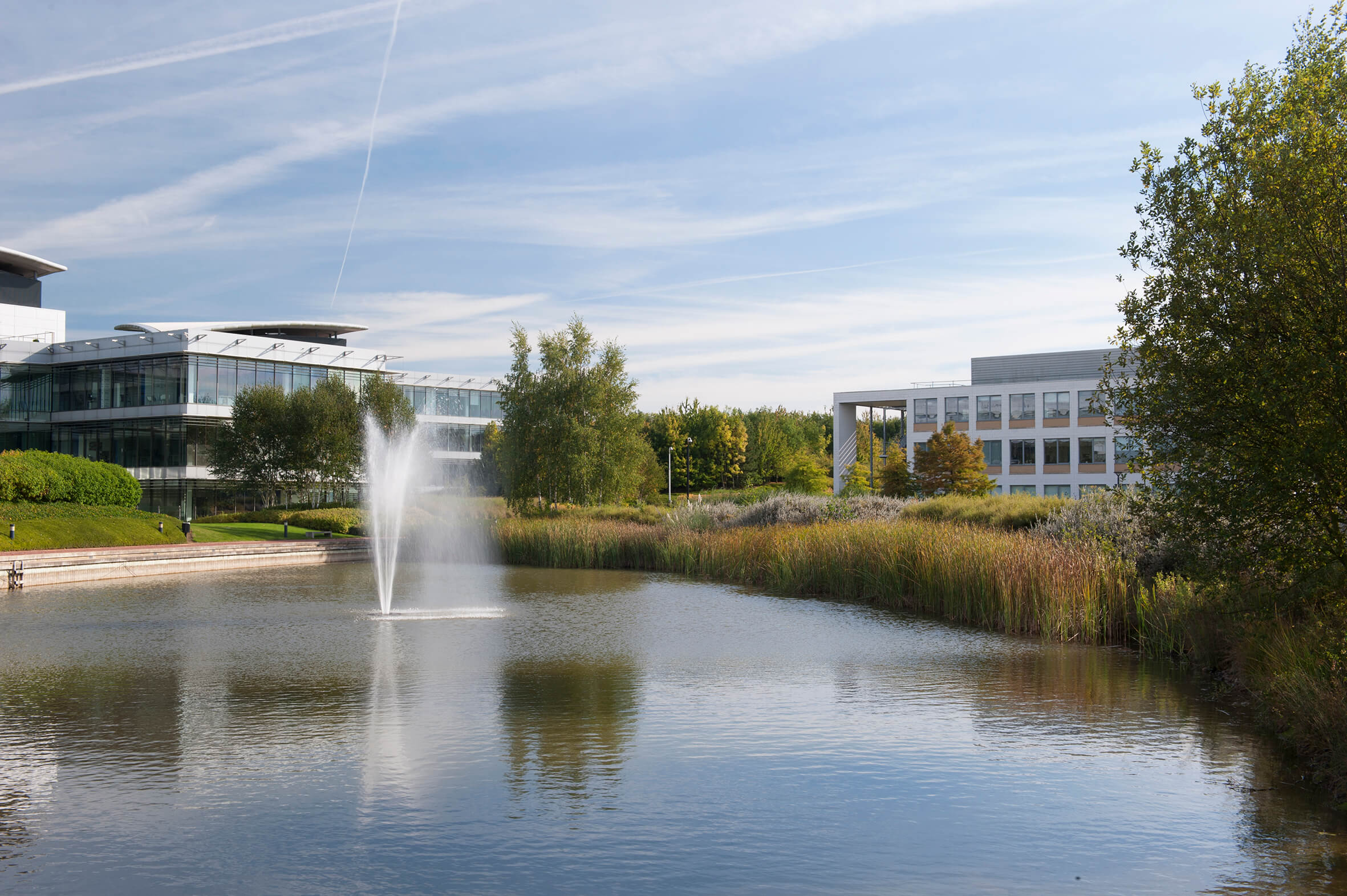
How can we help you?
SFA (Oxford) provides bespoke, independent intelligence on the strategic metal markets, specifically tailored to your needs. To find out more about what we can offer you, please contact us.