Space development
Critical minerals, policy, and the energy transition
Critical Minerals and Space Technologies
The modern space sector encompassing satellite communications, Earth observation, deep space exploration, and launch vehicle innovation is increasingly dependent on a diverse range of critical minerals. As nations and private enterprises invest in space as both a strategic domain and a commercial frontier, the demand for specialised materials has grown in parallel. From lightweight alloys and thermal-resistant composites to rare elements essential for sensors, optics, propulsion, and electronics, critical minerals underpin every stage of space technology. In an era defined by intensifying geopolitical competition, shifting energy policies, and mounting supply chain pressures, securing access to these minerals has become a pivotal concern for governments and industry stakeholders alike.
Policy implications of critical minerals in space technology
The increasing reliance on critical minerals in the space sector has significant policy implications, both domestically and globally. As space emerges as a domain of strategic competition, encompassing commercial, scientific, and defence dimensions, governments are moving to secure access to the materials that underpin space technologies. From rare-earth magnets and radiation-hardened semiconductors to high-performance alloys and propellants, the minerals enabling satellite communications, space exploration, and orbital infrastructure are becoming central to national critical minerals strategies.
In the United States, the CHIPS and Science Act (2022) has expanded funding for semiconductor and advanced materials development, supporting space-grade electronics and power systems. The U.S. Department of Defense has also invested in domestic rare-earth processing capabilities to reduce dependence on external sources for magnets used in satellite attitude control and deep-space probes.
The European Space Agency's (ESA) Agenda 2025 identifies materials security as a pillar of European strategic autonomy, encouraging investment in recycling and substitution technologies for critical minerals. Canada’s Critical Minerals Strategy recognises space as a high-value, dual-use domain where secure access to materials like titanium, nickel, and cobalt is vital for both civilian and defence applications.
Moreover, the rising cost and scarcity of noble gases such as xenon and krypton have prompted policy dialogues on propellant reuse and recycling. Japan’s Basic Plan on Space Policy integrates space resource development, including in-situ resource utilisation (ISRU) and asteroid mining, into broader supply chain resilience efforts.
Multilateral organisations like the United Nations Office for Outer Space Affairs (UNOOSA) are beginning to consider frameworks for resource governance beyond Earth. In this evolving context, critical mineral policy intersects with export controls, trade strategy, supply chain mapping, and the regulation of emerging technologies.
Securing the critical minerals that underpin space exploration and satellite technology is no longer a purely technical concern—it has become a strategic imperative. As the geopolitical stakes of space dominance rise, the intersection of material science, aerospace innovation, and international competition is reshaping national policy agendas.
Governments are increasingly focused on enhancing supply chain transparency and resilience to ensure uninterrupted access to essential elements. Disruptions, whether due to geopolitical tensions, trade restrictions, or limited global production can threaten satellite networks, navigation systems, and advanced space missions.
To mitigate these risks, countries are investing in domestic processing and recycling capabilities. By closing the loop on critical mineral usage, these efforts aim to reduce reliance on volatile import routes while fostering more sustainable resource management.
Export controls and import regulations are also being refined to protect strategic technologies and materials. High-tech compounds and rare earths vital to aerospace applications are now frequently subject to national security reviews, reflecting their growing importance in both civil and military domains.
In parallel, public and private funding is being directed toward research on substitute materials and advanced alloys that can enhance performance or reduce dependence on supply-constrained elements. This innovation push supports long-term resilience in satellite and spacecraft manufacturing.
Finally, as space mining and off-world manufacturing inch closer to reality, nations are promoting international norms for in-situ resource utilisation (ISRU). Establishing cooperative frameworks for lunar and asteroid mining is becoming a diplomatic priority.
Structural materials and alloys
The extreme conditions of space, including vacuum, radiation, micrometeorites, and dramatic temperature fluctuations, require materials with exceptional performance characteristics. The following metals and alloys underpin spacecraft, satellites, and space infrastructure, enabling missions that would otherwise be impossible.
-
Titanium – Titanium's exceptional strength-to-weight ratio is indispensable in space applications, where every gram counts. The Ti-6Al-4V alloy is widely preferred for spacecraft structural components due to its outstanding mechanical properties.Titanium inserts serve as critical mounting points, securing devices to spacecraft and satellites while handling heavy loads at minimal weight. Optimised designs created via 3D metal printing significantly reduce weight compared to traditional manufacturing methods, enhancing structural properties, increasing payload capacity, and offering substantial launch cost savings.Moreover, titanium effectively mitigates thermo-elastic stresses in spacecraft. Titanium inserts installed during the curing process of carbon fibre-reinforced polymers manage these stresses, preserving structural integrity amid extreme temperature fluctuations in space.
-
Aluminium – Aluminium alloys form the basis of most spacecraft structures, providing an ideal balance of low density and robust mechanical performance. Aluminium alloys have been central to aerospace manufacturing since the introduction of metal-skinned aircraft.Alloy series such as 2XXX, 5XXX, 7XXX, and 8XXX offer custom solutions for specific requirements. Aluminium-magnesium alloys, in particular, are advantageous in space applications due to their reduced density and lower flammability compared to other aluminium alloys.Crossover aluminium alloys are specially designed for use in environments exposed to intense radiation. They are strengthened through a process called 'precipitation hardening,' forming a chemical structure known as the T-phase. This gives the alloys excellent resistance to radiation damage, ensuring spacecraft remain structurally strong during long-term missions facing constant solar radiation.
-
Vanadium – Vanadium plays a key role in enhancing the strength and performance of titanium alloys commonly used in aerospace applications. One of the most widely used alloys is Ti-6Al-4V, which contains 6% aluminium and 4% vanadium. This alloy is especially favoured for critical aerospace components that undergo significant stress.Adding vanadium enables specialised heat treatments that create alloys capable of maintaining their strength at high temperatures—up to approximately 545°C. Such thermal stability is crucial for spacecraft components exposed to extreme temperature variations, including during atmospheric re-entry or within propulsion systems.Emerging titanium alloys with higher vanadium content (8%, 10%, and 15%) are currently under development. These alloys offer the potential for even greater strength, which could lead to significant weight reductions in next-generation spacecraft.
-
Nickel – Nickel-based superalloys are essential in space propulsion systems, particularly for components that must withstand extreme temperatures. These alloys offer exceptional thermal stability and corrosion resistance, crucial for parts such as injectors and thrusters that experience intense thermal stresses during operation.Nickel alloys are valued for their ability to maintain strength and structural integrity at high temperatures, significantly reducing the risk of catastrophic failure in propulsion systems. Additionally, advances in nickel alloy additive manufacturing have opened new possibilities for designing complex propulsion components, enabling shapes and structures that are challenging or impossible to create through conventional manufacturing methods.
-
Cobalt – Cobalt-based superalloys play a vital role in space applications that require exceptional resistance to very high temperatures. Unlike nickel-based alloys, cobalt alloys achieve their strength through different mechanisms, offering superior resistance to hot corrosion and thermal fatigue, qualities essential in demanding space environments.Due to cobalt’s higher melting point compared to nickel, cobalt-based superalloys are particularly suited to components that experience lower stress but operate at higher temperatures, such as stationary vanes in gas turbines. Recent advancements in cobalt-based superalloys with γ/γ' microstructures have significantly enhanced their performance, making them increasingly suitable for applications demanding both high-temperature capability and low density.Continuous improvements in cobalt-based superalloys are broadening their potential uses in space systems, especially for components that must reliably maintain structural integrity under severe thermal conditions.
-
Chromium – Hard chrome plating provides outstanding hardness, wear resistance, adhesion, and corrosion protection—key properties for equipment exposed to harsh space conditions. These characteristics make chromium plating an essential technology for significantly improving the durability and reliability of space hardware components.Traditional lubricants are ineffective or problematic in the vacuum of space. Chromium's natural lubricity (low coefficient of friction) allows components to move smoothly with minimal friction, which is essential for moving parts like hinges, valves, and bearings in space equipment. This property reduces the risk of mechanical failures that could compromise mission success.Additionally, chromium's excellent heat resistance helps components dissipate heat and provides thermal stability, enabling equipment to operate efficiently despite extreme temperature fluctuations. The weight savings offered by chromium coatings compared to alternative materials further contribute to the efficiency of space missions by reducing fuel consumption and increasing payload capacity.
-
Magnesium – Magnesium is highly attractive for space applications due to its exceptionally low density (0.063 lb/in³ compared to aluminium’s 0.100 lb/in³), making it ideal for minimising weight. Although magnesium alloys are generally not as strong as aluminium alloys, their low density ensures they remain competitive in terms of specific strength and stiffness.The excellent damping properties of magnesium alloys make them particularly useful in environments with significant vibrations, potentially reducing structural fatigue in spacecraft during launch and operation. However, magnesium alloys typically have poorer corrosion resistance, posing challenges for long-duration space missions. Recent advances in alloy development have significantly improved corrosion resistance, bringing it closer to that of aluminium alloys and expanding magnesium’s potential applications in space structures.
-
Beryllium – Beryllium offers an exceptional combination of very low density, high stiffness, and excellent dimensional stability across a wide temperature range. These characteristics make it highly valuable for applications demanding precise alignment and stability, including optical systems and scientific instruments used in space telescopes. In particular, space telescopes and optical systems utilise beryllium for mirrors and structural supports requiring precision alignment, minimal thermal distortion, and lightweight properties, such as the mirror segments of the James Webb Space Telescope. Similarly, satellite guidance and navigation systems rely on beryllium for components like gyroscopes, sensors, and precision instrument housings that must remain stable despite thermal fluctuations.The thermal stability of beryllium ensures that precision components maintain their dimensions and alignment even during extreme temperature fluctuations encountered in space. However, the toxicity and challenging machinability of beryllium have restricted its use primarily to these specialised applications, where the advantages of its unique properties outweigh the complexities involved in manufacturing.
-
Tungsten - Tungsten’s exceptionally high melting point and outstanding thermal stability make it indispensable for space components exposed to extremely high temperatures, especially within propulsion systems. Research indicates that tungsten fibre-reinforced composites significantly enhance high-temperature strength and enable considerable weight reductions in high-temperature space power systems.
Tungsten’s superior creep resistance is particularly advantageous for long-duration space missions, ensuring that components maintain dimensional stability under sustained high-temperature loads. This reliability is crucial for the consistent operation of spacecraft propulsion systems during extended, multi-year missions.
-
Niobium - Niobium significantly improves the thermal resistance of alloys used in critical high-temperature applications such as rocket nozzles and thrusters. Research into tungsten fibre-reinforced niobium composites has shown considerable promise for meeting the demanding requirements of advanced space power systems, particularly in terms of increased temperature tolerance and improved creep resistance.Space power systems are essential technologies that generate, store, and distribute electrical power onboard spacecraft. Examples include solar arrays, radioisotope thermoelectric generators (RTGs), fuel cells, batteries, and nuclear power systems.For these systems, maintaining dimensional stability and performance over long durations is essential. Niobium-based composites excel here, providing excellent long-term creep resistance, even under sustained exposure to high temperatures and mechanical stress during extended missions.
-
Low Earth Orbit (LEO) satellites require materials that withstand atomic oxygen erosion, radiation, and thermal cycling between -150°C and +150°C. Niobium’s naturally occurring oxide layer (Nb₂O₅) provides inherent protection against oxidative degradation, while its high thermal emissivity (0.7–0.8) enables passive temperature regulation. Lockheed Martin’s LM 2100 satellite bus employs niobium alloy RF waveguides and optical bench structures to maintain dimensional stability during rapid day-night transitions.
-
Rocket motor nozzles present even greater material challenges, with combustion gases exceeding 3,500°C in solid-fuel systems. Niobium C-103’s oxidation resistance is augmented by silicide coatings that form a self-healing SiO₂ layer at high temperatures, allowing SpaceX’s Raptor engines to achieve 330-bar chamber pressures in reusable configurations.
- China’s 2025 breakthrough in niobium-silicon-hafnium (Nb-Si-Hf) alloys aboard the Tiangong space station highlights microgravity’s potential for advanced metallurgy. The absence of buoyancy-driven convection ensures uniform dispersion of hafnium dopants (<0.5 wt%), tripling room-temperature fracture toughness to 25 MPa·m¹/² while maintaining a 1,700°C operational limit. Processed via microgravity rapid solidification, these alloys achieve 1.7 GPa compressive strength at 1,700°C while eliminating room-temperature brittleness through hafnium-doped grain boundary strengthening. Such advances could enable hypersonic missiles with 50% greater range and reusable platforms with extended endurance and shorter thermal recharge cycles.
Advanced composites and ceramics
Advanced composites and ceramics are high-performance materials used primarily for structural and shielding components in spacecraft. Compared to traditional aluminium designs, these materials collectively reduce spacecraft mass by 30–60%, while extending mission lifetimes from 5 years up to more than 15 years, essential for sustained interplanetary exploration.
-
Carbon – Carbon is widely used in structural composites, including satellite panels, rocket fairings, and spacecraft frames. Additionally, carbon-based shielding panels provide essential thermal protection for orbital spacecraft and re-entry vehicles. Emerging materials, such as carbon nanotubes, are currently being explored to construct ultra-lightweight truss structures, while graphene-enhanced composites show promise in advanced thermal management systems.Carbon composites offer exceptional properties, including a superior strength-to-weight ratio, being five times stronger than steel at only 20% of its weight. This dramatically improves fuel efficiency, reduces launch costs, and increases payload capacity. Moreover, carbon-based materials exhibit outstanding thermal stability, maintaining structural integrity across extreme temperatures ranging from –180°C to +1,650°C, essential during orbital manoeuvres and lunar surface operations. Additionally, carbon-carbon composites possess enhanced radiation tolerance, significantly reducing secondary radiation effects compared to metal alloys and thereby safeguarding sensitive spacecraft electronics.
-
Recent innovations, such as 3D-printed carbon lattice structures, integrate advanced topology optimisation with customised porosity, achieving a remarkable 97% mass reduction in non-critical structural zones without sacrificing load-bearing capacity. Looking forward, the future of carbon composites in space applications includes in-situ manufacturing, where lunar-regolith-derived carbon fibres could be used to 3D-print structures such as lunar launch pads. This technology would greatly reduce dependence on Earth-based resources, enabling sustainable and cost-effective space exploration.
-
Kevlar®(Aramid Fibres) – Kevlar® is highly valued in spacecraft construction for its exceptional strength, impact resistance, and thermal properties. It is extensively used as multilayer insulation (MLI) to shield satellites from micrometeoroids and orbital debris. Kevlar’s vibration-damping properties make it ideal for use in honeycomb cores within spacecraft flooring and control surfaces, reducing structural fatigue during launch and operation. Additionally, Kevlar® is crucial for pressurised systems, forming filament-wound gas containment vessels designed to resist fragmentation under extreme conditions.
-
Kevlar’s outstanding radiation-shielding capability is also critical in space: a Kevlar® layer of just 10 g/cm² can reduce cosmic ray exposure by over 50%, significantly outperforming aluminium-based shielding in environments dominated by proton radiation. Its remarkable impact resistance, absorbing between 80–120 kJ/m², protects spacecraft from damage by orbital debris travelling at speeds up to 7 km/s. Furthermore, Kevlar’s low thermal conductivity (0.04 W/m·K) and flame resistance (stable below its decomposition threshold of approximately 500°C) make it an ideal material for thermal insulation.
-
In practice, NASA’s Artemis programme employs Kevlar®-reinforced aerogels in lunar lander legs, achieving 40% mass reduction compared to traditional aluminium designs. These aerogels also withstand extreme temperature spikes of up to 1,200°C during descent engine burns, demonstrating the material’s superior performance under severe thermal conditions.
-
Looking to future advancements, Kevlar®-templated graphene aerogels—classified as quantum materials, offer ultra-low thermal expansion (below 0.1 ppm/°C). This exceptional property makes them ideal for precision instruments, enhancing accuracy and reliability in space-based applications.Kevlar®, carbon, and silicon carbide (SiC) combine effectively across various spacecraft systems to enhance performance; for example, re-entry thermal protection systems (TPS) utilise carbon as the outer ablative protective layer, Kevlar® as mid-layer insulation, and silicon carbide as the underlying hot structural substrate, while in ion thrusters, carbon functions as grid electrodes, Kevlar® is employed for insulation bushings, and silicon carbide provides the lining for the discharge chamber due to its thermal durability. Additionally, space telescopes, such as the James Webb Space Telescope, feature carbon in optical benches, Kevlar®-reinforced membranes in sunshield layers, and silicon carbide as the substrate material for primary mirrors, ensuring dimensional stability under thermal fluctuations.
-
A notable example of these combined advantages is the James Webb Space Telescope's sunshield, which uses five Kevlar®-reinforced membrane layers coated with carbon nanotubes. This configuration effectively manages a thermal gradient of 300:1, while dedicating less than 1% of the telescope’s total mass to thermal control systems.
-
Silicon carbide ceramics – Silicon carbide (SiC) ceramics are extensively utilised in demanding space applications due to their exceptional thermal, mechanical, and radiation-resistant properties. In propulsion systems, SiC serves as a critical material for nozzle throats in solid rocket motors, reliably withstanding exhaust gas temperatures exceeding 3,000°C. Optical systems, including precision space telescopes, employ SiC for dimensionally stable mirrors, benefiting from its exceptionally low coefficient of thermal expansion (CTE) of 2.4×10⁻⁶/°C. Additionally, in nuclear systems, SiC acts as a neutron-transparent cladding material in space-based fission reactors, with neutron transparency measured at only 0.12 barns.Key properties contributing to SiC’s value in space include outstanding thermal resistance, with the material retaining 85% of its flexural strength even at temperatures as high as 1,400°C, enabling its use in reusable launch vehicle components. Its extreme hardness, measured at 28 GPa on the Vickers scale, provides robust protection against micrometeoroid erosion encountered in low Earth orbit. Furthermore, SiC ceramics demonstrate remarkable radiation immunity, experiencing less than 0.1% dimensional change after exposure to intense neutron radiation (10¹⁸ neutrons/cm²), making them ideal for extended deep-space missions.
-
A practical example is NASA’s Mars Sample Return mission, which uses reaction-bonded SiC wheels on sample caches. These wheels offer twice the abrasion life compared to conventional alumina ceramics under simulated Martian dust conditions.
Propellants and pressurisation gases
Propellants and pressurisation gases play a crucial role in spacecraft propulsion systems, enabling precise thrust control, efficient fuel management, and reliable operations in space. Selecting the appropriate propellant or gas depends on mission-specific requirements, including cost, performance, availability, and handling characteristics. Electric propulsion typically relies on gases like xenon, krypton, and innovative alternatives like bismuth, each offering distinct advantages in thrust efficiency, cost-effectiveness, or ease of use.
The high cost and limited availability of xenon have resulted in exploratory policy initiatives aimed at fostering krypton and bismuth alternatives, as well as enabling more efficient propellant recycling technologies. These efforts are often supported by public-private partnerships and government R&D programmes.
Meanwhile, helium serves as a versatile support gas, critical not only for maintaining pressure and ensuring smooth propellant flow but also for thermal regulation and meticulous system integrity checks. Understanding these materials and their unique properties is essential for the advancement and optimisation of space propulsion technology.
-
Xenon - Xenon is the gold standard for electric propulsion, dominating as the preferred propellant in Hall-effect thrusters (HETs) due to its high atomic mass (131.3 u) and favourable ionisation characteristics. Within HET systems, xenon atoms undergo ionisation through electron collisions within a magnetic field, generating ions accelerated to velocities ranging from 15 to 30 km/s, corresponding to specific impulses (Isp) between 1,600 and 2,500 seconds. This efficiency underpins critical space missions, such as the European Space Agency’s SMART-1 lunar probe, which utilised xenon-powered HETs to achieve a velocity increment of 3.6 km/s over a 14-month operation.
-
Xenon’s large electron-impact ionisation cross-section—approximately 5×10⁻¹⁹ m² at 100 eV enables propellant utilisation rates of 90–99%, significantly reducing waste. Despite its efficiency, xenon remains scarce, with concentrations of just 0.008 ppm in Earth's atmosphere, and costly at around $2,000/kg, prompting the ongoing search for viable alternatives. Nevertheless, xenon continues to dominate critical missions, exemplified by NASA’s Psyche spacecraft, which employs four xenon HETs operating at 4.5 kW each, providing sustained thrust over a six-year journey to a metallic asteroid.
-
Krypton - Krypton emerges as a cost-effective alternative, addressing xenon’s economic constraints while preserving operational performance. With an ionisation energy similar to xenon’s (14.0 eV compared to xenon’s 12.1 eV) but at only one-tenth of xenon’s cost ($200/kg), krypton is suitable for scalable electric propulsion systems. The Polish-developed IPPLM thruster illustrates krypton’s viability, delivering 83 mN of thrust at just 0.5 kW—performance comparable to xenon-based systems operating at similar power levels.
-
Advances in magnetic field optimisation, specifically employing radial fields ranging from 100 to 300 Gauss, effectively mitigate krypton’s lower atomic mass of 83.8 u, enhancing ion confinement and improving overall thrust efficiency. High-power testing by NASA’s 457M HET achieved 2.5 N of thrust and specific impulse values of 4,500 seconds at power levels up to 72.5 kW, demonstrating krypton’s practicality for demanding missions that require substantial velocity changes, such as crewed missions to Mars.
-
Bismuth – Bismuth represents a high-performance, condensable propellant that introduces unique advantages due to its distinctive phase-change characteristics. Possessing the highest atomic mass (208.98 u) among stable elements and an ionisation energy of just 7.29 eV—approximately 40% lower than xenon—bismuth facilitates exceptional performance, achieving specific impulses above 8,000 seconds at voltages up to 10 kV.
-
Thrusters such as Busek’s BHT-1500-V2 demonstrate bismuth’s superiority, attaining thrust-to-power ratios that are 22% higher than comparable xenon thrusters at 300 V discharge voltages, attributed to enhanced ionisation that yields propellant utilisation efficiencies as high as 95%. Additionally, bismuth’s condensability uniquely simplifies ground-testing logistics by solidifying vapour on vacuum-chamber walls at ambient temperatures, effectively creating a self-pumping system that significantly reduces testing costs by removing the need for complex cryogenic equipment.
-
Economically, bismuth offers substantial savings for missions requiring large propellant masses; for example, a 10,000 kg propellant load of bismuth costs around $75,000, compared with approximately $20 million for an equivalent quantity of xenon, a critical advantage for budget-sensitive lunar supply chain missions. Technical challenges, however, include developing reliable vaporisation methods. Innovations such as Michigan Tech’s direct-evaporation system, which utilises porous metallic discs heated to approximately 600°C, efficiently regulate propellant flow via waste heat generated by thruster operation, reducing auxiliary power requirements and maintaining overall efficiencies above 60%.
-
Helium – Helium is a versatile inert gas used widely in space systems, particularly for propulsion support and thermal management. In chemical propulsion, helium pressurises fuel tanks to maintain steady fuel and oxidiser flow, especially in microgravity conditions. Because helium is chemically inert, it prevents unwanted reactions, making it essential for safely handling reactive propellants like hydrazine or nitrogen tetroxide. Even leftover helium—typically about 5% of the initial load—can be useful, providing modest thrust (0.5 to 2 mN) in electric propulsion systems once ionised. This helps extend satellite mission durations.
-
Helium also excels in thermal control applications. For example, Absolut System developed a helium cooling loop for STFC’s laser amplifier, maintaining temperatures as low as 140 K (-133°C) with helium flowing at 200 grams per second. This system uses hydrodynamic gas-bearing circulators, eliminating lubricants and thus avoiding contamination—essential for sensitive optical equipment such as the James Webb Telescope’s Mid-Infrared Instrument (MIRI). Additionally, helium’s very small atomic size (140 pm) makes it ideal for precise leak detection during spacecraft assembly, enabling checks at sensitivities down to 1×10⁻¹² mbar·L/s. This ensures airtight seals vital for high-performance ion thrusters and sensitive fuel cells.
Electronics and semi-conductor materials
Policies such as the U.S. CHIPS Act, Europe’s Horizon Europe programme, and Japan’s Moon-to-Mars roadmap include provisions to secure next-generation semiconductor technologies. These include systems based on gallium nitride (GaN) and gallium arsenide (GaAs), which are increasingly critical in space electronics.
The harsh environment of space, characterised by extreme temperatures, ionising radiation, and vacuum conditions, demands materials with specialised electronic and optical properties. Elements such as germanium, gallium-based compounds, phosphorus, antimony, lithium, and arsenic derivatives underpin spacecraft electronics, solar panels, sensors, and communication systems. Their unique characteristics ensure reliable performance across missions lasting decades, from Earth-orbiting satellites to deep-space probes.
Looking ahead, policy frameworks are beginning to support in-situ resource utilisation (ISRU) as a means of reducing dependency on Earth-based supply chains. Lunar regolith, for example, contains trace amounts of germanium, phosphorus, and lithium—elements that could support 3D-printed optical systems and batteries for Moon-based infrastructure.
-
Germanium – plays a critical role in space systems due to its dual use in high-efficiency photovoltaics and infrared optics. In multi-junction solar cells, germanium wafers serve as substrates for III-V semiconductor stacks (such as InGaP/InGaAs/Ge), achieving efficiencies exceeding 30% under the air mass zero (AM0) solar spectrum typical in space. Its lattice constant closely aligns with that of gallium arsenide, reducing defects during epitaxial growth and enhancing photon absorption in the near-infrared range.
-
For infrared applications, germanium windows transmit around 90% of light within the 2–14 µm spectrum, making them essential in thermal imaging systems and star trackers. Their low chromatic aberration and high Knoop hardness (780) provide resilience against micrometeoroid impacts. However, germanium is prone to thermal runaway, with transmission performance declining significantly above 100°C, limiting its use in hotter environments. The European Space Agency’s Solar Orbiter employs germanium-based detectors to analyse emissions from the solar corona, capitalising on the material’s infrared transparency to capture data at temperatures nearing one million degrees Celsius.
-
Gallium – particularly in compound forms, is vital for radiation-hardened semiconductors. Gallium arsenide (GaAs) is widely used in space-grade solar cells and radiofrequency (RF) systems owing to its direct bandgap (1.42 eV) and high electron mobility (8,500 cm²/V·s). Triple-junction GaAs/InGaP/Ge cells, which have powered Mars rovers and deep-space missions, maintain approximately 34% efficiency even after enduring over 15 years of proton radiation in geostationary orbit. GaAs-based RF amplifiers function at Ka-band frequencies (26.5–40 GHz) with noise figures under 2 dB, supporting high-data-rate communications in missions such as NASA’s Psyche probe.
-
Gallium nitride (GaN), with its wide bandgap (3.4 eV) and high breakdown voltage (3.3 MV/cm), is well-suited to satellite power electronics and ion propulsion systems. GaN transistors achieve up to 98% efficiency in DC-DC converters, helping reduce heat in sealed spacecraft modules. Unlike silicon, GaN components are intrinsically resistant to displacement damage from gamma rays and heavy ions, surviving doses exceeding 1 Mrad(Si) without shielding. Radiation-hardened GaN modules from EPC Space are now used to power CubeSat reaction wheels, reducing mass by 40% compared to traditional silicon-based alternatives.
-
Phosphorus – is a key n-type dopant in silicon solar cells, improving conductivity by introducing free electrons into the crystal lattice. When present at concentrations between 10¹⁶ and 10¹⁸ cm⁻³, phosphorus-doped silicon achieves resistivities below 0.1 Ω·cm, enhancing charge collection in systems such as the International Space Station’s solar panels, which operate at around 16% efficiency.
Recent innovations in two-dimensional black phosphorus layers, with adjustable bandgaps ranging from 0.3 to 2.0 eV, have enabled the development of flexible photodetectors capable of sensing across the ultraviolet to infrared spectrum—ideal for deployment on lunar rovers. In optical coatings, phosphorus-doped silica reduces reflectivity to below 0.5% at 500 nm, which is crucial for the charge-coupled devices (CCDs) used in Earth observation satellites. The James Webb Space Telescope’s Near-Infrared Spectrograph (NIRSpec) employs such coatings to maximise light capture from distant celestial bodies.
-
Antimony – is used to stabilise infrared-transparent glasses and support radiation-hardened electronics. Antimony oxide (Sb₂O₃) is added to infrared glasses to ensure dimensional stability under thermal cycling conditions ranging from -180°C to +150°C, which is vital for space-based optical systems.
-
The Mid-Infrared Instrument (MIRI) aboard the James Webb Space Telescope uses antimony-borate glasses to maintain optical focus while observing wavelengths between 5–28 µm. Antimony also exhibits anisotropic conductivity, enabling the development of advanced transistors. Two-dimensional antimony films demonstrate electron mobility up to 1,200 cm²/V·s, outperforming silicon under intense radiation exposure, such as that found within Jupiter’s magnetosphere.
-
Lithium – is indispensable for spacecraft power storage and advanced electro-optic systems. Lithium-ion batteries dominate energy storage solutions in space applications due to their high energy density of approximately 250 Wh/kg, roughly 70% lighter than nickel-hydrogen alternatives. Systems such as Mastervolt’s MLI Ultra 12/1250 sustain over 2,000 charge-discharge cycles at 80% depth, supporting critical functions like life support in NASA’s Lunar Gateway.
-
In electro-optics, lithium niobate (LiNbO₃) modulators support high-speed data transmission, enabling laser communications at 100 Gbps in projects such as the Laser Communications Relay Demonstration (LCRD). Additionally, lithium tantalate (LiTaO₃) crystals exhibit the Pockels effect, a property where the crystal’s refractive index changes when an electric field is applied, allowing light signals to be switched or modulated at extremely high speeds. This effect enables terahertz-rate optical switching, which is essential for the rapid, reliable transmission of data in deep-space communication systems.
-
Arsenic – plays an enabling role in the fabrication of high-efficiency GaAs solar cells. When incorporated into gallium arsenide, arsenic forms a zincblende crystal structure that supports electron velocities approximately 2.5 times greater than those in silicon. Advances in hydride vapour phase epitaxy (HVPE) now allow GaAs crystals to grow at rates of 300 µm per hour, significantly reducing production costs while maintaining efficiencies of around 25%. These robust cells are scheduled to power caching robots in NASA’s Mars Sample Return mission, taking advantage of arsenic’s inherent radiation resistance, exhibiting less than 5% degradation over 15 years.
Permanent magnets and rare-earth elements
Rare earths such as samarium, neodymium, and dysprosium play a critical role in permanent magnets, which are essential across advanced technologies, including defence and aerospace. Their strategic value has prompted national stockpiling and targeted investments, such as U.S. defence initiatives aimed at boosting domestic magnet manufacturing and reducing reliance on Chinese imports.
These rare-earth elements are indispensable in space applications, where materials must withstand vacuum, radiation, and extreme thermal fluctuations and require long-term precision performance. Their exceptional magnetic and optical properties make them vital to modern spacecraft systems.
-
Samarium-cobalt magnets, particularly the SmCo₅ and Sm₂Co₁₇ alloys, are indispensable for components exposed to high or fluctuating temperatures. These magnets can operate reliably in environments ranging from near absolute zero (-273°C) up to 350°C, making them particularly well-suited to applications in rocket engines and deep-space probes where neodymium alternatives may fail.In spacecraft, SmCo magnets are essential for reaction wheels, stabilising flywheels in attitude control systems by providing precise angular momentum adjustments.
-
Their resistance to demagnetisation ensures consistent performance, whether in the intense heat of solar exposure or the deep cold of shadowed space. Notably, NASA’s Deep Space 1 mission employed SmCo magnets in its ion thruster system, which delivered 4.5 kW of thrust with a specific impulse ranging from 1,600 to 2,500 seconds. Additionally, gyroscopic sensors benefit from SmCo’s high coercivity (18–32 kOe), which protects against magnetic degradation in inertial measurement units (IMUs)—crucial for navigation in GPS-denied environments.SmCo magnets also offer a thermal advantage due to their low-temperature coefficient of -0.03%/°C (compared to -0.12%/°C for NdFeB), minimising performance drift caused by orbital thermal cycling. Moreover, they retain 98% of their magnetic flux after exposure to 10¹⁶ protons per square centimetre, making them particularly robust in radiation-heavy zones like the Van Allen belts.
-
Neodymium-iron-boron magnets offer the highest energy product of any known permanent magnet—up to 52 MGOe—enabling compact and lightweight components in satellites and planetary rovers. This power density is particularly advantageous for systems where mass and volume are at a premium. In satellite momentum wheels, NdFeB magnets allow CubeSat rotors to reach speeds of up to 10,000 RPM, achieving a 40% mass reduction compared to equivalent SmCo systems.
-
Nd magnets are also employed in deployable mechanisms, such as solar array hinges and antenna deployment systems, as seen in missions like ESA’s Rosetta. In addition, magnetorquers, used to adjust satellite orientation by interacting with Earth’s magnetic field, often rely on NdFeB magnets doped with dysprosium to enhance performance and reduce propellant usage.
-
However, one challenge with NdFeB magnets is their sensitivity to temperature. Pure neodymium magnets lose around 80% of their coercivity above 150°C. To overcome this, dysprosium is often added to improve thermal stability, particularly for applications like Mars rovers, which must endure surface temperatures ranging from -125°C to +20°C.
-
Dysprosium plays a vital role in enhancing the high-temperature stability of NdFeB magnets. By diffusing along grain boundaries, dysprosium prevents thermal demagnetisation, raising the maximum operating temperature of NdFeB from around 80°C to over 200°C with as little as 3–6% Dy addition.In space systems, Dy-doped NdFeB magnets are used in high-temperature motors, such as those in Venus landers, which must function in temperatures exceeding 450°C.
-
Dysprosium also contributes to cryogenic applications; its magnetocaloric properties help stabilise superconducting magnets in emerging space-based quantum sensors.Despite its importance, dysprosium is extremely scarce—found at just 0.005 parts per million in Earth’s crust. This scarcity has driven research into alternative sourcing strategies, including recycling from decommissioned satellites and potential extraction from asteroids.
-
Neodymium-doped yttrium aluminium garnet (Nd:YAG) crystals are a cornerstone of high-power, space-qualified laser systems used in precision optics for communication and scientific instrumentation.In optical communication, Nd:YAG lasers provide the stability and coherence needed for extreme-range data transmission. For instance, ESA’s LISA mission utilises these lasers to detect gravitational waves via interferometry across 2.5 million kilometres, with positional stability down to 10 picometres. Nd:YAG lasers also power spaceborne LIDAR systems, such as the one aboard NASA’s OSIRIS-REx, which used a frequency-doubled 532 nm laser for mapping the surface of asteroid Bennu in high resolution.
-
To ensure durability in space, radiation-hardened Nd:YAG crystals are often co-doped with cerium. This suppresses the formation of colour centres caused by cosmic radiation, allowing the lasers to maintain over 95% of their efficiency after more than a decade in geostationary orbit.
Optical and electro-optical materials
Bismuth, phosphorus, lithium, and germanium form the backbone of modern space optics, enabling spacecraft to operate in conditions where conventional materials would fail. Their unique properties—ranging from infrared transparency to radiation resistance—are essential for remote sensing, imaging, high-speed communications, and laser-based systems. These materials work synergistically to meet the demands of missions venturing to challenging environments such as Mars, Europa, and beyond. Looking ahead, advances in nanostructuring and in-situ resource utilisation could overcome current material constraints, ushering in a new era of self-sufficient, long-duration space exploration.
The space environment presents extreme challenges for optical systems, including severe temperature fluctuations, ionising radiation, and the need for long-term operational stability. Materials like bismuth, phosphorus, lithium, and germanium play a crucial role in addressing these demands through their integration into lenses, IR filters, ceramics, mirror substrates, and glass components. Their optical clarity, infrared performance, and thermal resilience are vital across spacecraft, satellites, and planetary missions. A notable example is ESA’s Solar Orbiter, which combines germanium IR detectors, bismuth-tellurite fibre optics, and lithium niobate (LiNbO₃) modulators to study the dynamics of solar wind.
-
Germanium is indispensable for thermal imaging and infrared sensing due to its wide IR transparency window (2–14 µm). With a high refractive index of 4.0 and minimal chromatic aberration, it ensures sharp, accurate imaging in instruments such as the James Webb Space Telescope’s Mid-Infrared Instrument (MIRI). However, a key limitation is germanium’s “thermal runaway” property—above 100°C, its transmission performance drops dramatically. As a result, it is unsuitable for high-temperature zones like those near rocket nozzles.Germanium finds application in IR windows for Earth observation satellites, supporting the detection of wildfires, volcanic activity, and other surface phenomena. It also serves in spectrometer lenses on Mars rovers, helping analyse the mineral composition of Martian terrain. Recent innovations, such as diamond-like carbon (DLC) and broadband anti-reflective (BBAR) coatings, have reduced reflection losses to less than 1% in the 8–12 µm range, which is critical for low-light systems such as lunar night-vision imaging.
-
Germanium’s tendency towards thermal runaway necessitates active cooling solutions for use in extreme environments such as Venusian landers. Innovations like diamond-like carbon coatings are being explored to reflect excess heat and extend operational lifespans.
-
Bismuth tellurite glasses (Bi₂O₃-TeO₂) offer tunable refractive indices ranging from 1.97 to 2.12 and reduced optical band gaps as bismuth content increases. These optical properties arise from Bi³⁺ ions interacting with non-bridging oxygen atoms, strengthening light-matter interaction and enabling highly responsive systems.Bismuth-based materials are increasingly used in dense optical fibres for deep-space laser communications and in plasmonic sensors aboard CubeSats, where they can detect micrometeoroid impacts. Due to their high polarisability, bismuth compounds allow for compact, integrated optical systems. For example, bismuth-doped metasurfaces can dynamically modulate near-infrared light for LiDAR mapping on lunar landers.
-
On the frontier of materials science, nanostructured bismuth is attracting attention as a lead-free alternative in radiation shielding. Bismuth nanospheres, which exhibit Mie resonances tunable from the far-infrared to the ultraviolet, may replace toxic materials while offering new capabilities in light manipulation and thermal control.
-
Phosphate glasses doped with phosphorus are prized for their structural stability under gamma and proton irradiation, making them ideal for space-based lasers and fibre optics. In fluoride-phosphate glass compositions, such as Ca(PO₃)₂-AlF₃, the oxygen-to-phosphorus (O/P) ratio determines optical dispersion. Lower O/P ratios (below 3.4) stabilise the optical band gap, improving clarity under prolonged radiation exposure.
-
Applications include laser amplifiers in LIDAR systems designed for asteroid composition analysis, and radiation-hardened optical lenses in probes headed for high-radiation environments such as Jupiter’s moon Europa. Phosphate glasses have demonstrated the ability to retain over 95% transmittance even after exposure to 10¹⁸ neutrons/cm², outperforming conventional silicate-based alternatives in the harsh conditions of the Jovian system.
-
Phosphate glasses, while highly radiation resistant, are susceptible to colour centre formation under cosmic ray exposure. Co-doping with cerium or europium has been shown to suppress defect generation, improving long-term stability. In parallel, in-situ manufacturing offers a promising route to sustainability: germanium and phosphorus, present in trace amounts in lunar regolith (0.1 ppm and 1,200 ppm respectively), could potentially support 3D-printed optical systems directly on the Moon.
-
Lithium, particularly in the form of lithium niobate (LiNbO₃), is central to high-speed optical communication systems in space. Known for its strong electro-optic effect (r₃₃ = 30 pm/V) and broad transmission range (400 nm to 5 µm), LiNbO₃ enables terahertz-rate optical switching and dynamic beam steering. These capabilities are vital for laser-based data links between satellites and across planetary distances.One of the key applications is in free-space optical modulators, where lithium niobate devices—enhanced with gold-grating metasurfaces, achieve modulation speeds of up to 190 MHz. This technology supports inter-satellite communication networks and quantum communication systems, including entangled photon sources for secure Earth-Moon links.
-
Recent developments in thin-film LiNbO₃ have reduced device sizes by up to 90%, allowing seamless integration into small spacecraft such as CubeSats, miniaturised satellite made up of modular units, typically measuring 10 cm × 10 cm × 10 cm and weighing about 1.3 kg per unit.
Electrical conductors
Copper is indispensable to spacecraft systems due to its outstanding electrical conductivity, excellent thermal management capabilities, and strong resistance to radiation. Its proven reliability ensures consistent power distribution and effective heat dissipation, even in the most demanding space environments. With unmatched conductivity (59.6 × 10⁶ S/m), ease of manufacture, and superior thermal performance, copper remains central to mission success. As space exploration ventures deeper into extreme environments—such as Venus’s dense atmosphere or Europa’s high-radiation zones—advanced copper alloys and composites will become increasingly essential. Looking ahead, the potential for copper extraction from lunar regolith (which contains around 55 ppm) through electrostatic separation highlights copper’s role in building sustainable off-world infrastructure.
Copper’s high electrical conductivity plays a key role in reducing resistive losses, which is crucial for efficient power transmission across long distances within spacecraft. NASA typically employs oxygen-free high conductivity (OFHC) copper, with a purity level of 99.99%, to minimise oxidation at grain boundaries in vacuum conditions. A prime example is the James Webb Space Telescope, which uses copper interconnects in its Near-Infrared Spectrograph (NIRSpec) to maintain signal integrity across temperature variations of up to 150 K.
Printed circuit boards (PCBs)
In spacecraft electronics, printed circuit boards often rely on rolled-annealed copper foils (RA-Cu) due to their low resistivity (1.7 µΩ·cm). These copper-based PCBs offer several advantages, including:
-
High-speed data transmission, supporting signals up to 25 Gbps, such as those used in Xilinx FPGAs aboard Mars rovers.
-
Superior radiation tolerance, with annealed copper retaining 95% conductivity even after exposure to intense proton radiation (10¹⁵ protons/cm²), outperforming alternatives like aluminium in high-radiation regions such as Jupiter’s magnetosphere.
Radiation-hardened PCB designs, such as those developed by Cadence, feature optimised copper layering (2 oz/ft²), striking a balance between high current-carrying capacity (45 A/mm²) and strict spacecraft weight constraints.
Thermal management and cooling systems for spacecraft
Copper is also integral to spacecraft thermal regulation and cooling. In NASA’s Advanced Passive Thermal eXperiment (APTx) aboard the International Space Station, copper-water heat pipes proved highly effective, transferring 65 W of heat at 70°C with an exceptionally low thermal gradient (0.02°C/cm). These systems offer reliable performance in microgravity, thanks to grooved copper wicks that maintain steady capillary action. They are also robust under extreme temperature cycles, operating between -40°C and +120°C—ideal for surviving lunar nights. Such copper-water heat pipes are currently used to cool sensitive electronics in Lockheed Martin’s Next-Generation OPIR missile-warning satellites, maintaining detector temperatures around 193 K (-80°C).
Rocket engine cooling
Copper’s exceptional thermal conductivity has long made it vital to rocket engine cooling systems. The Space Shuttle Main Engines used NARloy-Z (a Cu-3Ag-0.5Zr alloy), which delivered thermal conductivity of 330 W/m·K at 600°C—three times that of stainless steel. This alloy also offered resistance to hydrogen embrittlement, supporting over 100 successful launches without structural fatigue. Building on this, modern materials like GRCop-42 (Cu-4Cr-2Nb) maintain 98% of the conductivity of pure copper while providing greatly enhanced mechanical strength, with a yield strength of 450 MPa.
Innovative materials for extreme space environments
To meet the increasingly demanding conditions of deep space, copper-based materials are being further refined for resilience and performance. For example:
-
In radiation hardening, beryllium-copper alloys (such as C17200) offer a combination of high hardness (22 HRC) and good conductivity (18%), making them ideal for precision components such as slip rings on Mars rovers. Meanwhile, diamond-copper composites—capable of thermal conductivity up to 550 W/m·K—are being explored through programmes like DARPA’s CHIPS initiative. These materials support improved heat dissipation and reduced radar signatures.
-
Although copper is ideal for internal spacecraft systems, it is vulnerable to erosion by atomic oxygen in Low Earth Orbit (LEO), degrading at a rate of approximately 0.5 µm per year. To mitigate this, protective measures are employed—such as silver-plated copper connectors on the ISS’s solar arrays (operating at 120 V and 160 A), and indium tin oxide (ITO) coatings, typically 80 nm thick, which shield copper surfaces from atomic oxygen degradation.
Looking ahead, ESA’s PROBA-3 mission will trial laser-sintered copper interconnects in 2026, potentially paving the way for on-orbit manufacturing and in-space PCB repair. This innovation could significantly enhance the maintainability and longevity of future spacecraft systems.
PGMs in space applications
Platinum group metals (PGMs) possess a unique combination of properties—outstanding electrical conductivity, catalytic activity, and the ability to adsorb hydrogen and oxygen—which make them invaluable in space technologies. Their use enhances the energy and materials efficiency of key systems, particularly under the extreme conditions encountered in space. In propulsion systems, PGMs offer high thermal stability and catalytic resilience, enabling long-term performance. For ion propulsion systems, which outperform traditional chemical propulsion in efficiency and longevity, PGMs play a central role in ionisation and thrust generation.
-
Platinum is essential to modern aerospace propulsion systems due to its exceptional catalytic stability and high melting point. In rocket engines, it facilitates the efficient combustion of propellants by lowering activation energy thresholds. This not only boosts thrust-to-weight ratios but also reduces fuel consumption—particularly valuable for reusable launch vehicles that must deliver consistent performance across multiple missions. Platinum also underpins hydrogen fuel cell technologies used in lunar and Martian exploration. Programmes such as NASA’s Artemis and JAXA’s collaboration with Toyota deploy platinum-catalysed fuel cells to power rovers, offering high energy density and zero emissions.
-
Platinum's resistance to corrosive byproducts from hydrogen-oxygen reactions ensures durability in environments where repair is impractical. Recent innovations include platinum-rhodium alloys used to line nozzles in hybrid engines, offering erosion resistance and structural integrity at temperatures exceeding 1,500°C—crucial for sustained orbital burns.
-
Palladium’s versatility is reflected in its applications in energy generation and storage. In photovoltaics, palladium diselenide (PdSe₂) demonstrates superior light absorption, especially in ultraviolet and near-infrared ranges. This enables lightweight, radiation-hardened thin-film solar panels suitable for high-radiation orbits.
-
In hydrogen fuel systems, palladium improves performance by accelerating hydrogen dissociation at lower temperatures, which is vital for deep-space missions reliant on hydrogen harvested from lunar ice. Palladium-based membranes also purify hydrogen by removing contaminants, critical in closed-loop life support systems. Furthermore, its potential role in nuclear thermal propulsion (NTP) is being explored; palladium’s neutron moderation properties could enhance reactor safety and efficiency, enabling compact, reliable propulsion systems for future crewed missions to Mars.
-
Rhodium is prized for its hardness, corrosion resistance, and durability under extreme conditions, making it suitable for high-wear spacecraft components. Rhodium-plated electrical connectors on satellites maintain conductivity despite prolonged exposure to atomic oxygen and micrometeoroid impacts. This plating prevents fretting corrosion in docking systems and antenna arrays, ensuring reliable communication over mission lifetimes. In propulsion, rhodium-coated turbine blades used in gas turbine engines tolerate temperatures above 1,200°C while resisting oxidation. The metal also contributes to thermal management; rhodium-coated radiators are used in lunar habitats to dissipate excess heat during extended daylight periods.
-
Additionally, rhodium-based alloys are used in microgravity research aboard the International Space Station (ISS). The Rhodium Crystal Preservation project, for example, developed crystalline matrices to preserve biological samples without refrigeration—addressing cold-chain challenges during long-duration missions.
-
Ruthenium - Ruthenium is primarily used in electroplating and alloy engineering to improve wear resistance in moving spacecraft components. Ruthenium-nickel superalloys are applied in thrust vector control systems, where repeated actuation wears down traditional materials. These alloys reduce the maintenance needs of ion thrusters, especially in geostationary satellites requiring precise station-keeping for 15 years or more.
-
The RHODUNA® alloy, comprising 75% rhodium and 25% ruthenium, highlights the balance of cost and performance. It delivers 22% cost savings over pure rhodium while enhancing abrasion resistance by 40%, making it ideal for optical mirror coatings and laser communication arrays. Ruthenium’s catalytic qualities are also under investigation for in-situ resource utilisation (ISRU). Ruthenium-based catalysts could help convert Martian CO₂ into methane for use as rocket fuel, enabling return journeys from the Martian surface.
-
Iridium - Although direct references to iridium’s modern space applications are limited, its legacy speaks to its reliability. The Iridium satellite network—named for the element’s atomic number—utilised iridium alloys in radiation-hardened transponders. Iridium’s high melting point (2,466°C) and corrosion resistance make it ideal for components such as combustion chamber linings in bipropellant engines. These properties are particularly useful in high-thrust engines operating over extended durations and in corrosive fuel environments.
-
Osmium - Osmium’s extremely high density (22.59 g/cm³) and resistance to radiation make it suitable for shielding sensitive electronics in space. For example, the REACH (Responsive Environmental Assessment Commercially Hosted) system aboard Iridium NEXT satellites uses osmium-doped sensors to monitor space weather events such as solar particle storms. This data supports astronaut safety and protects critical equipment during extravehicular activities and orbital transfers.
-
Osmium also plays a role in satellite cybersecurity, where osmium-based secure boot modules help prevent firmware tampering. Its low neutron cross-section reduces interference with onboard nuclear batteries, ensuring uninterrupted function in deep-space missions. Experimental osmium-reinforced attitude control wheels have shown a 30% mass reduction compared to tungsten-based systems—an advantage for small satellite constellations. Despite concerns over toxicity, osmium’s exceptional gamma radiation stability has prompted interest in its use for radioisotope thermoelectric generator (RTG) casings. Encapsulating plutonium-238 in osmium alloys could potentially extend RTG lifespans beyond 50 years, supporting missions to the outer solar system and beyond.
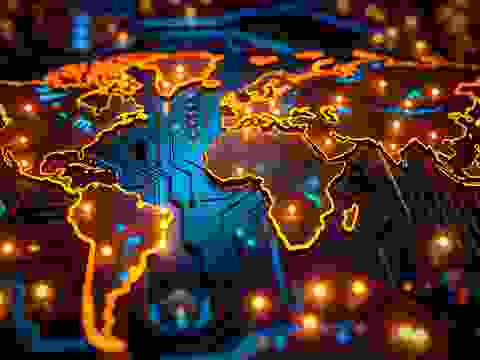
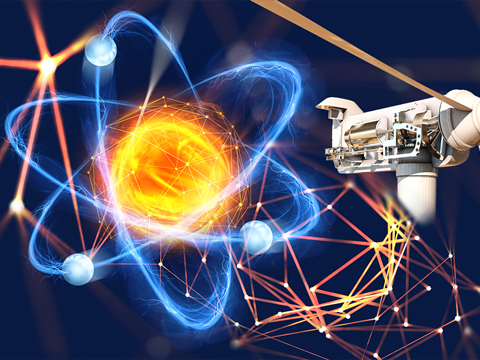
Critical sectors using strategic minerals
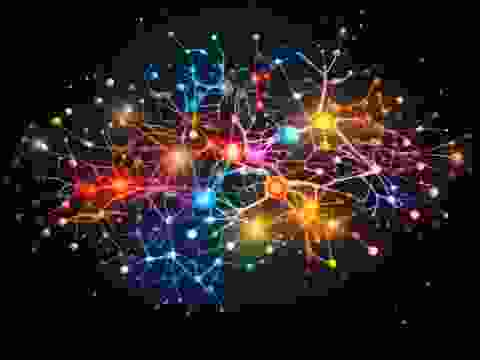
Meet the Critical Minerals team
Trusted advice from a dedicated team of experts.
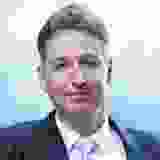
Henk de Hoop
Chief Executive Officer
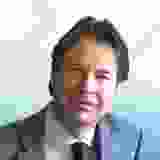
Beresford Clarke
Managing Director: Technical & Research
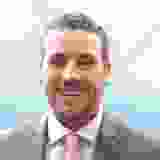
Jamie Underwood
Principal Consultant
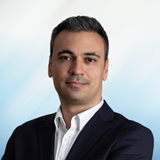
Ismet Soyocak
ESG & Critical Minerals Lead
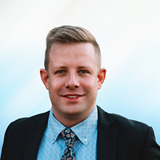
Rj Coetzee
Senior Market Analyst: Battery Materials and Technologies
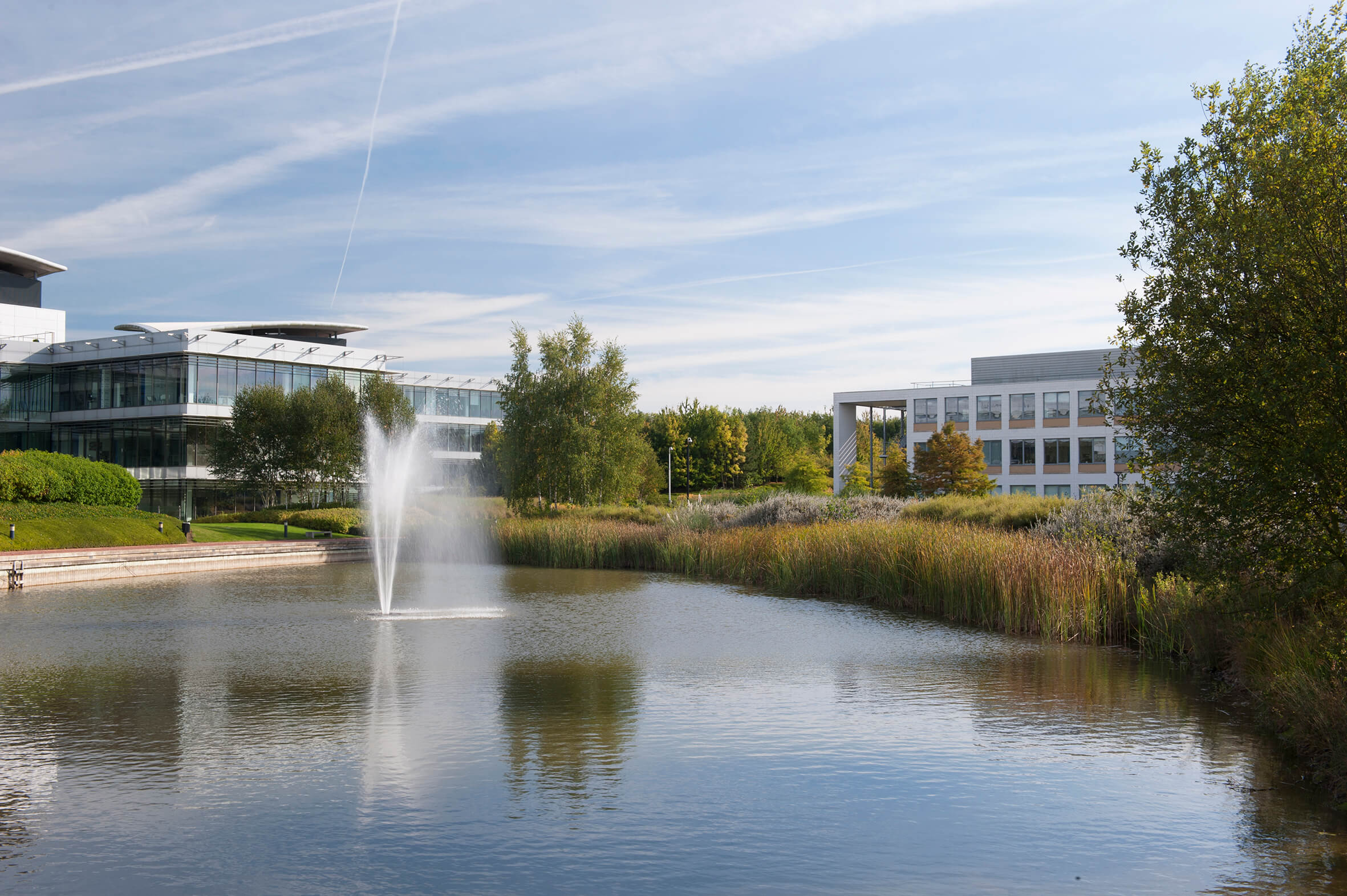
How can we help you?
SFA (Oxford) provides bespoke, independent intelligence on the strategic metal markets, specifically tailored to your needs. To find out more about what we can offer you, please contact us.