Zinc
Critical Minerals and The Energy Transition
Navigating the Zinc Market
Zinc is a strategically important mineral that plays a foundational role in global industry and infrastructure. Its value lies not only in its broad industrial applications—from galvanisation and die-casting to energy storage, pharmaceuticals, and agriculture—but also in its growing contribution to global sustainability and decarbonisation goals. As the world accelerates the shift towards cleaner energy systems and climate-resilient infrastructure, zinc is evolving from a traditional base metal into a critical enabler of modern technologies, including renewable energy integration, electric mobility, and long-duration energy storage. Zinc’s market dynamics are shaped by a combination of complex supply chains, geographically concentrated production, and a shifting demand profile. While galvanised steel continues to dominate consumption, especially in construction, automotive manufacturing, and infrastructure—emerging uses in battery chemistries, corrosion-resistant alloys, and circular economy initiatives are expected to diversify future demand. Meanwhile, supply security concerns, environmental permitting, and the limited substitutability of zinc in key applications are influencing national and international strategies aimed at securing access to this indispensable mineral.
An introduction to zinc
Zinc demand and end-uses
Zinc is a vital industrial resource with a wide range of applications across multiple sectors. It is the fourth most-produced metal globally, following iron, aluminium, and copper. Global demand for zinc is expected to grow steadily throughout the decade, driven by infrastructure development and industrial expansion, particularly in emerging economies.
Galvanisation remains the most significant end-use for zinc, accounting for approximately half of total global consumption. This process involves coating iron or steel with zinc to prevent corrosion, achieved through two protective mechanisms: barrier protection and sacrificial protection. Upon exposure to air, zinc forms a layer of zinc oxide, which subsequently converts into zinc carbonate—a stable, durable layer that shields the underlying metal from corrosive elements.
As galvanisation continues to dominate zinc usage, emerging applications in energy storage systems and specialised chemical processes are poised to diversify the demand landscape. Zinc’s unique properties and its crucial role in prolonging the lifespan of steel infrastructure ensure its enduring relevance in the global industry.
Hot-dip galvanising is the most widely used method, involving the immersion of iron or steel into molten zinc at around 450°C. This process forms a strong metallurgical bond, producing multiple layers of zinc-iron alloys. The resulting galvanised components require no further surface preparation and are immediately ready for deployment.
Galvanised steel is extensively used in construction, automotive manufacturing, shipbuilding, and infrastructure development. In typical environments, a properly galvanised industrial steel component can last over 50 years, or around 20 years in high-moisture conditions.
While pure zinc possesses relatively low strength and hardness, its mechanical properties are significantly improved when alloyed with elements such as aluminium and copper. These zinc alloys exhibit excellent die-casting characteristics, including high fluidity, dimensional stability, and mechanical strength.
As a result, they are widely used in automotive components, mechanical parts, and precision die-casting applications, particularly where superplasticity is required. Zinc-copper-titanium alloys stand out for their mechanical performance, offering properties comparable to aluminium alloys, brass, and grey cast iron, alongside significantly enhanced creep resistance.
Zinc’s versatility also extends to printing and related industries. It is used in the manufacture of printing zinc plates, powder corrosion photographic plates, and offset printing plates. These applications benefit from zinc’s favourable characteristics, while also reducing reliance on more hazardous elements such as lead and cadmium.
Zinc batteries represent an emerging significant end-use with promising growth potential. These energy storage solutions offer several advantages over conventional alternatives:
-
Zinc batteries provide long cycle life, high specific energy and power density, along with maintenance-free operation. They support wide operating temperature ranges (-30°C to 75°C) and require minimal maintenance to preserve performance and safety. Nickel-zinc batteries achieve the highest power density among mainstream rechargeable battery chemistries.
-
Compared to lithium-ion alternatives, zinc batteries offer enhanced sustainability through water-based electrolytes instead of organic solvents. They utilize non-fluorinated salts with fewer additives and have lower environmental impact. Additionally, zinc batteries don't pose fire risks during catastrophic failures, making them inherently safer than lithium or sodium batteries.
-
A particularly promising application is in long-duration energy storage, where zinc batteries can economically store energy for periods ranging from 3-72 hours. This capability enables better utilization of renewable energy sources by providing power during extended periods without sun or wind.
Zinc compounds exhibit remarkable versatility across numerous industries due to their diverse chemical and physical properties:
-
Zinc oxide (ZnO) is utilized in rubber manufacturing, paints, pharmaceuticals, and electronics. Zinc sulfide (ZnS) finds applications in optics, pigments, and electronics, while zinc chloride (ZnCl₂) is employed in textiles, metallurgy, and chemical synthesis. Zinc sulfate (ZnSO₄) serves the agriculture, nutrition, and medicine sectors.
-
Zinc dust plays specialized roles across multiple industries. In the paint and coatings sector, it functions as a binding agent and protective coating on metal surfaces, providing anti-corrosive properties. The electronics industry uses zinc dust in thermal paste production to address overheating in components like processors and chipsets. Additionally, the rubber and plastics industry employs zinc dust as a strengthening agent to enhance mechanical properties.
Zinc also has a purpose in specialised industrial applications. In conustruction and building materials, Zinc sheet is widely used for building applications, particularly in roofing, flashing, and architectural elements. Its corrosion resistance and self-healing properties make it ideal for these exposed applications. In metallurgical industries, zinc is used for metal recovery processes. Zinc dust specifically assists in separating valuable metals during processing operations. In pharmaceutical and healthcare industries, zinc compounds appear in pharmaceutical formulations, particularly topical treatments that leverage zinc's antimicrobial properties, and is also recognized as an essential nutrient in human health.
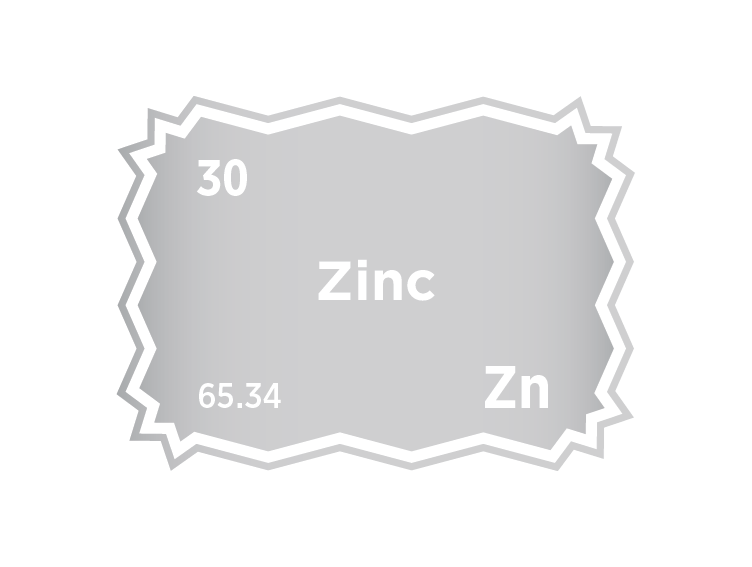
Zinc supply
Zinc is primarily produced through the mining of zinc-bearing ores, with sphalerite (zinc sulphide, ZnS) being the most economically significant. Sphalerite is often found in association with other base metals such as lead, silver, and copper, meaning that zinc is frequently mined as part of polymetallic deposits. Less common zinc minerals include smithsonite (zinc carbonate), hemimorphite (zinc silicate), and willemite (zinc silicate), though these are typically of secondary importance in global production.
Zinc supply is geographically diverse but heavily concentrated among a few major producers. China is the world’s leading zinc mine producer, followed by Peru, Australia, Mexico, and the United States. Other significant producers include Bolivia, India, Kazakhstan, Canada, and Russia, each contributing meaningfully to the global zinc market. Many countries with smaller-scale operations also play critical roles in regional supply chains.
Refined zinc, or zinc slabs, are produced through smelting and refining processes that convert zinc concentrate into usable metal. China, India, South Korea, Canada, and Mexico are among the largest slab producers, supporting downstream industries across construction, automotive, and battery manufacturing.
Supply security remains a key concern, particularly due to the concentration of smelting capacity in Asia and the environmental and permitting challenges facing new mine development in other regions.
Zinc mine producers
Zinc substitution
Zinc is challenging to substitute in many of its core applications due to its unique combination of properties, including corrosion resistance, low melting point, electrical conductivity, and excellent die-casting performance. In galvanisation, where zinc protects steel from rust through both barrier and sacrificial mechanisms, viable alternatives such as aluminium, magnesium, or advanced organic coatings often fall short in terms of long-term durability, cost-effectiveness, and ease of application. Galvanised steel remains the material of choice in construction and infrastructure due to zinc’s proven performance in harsh environments.
In die-casting and alloy production, magnesium, aluminium, and certain engineered plastics may replace zinc in specific cases; however, they typically lack the same balance of strength, fluidity, and dimensional stability, particularly in complex or high-precision components. Substitution may also require major retooling and requalification, further raising costs.
In energy storage, zinc-based batteries offer a safer and more sustainable alternative to lithium-ion chemistries. For long-duration and grid-scale applications, zinc's low flammability, abundant supply, and recyclability give it a competitive edge, with limited direct substitutes offering the same risk profile and environmental benefits.
Overall, zinc’s physical and chemical characteristics, coupled with its industrial integration, make substitution both technically and economically constrained across most sectors.
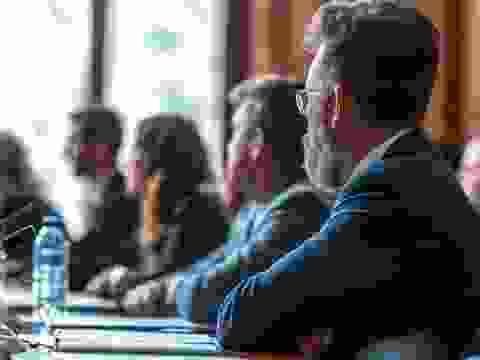
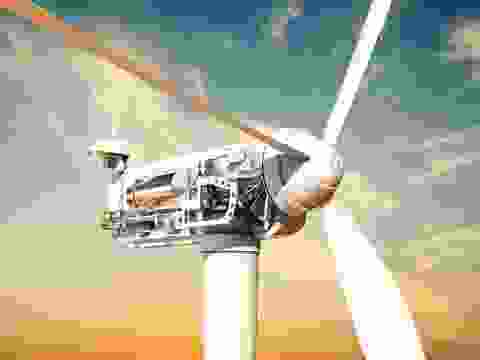
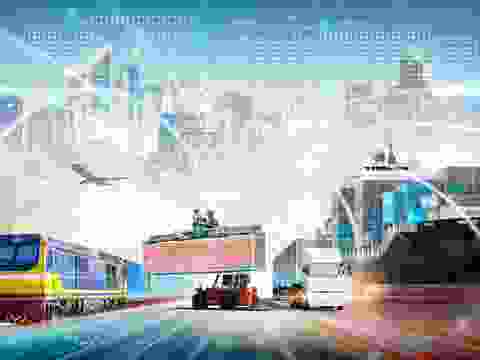
Meet the Critical Minerals team
Trusted advice from a dedicated team of experts.
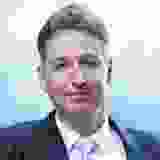
Henk de Hoop
Chief Executive Officer
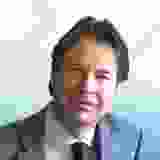
Beresford Clarke
Managing Director: Technical & Research
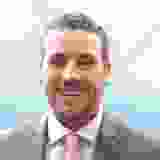
Jamie Underwood
Principal Consultant
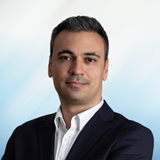
Ismet Soyocak
ESG & Critical Minerals Lead
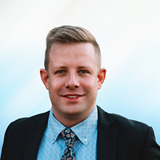
Rj Coetzee
Senior Market Analyst: Battery Materials and Technologies
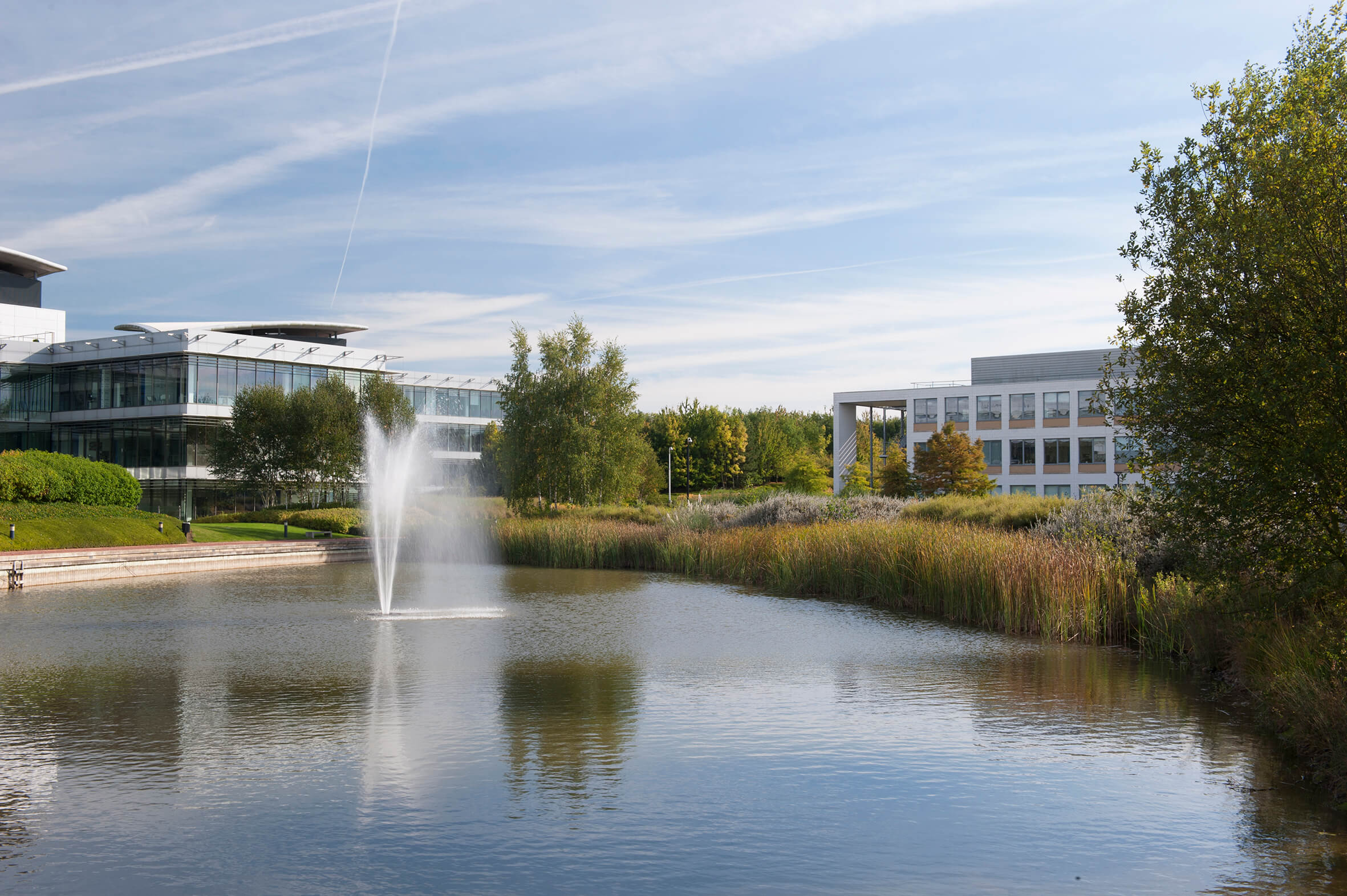
How can we help you?
SFA (Oxford) provides bespoke, independent intelligence on the strategic metal markets, specifically tailored to your needs. To find out more about what we can offer you, please contact us.