Manganese
Critical Minerals and The Energy Transition
Navigating the Manganese Market
Manganese is a vital industrial metal bridging the worlds of traditional manufacturing and emerging clean technologies. Long essential to steelmaking, it is now gaining strategic importance in the global energy transition—particularly as a critical component in next-generation battery chemistries. As governments accelerate decarbonisation and electric vehicle adoption grows, demand for high-purity manganese compounds is rising sharply. This surge in demand is putting new pressure on an already fragile supply chain, characterised by geographic concentration, infrastructure constraints, and a heavy reliance on Chinese processing capacity. China currently controls over 85% of global refining, especially for High-Purity Manganese Sulphate Monohydrate (HPMSM), which is vital for EV battery cathodes. Ore production is also highly concentrated, with South Africa, Gabon, China, Australia, and India dominating output. Manganese’s unique electrochemical and metallurgical properties make it difficult to substitute. Recent supply disruptions, including the 2024 closure of Australia’s Groote Eylandt mine, labour strikes in South Africa, and port delays in Gabon have exposed the fragility of global supply chains highlights the urgency of diversification by Western Governments. The US and EU are ramping up domestic production, refining, and recycling, supported by frameworks like the Inflation Reduction Act and the Critical Raw Materials Act. Meanwhile, efforts to secure alternative sources through trade agreements with African producers and strategic engagement in Latin America and Southeast Asia.
An introduction to manganese
Manganese demand and end-uses
The global manganese market is undergoing a significant transformation, driven by shifting industrial demands and technological innovation. While steel production has historically dominated manganese consumption, the rapid growth of electric vehicle (EV) battery technologies is reshaping end-use patterns and future demand trajectories.
Steel manufacturing remains the primary consumer of manganese, accounting for approximately 90% of global demand. As a critical alloying agent, manganese enhances steel’s strength, hardness, and resistance to wear. This is particularly vital in the construction sector, where fast-growing economies such as China and India continue to drive steel demand. Together, these two countries account for around 65% of global manganese consumption, spurred by infrastructure development and the electrification of transport. China’s New Energy Vehicle Industrial Development Plan targets 40% EV penetration by 2030, necessitating 500 ktpa of High-Purity Manganese Sulphate Monohydrate (HPMSM). Meanwhile, India’s National Steel Policy aims to double domestic steel output to 300 million tonnes by 2030.
Advancements in high-strength, lightweight steel for automotive applications are also reinforcing manganese’s indispensability. Innovative alloys, such as advanced high-manganese steels (e.g., Twinning-Induced Plasticity steels), are gaining traction in vehicle manufacturing for their superior crash resistance and contribution to fuel efficiency.
Beyond metallurgy, the energy transition has positioned manganese as a strategically critical material in lithium-ion battery production. Although less than 1% of current global manganese output supports battery manufacturing, this segment is poised for exponential growth. HPMSM is essential for cathode chemistries such as nickel-cobalt-manganese (NCM) and lithium-manganese-iron-phosphate (LMFP). The latter is gaining industry attention due to its cost-effectiveness, thermal stability, and reduced reliance on cobalt and nickel.
Automakers like Tesla and Volkswagen are actively integrating manganese-rich cathode technologies to reduce costs and align with sustainability objectives. By 2025, it is estimated that 30% of new EV models will incorporate LMFP chemistries, requiring approximately 50–60 kg of manganese per vehicle. This shift is spurring investment in HPMSM refining infrastructure, particularly in the United States and Australia, as part of broader efforts to reduce dependency on China, which currently supplies around 70% of global HPMSM output.
The coming decade will test the industry’s capacity to scale high-purity manganese production while maintaining cost competitiveness. Strategic investment, innovation in refining technologies, and greater collaboration across the supply chain will be critical in securing manganese’s role as a cornerstone of sustainable industrialisation.
Manganese also plays an essential role across several niche sectors. In agriculture, manganese sulphate is widely used in fertilisers to correct soil deficiencies, as well as in animal feed additives to support metabolic health, trends that are intensifying with the push for higher agricultural productivity. In the chemical sector, manganese compounds are utilised in water treatment, ceramic manufacturing, and the production of dry-cell batteries.
In the aerospace and automotive industries, manganese-aluminium alloys (e.g., 3000-series) are valued for their corrosion resistance and weldability. These alloys, typically containing 1–1.5% manganese, are used in fuel tanks, heat exchangers, and lightweight structural components. Manganese is also present in copper-nickel alloys deployed in desalination plants and offshore oil infrastructure, thanks to their excellent seawater corrosion resistance.
In electronics and energy storage, manganese dioxide remains critical for the performance of alkaline and zinc-carbon batteries, widely used in consumer electronics and emergency devices. Emerging uses include manganese-based supercapacitors and grid-scale storage systems, where its high ionic conductivity and affordability offer advantages over lithium-ion alternatives.
While steel remains manganese’s foundational market, the global energy transition is unlocking unprecedented demand for battery technologies. To remain resilient, market participants must address supply chain vulnerabilities through diversified sourcing, investment in refining capacity, and stronger engagement with recycling ecosystems. Regulatory frameworks such as the EU’s upcoming Battery Passport requirements will also play a defining role in shaping future production and sustainability standards.

Manganese supply
The global manganese supply chain is heavily concentrated, with a few key countries dominating both ore production and downstream processing. South Africa, Gabon, China, Australia, and India account for the majority of global manganese ore output. Africa alone holds roughly 75% of global manganese reserves.
In 2024, the market faced major disruptions that highlighted its fragility. The temporary shutdown of South32’s Groote Eylandt mine in Australia—responsible for around 15% of global high-grade supply—triggered a sharp price increase, with 44% manganese oxide rising 22% in Q2. Simultaneously, weather-related delays in Gabon and labour strikes in South Africa disrupted exports, revealing the supply chain’s sensitivity to localised events in politically and logistically complex regions.
China dominates the refining stage, controlling approximately 85% of global capacity, particularly for High-Purity Manganese Sulphate Monohydrate (HPMSM) used in lithium-ion batteries. This concentration creates strategic vulnerabilities for Western economies, especially as battery demand surges.
In response, efforts are accelerating to localise and diversify supply chains. In the United States, the Inflation Reduction Act has spurred over $2.1 billion in domestic manganese projects. Electric Metals USA is developing a facility in Minnesota targeting 50 ktpa of HPMSM by 2026. Similarly, the EU’s Critical Raw Materials Act lists manganese as a strategic resource, with an ambition to reach 50% domestic processing capacity by 2030.
Meanwhile, logistical bottlenecks persist. In Gabon, Eramet’s Moanda mine, one of the largest globally, faces export constraints due to an ageing rail network. In South Africa, chronic inefficiencies at Transnet ports have caused up to 20% shipment backlogs, straining global supply further.
Recycling offers a potential buffer. Pilot programmes in Europe and North America have shown recovery rates of up to 95% from spent batteries, though commercial scalability remains uncertain.
As demand for battery-grade manganese intensifies, securing a reliable and transparent supply will be critical. Strategic investments, infrastructure upgrades, and greater recycling capacity will be essential to reduce dependency on a small group of suppliers and to support the broader energy transition.
Manganese substitution
Manganese is challenging to substitute in many of its primary applications due to its favourable cost-performance balance, particularly in steelmaking and battery technologies. While substitution pathways exist in certain sectors, they are frequently associated with performance limitations, cost inefficiencies, or secondary supply risks. In steel production, manganese serves as a critical deoxidiser and alloying agent. Alternatives such as nickel, chromium, or molybdenum can be used in certain high-performance alloys, but these substitutes are typically more expensive, may require higher concentrations, and often lack the same versatility, increasing both material and processing costs.
In the battery sector, manganese is a key component in lithium-ion chemistries such as lithium manganese oxide (LMO) and nickel-manganese-cobalt (NMC) cathodes. While lithium iron phosphate (LFP) batteries avoid manganese entirely and offer enhanced safety and cost advantages, they generally provide lower energy density, making them less suitable for long-range electric vehicles. Solid-state battery developments may further reduce reliance on manganese, but commercial scalability remains a limiting factor.
For chemical applications, such as catalysts, pigments, and fertilisers, partial substitution with compounds of iron, copper, or cobalt is technically feasible. However, such alternatives often involve compromises in reactivity, environmental impact, or overall effectiveness.
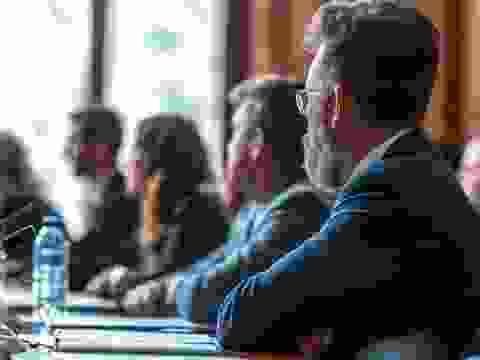
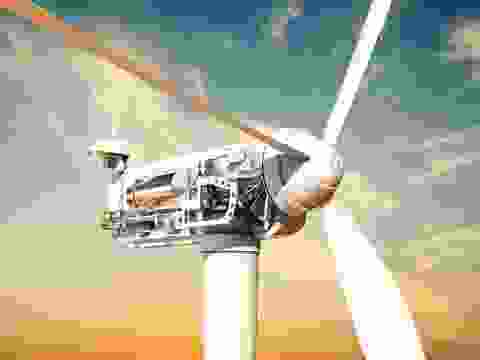
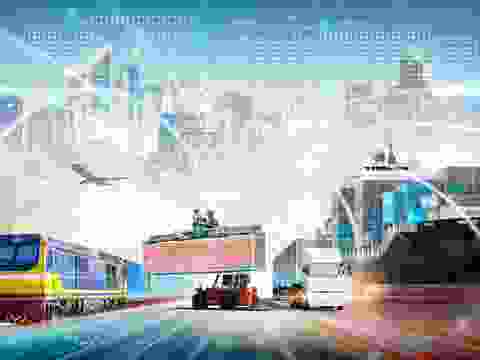
Meet the Battery Metals team
Trusted advice from a dedicated team of experts.
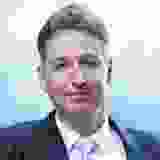
Henk de Hoop
Chief Executive Officer
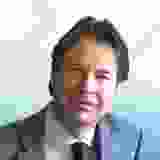
Beresford Clarke
Managing Director: Technical & Research
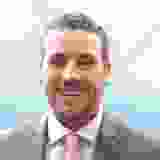
Jamie Underwood
Principal Consultant
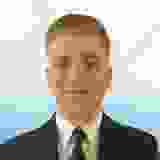
Daniel Croft
Commodity Analyst
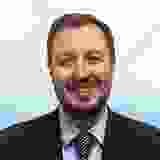
Thomas Chandler
Principal Lithium Supply Analyst
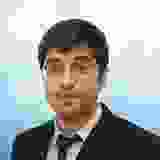
Lakshya Gupta
Senior Market Analyst: Battery Materials and Technologies
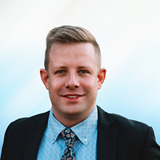
Rj Coetzee
Senior Market Analyst: Battery Materials and Technologies
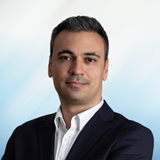
Ismet Soyocak
ESG & Critical Minerals Lead
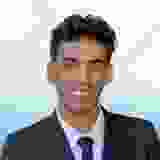
Dr Fahad Aljahdali
General Manager, KSA
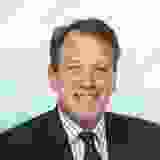
David Mobbs
Head of Marketing
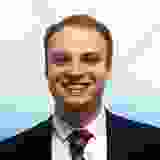
Joel Lacey
Sales and Marketing Specialist
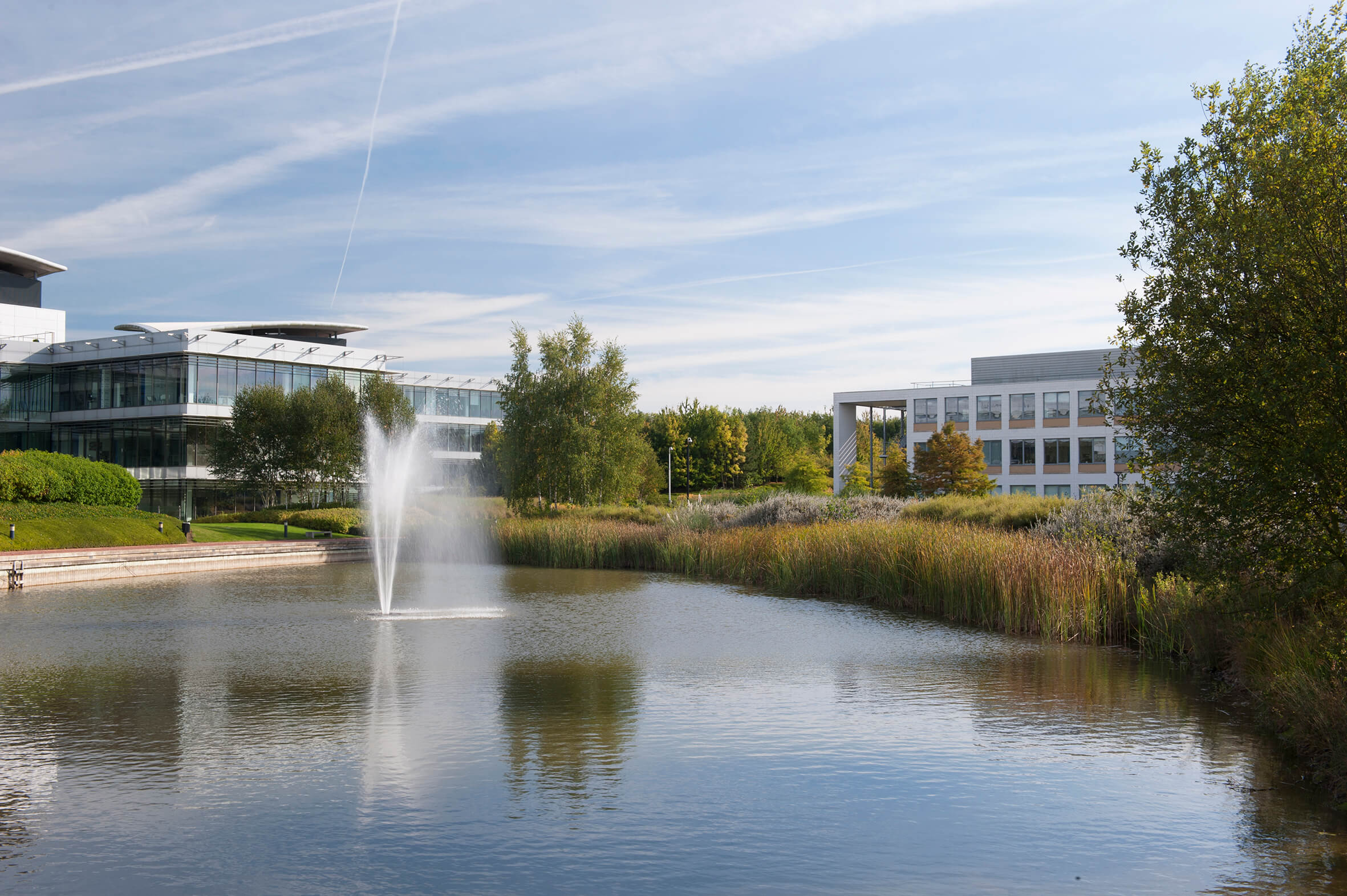
How can we help you?
SFA (Oxford) provides bespoke, independent intelligence on the strategic metal markets, specifically tailored to your needs. To find out more about what we can offer you, please contact us.