The Graphite Market
Critical Minerals and The Energy Transition
Navigating the Graphite Market
Graphite, a naturally occurring form of crystalline carbon, has long been a cornerstone material in both historical and modern technological applications. Its exceptional properties, high thermal and electrical conductivity, chemical stability, and lubricating abilities, make it indispensable across diverse industries. Traditionally valued for its role in steel production and as the core component in pencils, graphite's significance has dramatically expanded with advancements in contemporary technologies. The rise of lithium-ion batteries, fuel cells, and nuclear reactors has positioned graphite as a critical material in energy storage and generation systems. Its role is particularly vital in addressing global energy challenges, especially in the renewable energy and electric vehicle sectors, where efficiency and performance are paramount. As the world accelerates its transition towards sustainable energy solutions, graphite's strategic importance continues to grow, cementing its place at the heart of the evolving energy landscape.
An introduction to graphite
Graphite demand and end-uses
Graphite used for industrial purposes comes in two forms, natural or mined graphite and synthetic or man-made graphite. The graphite market is highly fragmented, with non-standardised feedstocks that vary in quality and impact prices.
-
Natural graphite is mined from ore deposits and provides higher energy density and lower costs to lithium-ion battery packs, but it loses capacity more quickly. However, the production process is highly inefficient and does not scale well. It currently takes 3 tonnes of flake graphite to produce 1 tonne of battery-grade graphite.
-
Synthetic graphite is produced from hydrocarbon precursors (petroleum coke), providing longevity and fast charging capabilities to lithium-ion battery packs. However, the production of synthetic graphite is expensive, energy-intensive and requires specific carbon-rich feedstocks.
Automakers can use either natural or synthetic graphite or blend them together to exploit their individual qualities. Efforts are being made to replace graphite owing to its weight, flat voltage profile, inability to accommodate high-voltage cathodes, and long-term stability as the battery ages. While many automakers have adopted silicon-enhanced graphite (<10% silicon), other materials are in development, such as silicon-carbon, silicon oxides, graphenes, silicon metal, nano-composite silicon materials, and lithium metal, but these have their unique technical hurdles to overcome.
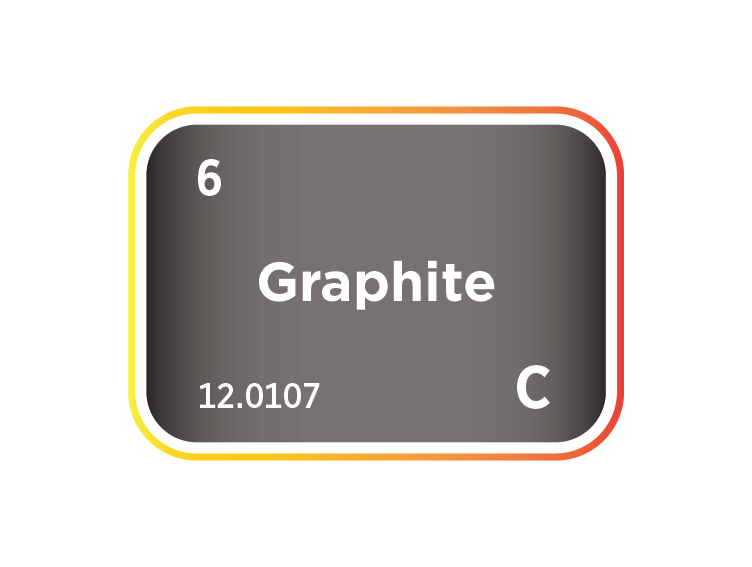
Natural graphite
Natural graphite, may seem like a ubiquitous material, but its end use depends on the textural attributes and the kind of deposit — amorphous, flake and vein graphite. For instance, Turkey may have the highest graphite reserves in the world, at 27.3% or 90 mt, mine production in 2022 was very low at 0.2% of global supply, as the deposits in the country are mostly (60%+) low-cost amorphous graphite. On the other hand, Madagascar, Mozambique and Tanzania have flake graphite deposits and have collectively increased production by 103% in 2022 from 2021 levels due to its ability to be converted into battery-grade graphite at a lower cost than amorphous due to higher yield with fewer chemicals.
-
Amorphous graphite (low cost, low purity). This is the most abundant and cost-effective graphite as it is easy to extract and process, but it is a low-grade form containing 60% carbon and would cost more to produce the purity needed for graphite. Furthermore, unlike flake graphite, amorphous graphite cannot be upgraded through flotation or purification, and is therefore used to increase the strength and durability of steel, brake linings, clutch materials, gaskets and pencil lead.
-
Flake graphite (cost depends on size, quality and impurities). This is the most widely used form and contains 80-98% carbon, depending on the flake size and morphology. Jumbo (300 μm+) and large (180-300 μm) sized flakes are typically reserved for refractory and nuclear applications, while medium-sized flakes (150-180 μm) are used to make the battery-grade form necessary for EV batteries. No two deposits are alike, and therefore producers must go through extensive quality control assessments to gain offtake agreements.
-
Vein graphite (high cost, high purity). Containing 95-99% carbon, this high-priced form of graphite is commercially extracted only in Sri Lanka. This form can be easily combined with other materials and used in refractories, ceramics, carbon brushes, lubricants and steelmaking. Owing to its conductivity, it is also the preferred material for electrical applications.
Flake graphite is the primary type used to produce battery-grade graphite, however, the current practices to produce battery-grade graphite are largely inefficient and environmentally unfriendly. The production of all forms of graphite for batteries is dominated by China — 65% of global mined graphite production and all refining is in China using methods that are increasingly under scrutiny.
Both natural and synthetic graphite have technical constraints, but synthetic graphite has a lengthier and more carbon-intensive production process. The quality of natural flake graphite is inconsistent as deposits can differ greatly, and there can be a significant yield loss if particles are too fine to go through the spheroidisation step. However, it takes up to 4-5 months to attain the crystallisation necessary to produce artificial graphite versus 3-5 days for natural graphite, resulting in the significant price discrepancy seen between the two forms.
Natural graphite supply
China controlled an estimated 65% of natural graphite mine production in 2022 at 850 kt, and all of the refining. Commercial-scale graphite mining has moved from the eastern province of Shandong to the northeastern province of Heilongjiang and the north Inner Mongolia region due to a depletion of ore reserves and the negative impact of environmentally unsound practices on surrounding communities. The ores are fine flake (60%) and amorphous (40%), with a substantial volume of particulate emissions from the grinding and acid processes. Consequently, the central government has directed industry consolidation and introduced inspections at all levels of the value chain. As a result of these initiatives, the world’s largest anode material producers, Shenzhen BTR New Energy Materials, has integrated its operations upstream.
Africa has increased its mine production dramatically over the past two years. Mine production in Mozambique has more than doubled to 170 kt and in Madagascar it has risen by 57% to 110 kt. In addition, Tanzania had no mine production in 2021, but 8 kt in 2022 and this is expected to grow substantially over the next five years. Mozambique (25 mt of reserves), Madagascar (26 mt of reserves) and Tanzania (18 mt of reserves).
The US and Europe are 100% dependent on the import of natural graphite and with the Chinese government restricting exports, they need to develop domestic resources. Since the Chinese government is now requiring graphite producers to hold licences to ship high-grade graphite materials out of the country, the US and Europe will need to develop domestic assets to reduce supply risks. Graphite mine production in the US ceased in 1994 but now a few companies are developing mine assets, especially in Alaska and the Alabama graphite belt. Canada has about 5.7 million tonnes of graphite reserves and the only operating mine in North America and could be the primary supplier to the US given its FTA status and benefits received under the IRA.
Finally, the European Commission published a critical mineral study on graphite to increase domestic output and flake deposits in Czechia, Finland, Germany, Sweden and Norway are being assessed for development or expansion.
Synthetic graphite supply
Needle coke is the precursor material needed to produce synthetic graphite and is typically derived from petroleum coke or coal-tar pitch from the gas and coal industries. Although both are by-products of well-established industrial processes, the production of needle coke is an energy-intensive process that lacks the necessary efficiency. In addition, only 5% of petroleum coke feedstock meets the high purity and structural specifications to produce synthetic graphite. The processes used to manufacture synthetic graphite are varied and complex, and standardisation may not be possible.
-
Petroleum coke is the leftover residue from the coking process used in the oil-refining industry. Needle coke is typically produced from petroleum coke derived from decanted heavy gasoil of catalytic cracking, heavy pyrolysis resin, and highly fragranced low-sulphur petroleum. Not surprisingly, the US accounts for more than 40% of petroleum coke production globally, though there is a lack of industry coordination among the raw material producers, intermediate producers and the battery industry.
-
Petroleum coke is the primary precursor material used in the US and needs to be specified before the production process to ensure it results in high-quality graphite, as the by-products of crude oil streams can differ significantly in quality. Therefore, synthetic graphite is produced only from the highest-grade crude oils that are high in aromatic organics content and these can be difficult to obtain.
-
Many petroleum refineries do not have the delayed coker units required. There are also some technical constraints that must be overcome, as the initial petroleum coke product is a solid, non-melting carbon that contains a number of volatile organic compounds that must be removed or turned into calcined petroleum coke, typically by a rotary kiln. GrafTech is the leading company that produces needle coke from petroleum coke to produce graphite electrodes for electric arc furnaces.
-
Coal-tar pitch is the residue from the distillation of coal tar – a by-product of the coking, liquefaction, or gasification of coal. Only three companies in the world outside of China produce needle coke from coal-tar pitch: Mitsubishi, the first company to successfully produce coal-based needle coke, C-Chem and POSCO Chemicals.
The Battery Metals market
SFA (Oxford) also provides regular market intelligence on the battery metal markets. Discover some of the critical materials used in batteries.
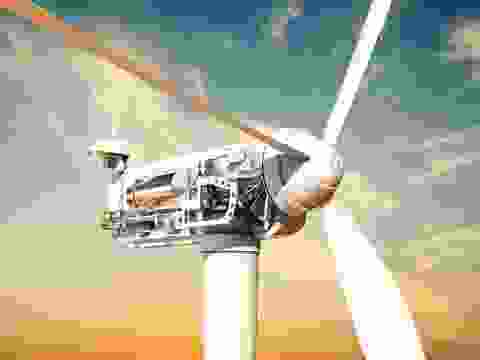
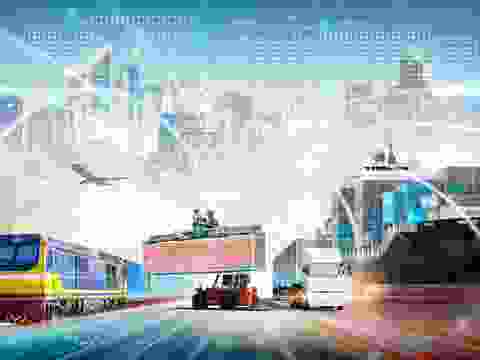
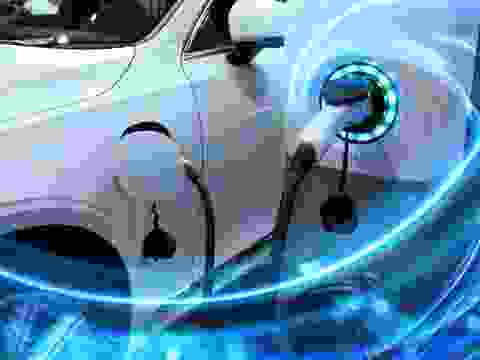
Meet the Critical Minerals team
Trusted advice from a dedicated team of experts.
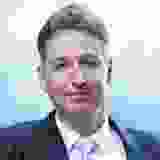
Henk de Hoop
Chief Executive Officer
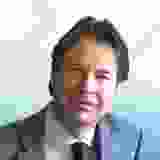
Beresford Clarke
Managing Director: Technical & Research
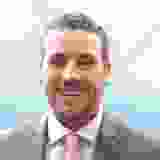
Jamie Underwood
Principal Consultant
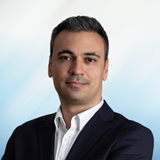
Ismet Soyocak
ESG & Critical Minerals Lead
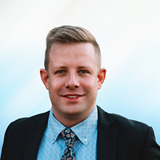
Rj Coetzee
Senior Market Analyst: Battery Materials and Technologies
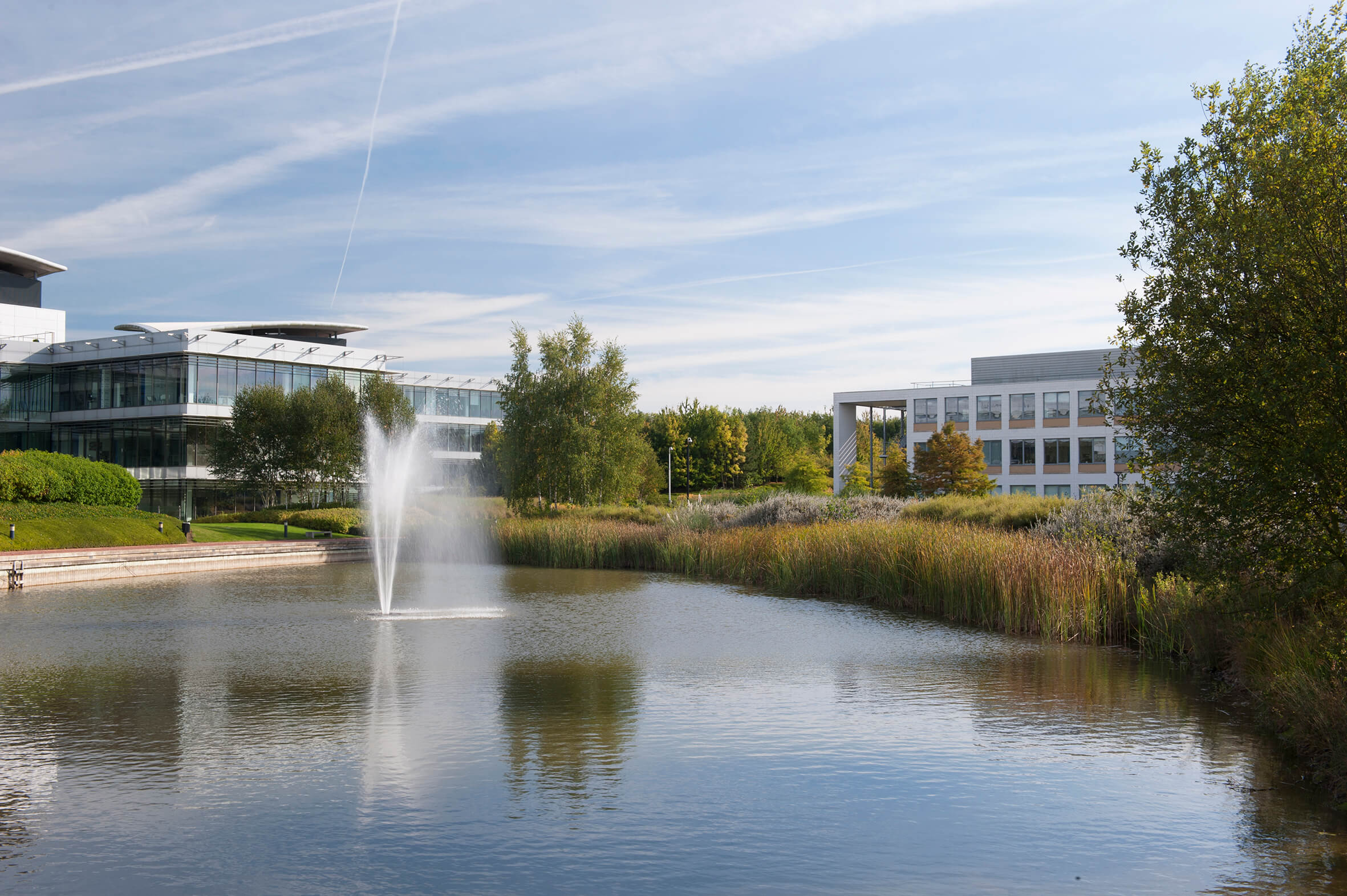
How can we help you?
SFA (Oxford) provides bespoke, independent intelligence on the strategic metal markets, specifically tailored to your needs. To find out more about what we can offer you, please contact us.