Aluminium
Critical Minerals and The Energy Transition
Navigating the Aluminium Market
Aluminium is one of the most important industrial metals of the 21st century, playing a critical role in the energy transition and the shift toward more sustainable global infrastructure. As a lightweight, corrosion-resistant, and endlessly recyclable material, aluminium supports a wide range of low-carbon technologies—from electric vehicles and solar photovoltaics to modern power grids and green buildings. Its versatility, performance, and circularity make it indispensable to both traditional industries and emerging clean energy systems. Global demand for aluminium is rising rapidly, driven by decarbonisation policies, vehicle electrification, renewable energy deployment, and the growth of sustainable packaging. This demand is not only reshaping markets but also prompting major shifts in supply chains, production methods, and recycling practices. At the same time, the aluminium industry faces the challenge of decarbonising its own energy-intensive processes, particularly in bauxite mining, alumina refining, and aluminium smelting.
An introduction to aluminium
Aluminium demand and end-uses
The global aluminium market is undergoing a significant transformation, driven by rising demand across a range of sectors—most notably those linked to the clean energy transition. As a lightweight, corrosion-resistant and infinitely recyclable material, aluminium plays a pivotal role in supporting a low-carbon future. It enables sustainable technologies such as electric vehicles, renewable energy systems, and energy-efficient buildings, while also confronting the challenge of decarbonising its own production.
This surge in demand is not evenly distributed across regions. The bulk of growth is expected to come from China and the wider Asia-Pacific region, with North America and Europe also playing notable roles. Together, these regions account for the vast majority of projected increases, reflecting differing stages of industrial development and clean energy uptake.
The transport sector is anticipated to be the primary driver of future aluminium demand. The move away from fossil fuel-powered vehicles towards electric vehicles (EVs) is having a profound impact on material requirements. Aluminium’s high strength-to-weight ratio makes it an ideal material for electric mobility, helping reduce vehicle weight, extend driving range and boost energy efficiency. Modern EVs, including light commercial vehicles and high-end sedans, increasingly rely on aluminium for their structural integrity and performance.
Geographically, China is expected to lead growth in aluminium demand from the transport sector, followed by North America and Europe. This reflects both government policies encouraging vehicle electrification and the scale of automotive production in these regions.
Beyond transport, the electrical sector represents the second-largest growth area for aluminium. Demand is being driven by the rapid expansion of renewable energy infrastructure. Aluminium is essential in solar energy systems, forming the backbone of solar panel frames and support structures. Industry experts have emphasised that solar power would not be viable at scale without aluminium, which constitutes the majority of photovoltaic system components. As global solar capacity continues to expand, aluminium will remain a critical material for enabling that growth.
The construction sector also remains a major consumer of aluminium, albeit with more modest growth projections. Its strength, resistance to corrosion, and long service life make it a preferred choice for a wide range of applications—from modern high-rise buildings to smart urban infrastructure. Despite slower growth rates, construction will continue to represent a significant share of overall aluminium use.
Another important area of demand is the packaging industry. In certain regions, such as North America, the packaging sector consumes more aluminium than construction due to the widespread use of aluminium in beverage cans, food containers, and sustainable packaging alternatives. Aluminium’s protective properties and recyclability make it highly suited to modern packaging needs.
In the context of the energy transition, aluminium’s role extends far beyond traditional applications. In solar power, it is used extensively in both photovoltaic and concentrating solar power systems, with the latter requiring even greater quantities per unit of energy generated. This has led to a steep rise in consumption from the solar industry over recent years.
Electric vehicles not only increase the amount of aluminium used per vehicle but also change how the metal is integrated into transport systems. Its lightweight properties help offset the added weight of EV batteries, thereby improving performance and efficiency. As EV production scales up, aluminium will become even more embedded in vehicle design and manufacturing.
Aluminium is increasingly used in power infrastructure, particularly in electricity transmission and smart grid systems. Its conductivity and cost-effectiveness make it a viable alternative to copper in power lines and connectors. Aluminium also plays a supporting role in energy storage technologies and hydrogen production, particularly in experimental systems where it reacts with water to produce hydrogen in an emissions-free process.
However, while aluminium is vital to enabling green technologies, its production is one of the most energy-intensive industrial activities. The sector contributes a sizeable share of global industrial greenhouse gas emissions, with the majority arising from the energy used in refining alumina and smelting aluminium. This presents a significant challenge: how to align aluminium production with climate goals while still meeting rising global demand.
To address this, the aluminium industry is embracing a range of green initiatives. Key among these are efforts to decarbonise the production process through the use of cleaner energy sources, the development of low-emission smelting technologies, and a greater emphasis on recycling. Recycled aluminium, or secondary production, requires only a fraction of the energy used in primary production and produces far fewer emissions. As a result, recycling is expected to form an ever-larger share of global aluminium supply.
This shift to circular economy principles is already making a measurable impact. A significant proportion of all aluminium ever produced is still in use today, underscoring its recyclability and value retention. By expanding recycling infrastructure and improving material efficiency, the industry aims to reduce its carbon footprint while meeting the needs of an energy-hungry future.
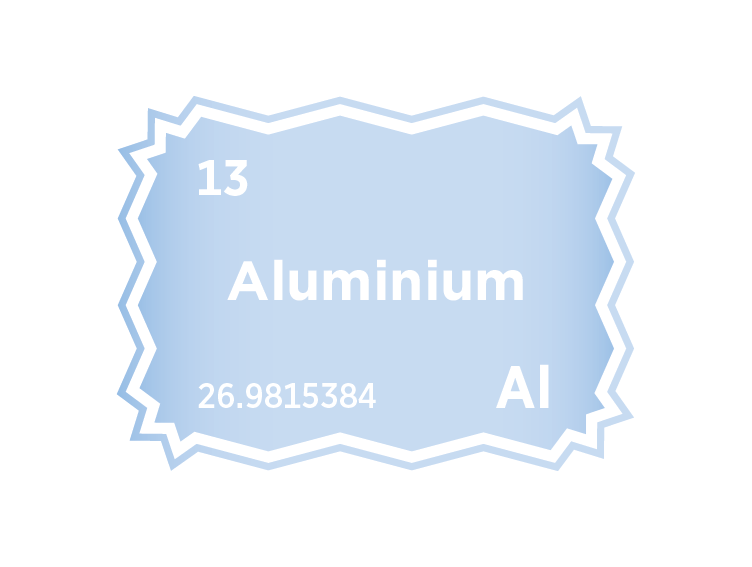
Aluminium and the Energy Transition
Aluminium supply
The aluminium supply chain is a complex, vertically integrated system that begins with the extraction of bauxite ore and progresses through several key stages: alumina refining, primary aluminium smelting, and downstream fabrication. Each stage involves different technical processes and is often concentrated in specific countries, reflecting variations in resource endowment, energy availability, and industrial capacity. The process is both energy-intensive and globally dispersed, with some countries specialising in raw material extraction and others dominating value-added production.
Bauxite mining is the first step in the supply chain. Bauxite, the primary ore for aluminium, is typically extracted via open-pit mining and contains high concentrations of alumina-bearing minerals such as gibbsite, boehmite, and diaspore. The largest producers of bauxite include Australia and Guinea, which together account for a significant share of global supply. Other major bauxite-producing countries include China, Brazil, India, Indonesia, and Russia. These nations benefit from extensive reserves and favourable mining conditions. Additional producers such as Jamaica, Vietnam, and Saudi Arabia also contribute meaningfully to the global market.
Once extracted, bauxite is processed into alumina (aluminium oxide) through the Bayer Process, which involves dissolving the ore in caustic soda at high temperatures to separate alumina from impurities such as iron oxides and silica. This stage is typically co-located with bauxite mining, although international shipments of bauxite also support alumina refineries in regions with less domestic ore. The leading alumina producers include China and Australia, followed by Brazil, India, and Russia. Other key producers are the United Arab Emirates, Saudi Arabia, Ireland, Spain, and Vietnam, each playing a role in refining capacity at regional or global levels.
The next stage, aluminium smelting, involves converting alumina into metallic aluminium through electrolytic reduction—most commonly using the Hall–Héroult process. This step is extremely energy-intensive, making access to affordable electricity a critical factor in determining smelter locations. China is by far the largest producer of primary aluminium, followed by Russia, India, and Canada. The United Arab Emirates, Bahrain, Australia, and Norway also host large-scale smelting operations, often leveraging hydroelectric or fossil fuel-based energy sources. Other contributing nations include the United States, Malaysia, Brazil, South Africa, Saudi Arabia, and Iceland, with additional capacity distributed across Europe, Central Asia, and parts of Africa.
Secondary aluminium production, or recycling, plays an increasingly important role in the supply chain. It requires only a fraction of the energy used in primary production and has far lower carbon emissions. Secondary aluminium is sourced from post-consumer waste (such as used beverage cans and automotive scrap) and post-industrial offcuts. Many industrialised countries have established strong recycling infrastructure, with the United States, European Union members, China, and Japan all actively promoting closed-loop recycling systems to reduce reliance on primary smelting.
The final stage of the supply chain is downstream fabrication, where aluminium is cast, rolled, extruded, or otherwise processed into semi-finished and finished goods. These include products for use in transport, construction, packaging, electrical systems, aerospace, and consumer electronics.
Aluminium substitution
Aluminium is a highly versatile material, widely used across industries due to its lightweight, corrosion resistance, strength, and recyclability. However, it does not exist in isolation, its use often depends on trade-offs between performance, cost, and sustainability. In some cases, aluminium competes directly with alternative materials that may be better suited to specific applications.
In the construction and automotive industries, steel remains a common substitute where weight is less of a concern and cost competitiveness is a priority. Steel’s durability and strength make it ideal for structural components, particularly in buildings and heavy-duty vehicles. In the packaging sector, plastics are frequently used in place of aluminium, especially in products where formability, lightweighting, and corrosion resistance are valued, although environmental concerns around plastic waste have begun to shift preferences in favour of more recyclable materials like aluminium.
Copper, known for its excellent conductivity, is often preferred in electrical applications such as wiring and transformers, although aluminium is used as a cost-effective and lighter-weight alternative in power transmission. In more advanced sectors, such as aerospace and high-performance automotive manufacturing, composites and carbon fibre materials are being adopted in place of aluminium due to their exceptional strength-to-weight ratios, despite being significantly more expensive.
Conversely, aluminium has increasingly replaced other materials in numerous applications. In both the automotive and aerospace industries, it is favoured over steel due to its lighter weight, which contributes to improved fuel efficiency and reduced emissions. In electrical systems, aluminium has gradually substituted for copper in many applications, particularly in overhead power lines, because of its lower cost, lighter weight, and adequate conductivity. Its corrosion resistance and recyclability further enhance aluminium’s appeal, especially in sectors striving to reduce their environmental impact and embrace circular economy principles.
Current bauxite and refractory bauxite producers
Historic bauxite producers
Primary aluminum producers
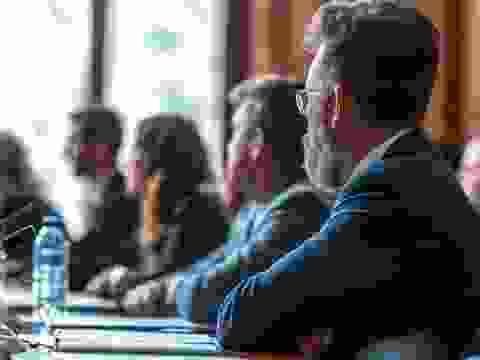
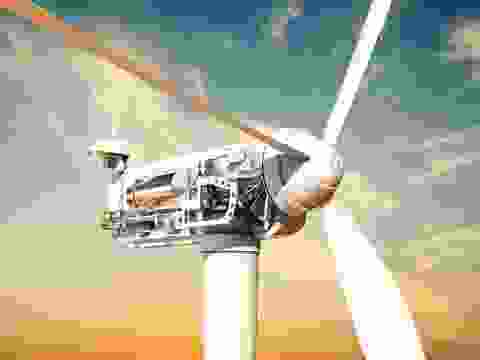
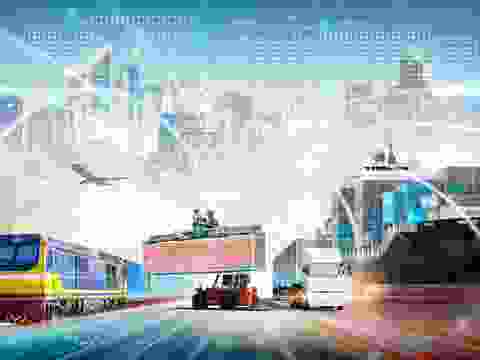
Meet the Critical Minerals team
Trusted advice from a dedicated team of experts.
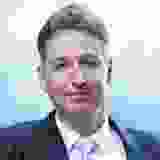
Henk de Hoop
Chief Executive Officer
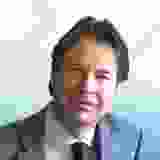
Beresford Clarke
Managing Director: Technical & Research
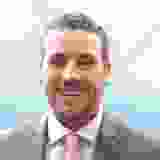
Jamie Underwood
Principal Consultant
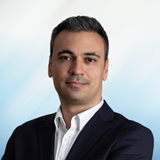
Ismet Soyocak
ESG & Critical Minerals Lead
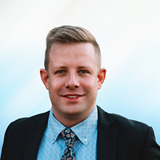
Rj Coetzee
Senior Market Analyst: Battery Materials and Technologies
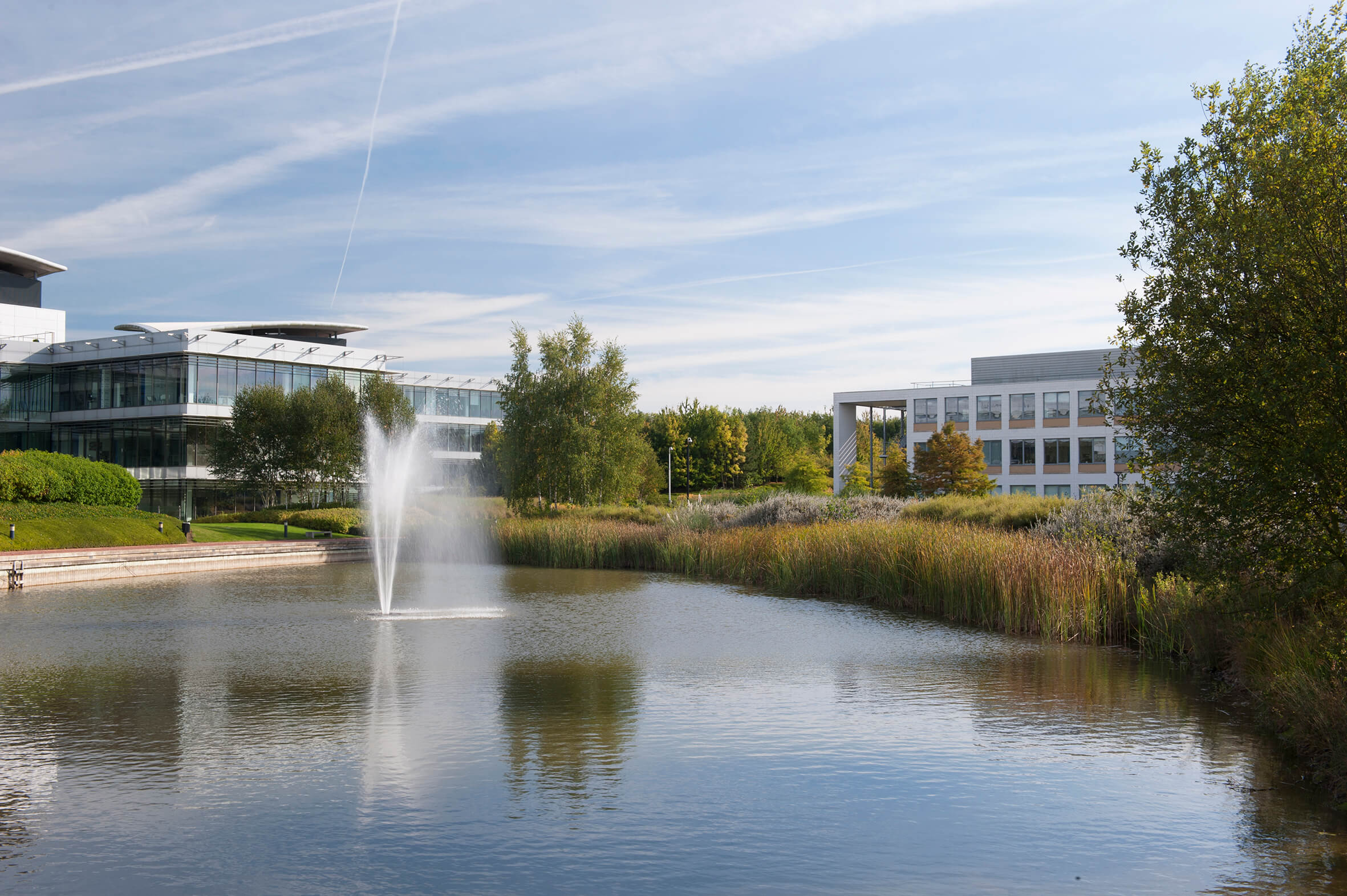
How can we help you?
SFA (Oxford) provides bespoke, independent intelligence on the strategic metal markets, specifically tailored to your needs. To find out more about what we can offer you, please contact us.